
Lame in carburo di tungsteno offer exceptional accuracy and strength for cutting jobs that demand the best tools. Their durable blend of tungsten carbide and other metals ensures they last much longer than regular steel blades, making them a top choice for tasks where toughness is crucial. In 2024, these blades accounted for 12% of the global industrial cutting tool market, with more than half of factories opting for carbide blades due to their superior performance. You’ll find these blades used in automotive shops, airplane factories, woodworking facilities, and packaging lines. If you need a lama personalizzata for a specific job, selecting the right material is key to achieving excellent results and extending the blade’s lifespan.
Punti chiave
- Tungsten carbide blades are very hard and sharp. They stay sharp much longer than steel blades. This makes them great for cutting tough things. They are good for jobs that need careful cutting.
- These blades do not wear out fast. They can handle heat and do not rust. This helps them last longer. They work well in tough places like factories and food plants.
- You can make custom tungsten carbide blades for special jobs. This helps you cut more accurately. It also saves money and makes less waste.
- You need to sharpen these blades with diamond tools. Taking care of them often keeps them working well. This also helps them last longer.
- Nanjing Metal makes custom blades for many needs. They use good materials and new ways to make blades. Their blades work for many kinds of factories.
Tungsten Carbide Blades Overview
What Are Tungsten Carbide Blades
You might ask what makes lame in carburo di tungsteno different from other cutting tools. These blades are made with a special material called carburo di tungsteno. This material mixes carburo di tungsteno grains and a cobalt binder. The mix makes the blades very hard and tough. On the Mohs scale, carburo di tungsteno gets a 9. Only diamonds and a few other things are harder than that.
Lame in carburo di tungsteno do not wear out fast. They keep their sharp edge much longer than steel blades. You can use them for hard jobs where other blades break. These blades work well in high heat and with rough materials. They do not lose their shape or sharpness. If you test them, you may feel a small magnetic pull. They do not rust like iron-based steels. This makes them easy to spot. They are great for places with water or chemicals.
Mancia: If you want a blade that stays sharp and lasts long, lame in carburo di tungsteno are a good pick for woodworking, mining, aerospace, and many other jobs.
Tungsten Carbide Blade vs. Steel Blade
When you look at a tungsten carbide blade and a steel blade, you see big differences. The table below shows how they compare:
Aspetto | Lame in Carburo di Tungsteno | Lame in acciaio |
---|---|---|
Durezza | Extremely hard; ranks very high on Mohs scale | Less hard; dulls faster under heavy use |
Resistenza all'usura | Maintains sharp edge much longer; lasts up to 100x longer | Wears down quickly; requires frequent sharpening |
Efficienza di taglio | Higher due to sustained sharpness and precision | Lower due to faster edge dulling |
Impact Resistance | More brittle; less impact-resistant | More ductile; better at absorbing shocks |
Longevità | Significantly longer lifespan in abrasive conditions | Shorter lifespan; frequent replacements needed |
Costo | Higher upfront cost but better long-term value | Lower initial cost but higher maintenance costs |
Applicazioni ideali | Precision cutting, industrial use, metalworking, packaging | High-impact or shock-loading scenarios |
Lame in carburo di tungsteno stay sharp much longer than steel blades. You will not need to sharpen or replace them as often. They also make cleaner and more exact cuts. Steel blades cost less at first and can handle hard hits better. They bend more and do not break as easily. If you need a cheaper blade or work with lots of shocks, steel blades might be better. But for most jobs that need clean cuts, lame in carburo di tungsteno work best and last longer.
Nota: Lame in carburo di tungsteno may cost more at first, but they save you money in the long run because they last longer and cut better.
Material and Properties

Tungsten Carbide and Cobalt Composition
Typical Composition Ratios
Most industrial blades use a mix of tungsten carbide and cobalt. The cobalt amount is usually between 6% and 20% by weight. This range helps the blade stay hard, tough, and last longer. For example:
- YG6 grade blades have about 6% cobalt. These blades are very hard and resist wearing out, so they are good for cutting tools.
- YG15 grade blades have about 15% cobalt. These blades are tougher and can take more hits, which is important for heavy-duty tools.
The rest of the blade, between 70% and 97%, is tungsten carbide. If you want a blade that stays sharp longer, pick one with more tungsten carbide. If you need a blade that can handle more shock, choose one with more cobalt.
Role of Cobalt as a Binder
Cobalt works as a binder in these blades. It holds the tungsten carbide grains together. More cobalt makes the blade tougher and less likely to break. But the blade will be a bit softer. Less cobalt makes the blade harder but also more brittle. This means it can chip more easily if you use it for tough jobs. Most companies use between 6% and 15% cobalt to get the best mix of hardness and toughness. This balance helps the blade last longer in hard jobs like metalworking and mining.
Hardness and Abrasion Resistance
Hardness Comparison with High Carbon Steel
Tungsten carbide blades are known for being very hard. You can see this in the numbers. The Vickers hardness for tungsten carbide is between 1100 and 2600 HV, depending on the grade. High carbon steel usually has a Vickers hardness below 1000 HV. The table below shows how different grades compare:
Material/Grade | Rockwell Hardness (HRA/HRC) | Vickers Hardness (HV) |
---|---|---|
YG6 (Tungsten Carbide) | 90.5 HRA | 1450 |
YG15 (Tungsten Carbide) | 86.0 HRA | 1100 |
G10 (Tungsten Carbide) | 93.0 HRA | 1650 |
Acciaio ad alto tenore di carbonio | 60 HRC (approx.) | <1000 |
You can also see a chart below:

Wear Resistance in Demanding Applications
Tungsten carbide blades have high hardness and wear resistance. This means they keep their edges sharp much longer than steel blades. In factories, these blades can last 300% to 500% longer than regular steel blades. Their special structure helps them resist bending and edge wear, even at high speeds or for long times. For example, in paper or textile factories, you can use a tungsten carbide blade for months before sharpening. This saves time and money on repairs. The fine grain size and the right amount of cobalt help the blade resist chipping and keep cutting well.
Mancia: If you want a blade that can cut tough, rough materials and keep its edge, pick one with high hardness and wear resistance.
Heat Resistance and Edge Retention
Performance at Elevated Temperatures
Tungsten carbide blades work well even at high temperatures. You can use them for cutting when it gets up to 900°C or even 1000°C. The blade keeps its hardness and does not lose its shape or sharpness. This makes it great for jobs that get very hot, like metal cutting or machining.
Edge Retention in Continuous Use
Edge retention is a big reason to pick lame in carburo di tungsteno. These blades can keep their edges sharp up to 10 times longer than most other knife materials. Even if you use them all the time, you will not need to sharpen them often. Some people use the same blade for months without sharpening. This high edge retention comes from the blade’s great hardness and wear resistance. But remember, these blades are more brittle than steel. They work best for straight cutting and slicing, not for prying or twisting. You need special diamond stones to sharpen them, but you will not need to do this often.
Nota: If you need a blade for lots of use and want to avoid sharpening, tungsten carbide blades give the best edge retention and long-lasting performance.
Benefits of Tungsten Carbide Knives
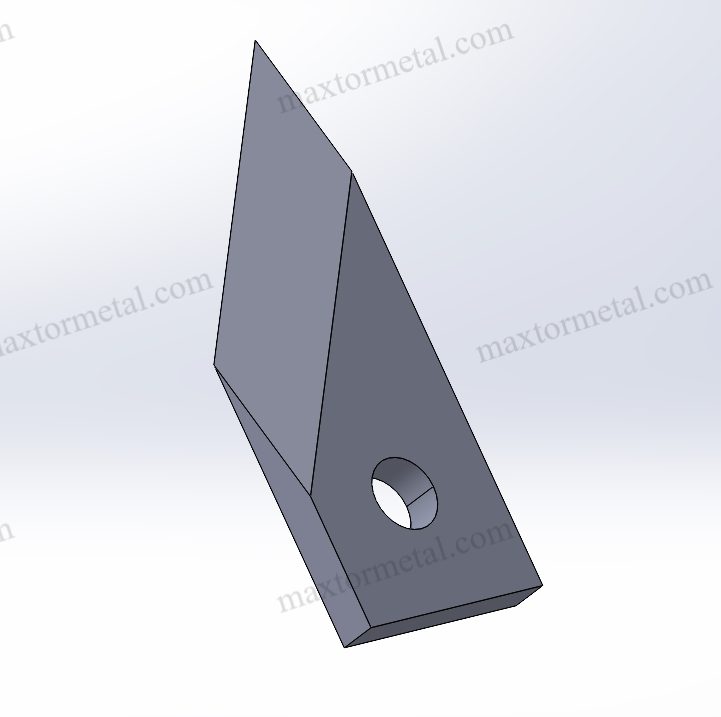
Durability and Longevity
Exceptional Wear Resistance
If you pick tungsten carbide knives, you get a knife that stays sharp much longer than most other types. These knives are very hard, so you do not need to sharpen them often. You can use them for tough jobs, like cutting metal or rough materials, and they still work well. Their edges stay sharp, so you get great cutting and do not have to stop for maintenance as much.
Corrosion Resistance in Harsh Environments
Tungsten carbide knives work well in places with water, chemicals, or heat. Tungsten does not rust, and when it is part of tungsten carbide, the knife gets even stronger. The blade forms a special layer that keeps it safe from damage. This means your knife stays sharp and strong, even in wet or acidic places. You do not have to worry about the blade getting weak or rusty. This toughness saves you money because you do not need new knives as often, and your knife keeps working well in hard jobs.
Mancia: If you work in a factory or workshop with tough conditions, tungsten carbide knives will keep their edges sharp and ready to use.
Real-World Lifespan in Metalworking
You will see that tungsten carbide knives last much longer than high-speed steel blades. In metalworking, these knives can last three times as long. For example, one company used to change blades 12 times a year, but with tungsten carbide, they only changed them 4 times. This means you spend less time stopping work and less money on repairs. These knives are very hard (88-92 HRC) and can handle heat up to 2000°F (1090°C). They keep their edges sharp, even when you use them a lot. This makes your work faster and saves you money.
Precision Cutting Performance
Superior Cutting Accuracy
Tungsten carbide knives help you cut with great accuracy. Their sharp edges last a long time, even after many uses. You can cut hard things like stainless steel and strong alloys without losing precision. Because these knives are hard and resist wearing out, you get smooth cuts and tight fits. Your finished work will look better.
- Tungsten carbide is the hardest material for roll shear blades.
- It keeps its sharpness and shape under heavy use.
- It does not bend or warp from heat during long jobs.
- It does not rust, so it lasts longer and works well.
- Special machines, like CNC, help make the blade shape perfect.
Comparison with High Carbon Steel Blades
When you look at tungsten carbide knives and high carbon steel blades, you see big differences. High carbon steel blades start sharp but get dull fast and need to be replaced often. Tungsten carbide knives keep their edges much longer. They do not wear out, get hot, or rust as quickly, so you spend more time working and less time changing blades. Tungsten carbide blades also cut tougher things better.
Caratteristica | Tungsten Carbide Knives | Lame in acciaio ad alto tenore di carbonio |
---|---|---|
Durezza | 5x harder than steel | Good, but dulls faster |
Mantenimento del bordo | Extreme edge retention | Necessita di affilatura frequente |
Resistenza all'usura | Eccellente | Moderare |
Resistenza alla corrosione | Alto | Basso |
Cutting Power | Superior | Inferiore |
Durata | Long life | Shorter lifespan |
Advantages in Electronics Manufacturing
In electronics factories, you need knives that make clean, exact cuts every time. Tungsten carbide knives are great for this. Their hardness and strength mean you get fewer rough edges and waste less material—up to 15% less than with high carbon steel blades. Some blades have special coatings, like Titanium Carbonitride (TiCN), to stop things from sticking to the blade. This helps you get smoother cuts and better battery parts. You also do not have to fix or change the knives as often, so you save time. This means you make more products and have fewer stops.
- High hardness gives better cuts and less waste.
- Long blade life helps you work up to 30% faster.
- Picking the right blade stops chipping and helps with rough materials.
Nota: If you want a knife that is really tough, lasts a long time, and cuts well, tungsten carbide knives are the best for hard jobs that need careful cutting.
Applications of Carbide Cutting Tools
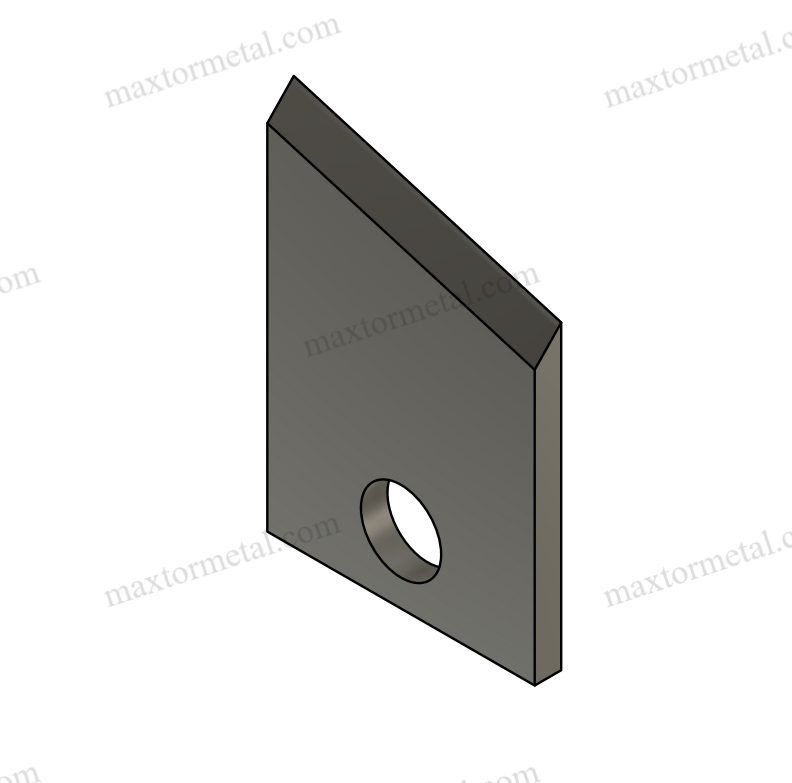
Tungsten carbide knives and blades are used in many industries. They are important where you need precision, strength, and speed. These cutting tools can handle hard jobs and work well in tough places. Let’s see how they are used in different jobs.
Industrial Tungsten Carbide Blade Uses
Manufacturing Industry Applications
You see industrial tungsten carbide blade solutions in many factories. These blades help cut, trim, and shape things with great accuracy. Here are some ways they are used:
- Metalworking: You use tungsten carbide blades for cutting, milling, drilling, turning, and reaming. These jobs shape metals like steel, aluminum, and titanium.
- Automated production lines: These blades give you steady quality and fast work.
- Aerospace and automotive: You use carbide cutting tools to make engine parts and airplane pieces that need exact cuts and strong edges.
Making these blades takes careful planning and picking the right materials. You get blades that stay sharp, do not wear out fast, and last longer than steel blades.
Food Processing Industry Applications
In food processing, you need blades that are safe and clean. Tungsten carbide knives give you many good things:
- They follow FDA and EU rules, so you know they are safe.
- Their hardness and toughness mean you change blades less, saving time and money.
- Corrosion-resistant grades let you use strong cleaners without hurting the blade.
- You get sharp, neat cuts for meat, bread, and vegetables, so your food looks good and stays the same.
Mancia: Using tungsten carbide knives in food plants helps you work faster and stop less. Their long life and sharpness make them a smart buy for any food factory.
Belt Cleaning and Conveyor Maintenance
Mining and moving big loads need good belt cleaning. Industrial tungsten carbide blade scrapers clean sticky stuff off conveyor belts. You get:
- Great cleaning with light pressure, which keeps belts safe.
- Less mess and spills, so your work area is safer.
- Little upkeep—often just one tightening for the blade’s life.
- Long-lasting use, even with rough materials.
Carbide-tipped blades help keep conveyor belts working well. You spend less time fixing things and more time moving stuff.
Woodworking Applications
Precision Saw Blades for Fine Carpentry
Carbide saw blades are loved by woodworkers. You get smooth, clean cuts and do not need to sand as much. Here’s why:
- Strong, heat-resistant tips stay sharp longer than steel.
- High tooth counts (60 to 80 teeth) give smooth finishes.
- Special tooth shapes, like alternating top bevel (ATB), stop splinters.
- You can cut hardwoods and plywood without rough edges.
Caratteristica | Advantage for Woodworking Precision |
---|---|
Durata | Blades last longer and need fewer replacements |
Nitidezza | Cleaner, more precise cuts |
Resistenza al calore | No warping during high-speed cutting |
Reduced Vibration | Smoother, more stable cuts |
Tagli più puliti | Professional-quality finishes |
Versatilità | Cuts many wood types with less splintering |
Industrial Planer and Joiner Knives
You use tungsten carbide knives in planers and joiners to make wood flat and even. These knives help you:
- Remove rough spots and defects fast, making wood better.
- Work quicker and save effort because the knives stay sharp.
- Stop less for blade changes, so you save time.
- Keep your line running, even during long, hard jobs.
Nota: If you want smooth, top-quality wood, tungsten carbide knives are the best for your shop.
Applicazioni di taglio Metal
Sheet Metal Slitting and Shearing
Jobs like cutting sheet metal need strong blades. Tungsten carbide blades give you:
- Great hardness for fast cutting of steel, aluminum, and copper.
- Sharp, tough edges that stay good for a long time.
- Smooth, flat cuts with very close accuracy.
- Lama personalizzata shapes and coatings for different needs.
Feature/Aspect | Descrizione |
---|---|
Durezza | Keeps sharpness during long cutting jobs |
Cutting Performance | Great for metal coils, sheets, and strips |
Resistenza all'usura | Fewer blade changes and less stopping |
Shear Force Reduction | Protects both blade and machine |
Precision & Repeatability | Gives steady, high-quality cuts |
Geometria della lama | Custom shapes for different materials |
Blade Coatings | Extra hardness and stops rust |
Applicazioni | Used in appliances, building, hardware, packaging, automotive |
Tube and Pipe Cutting in Heavy Industry
Heavy industry uses tungsten carbide blades to cut tubes and pipes. You get cuts on steel with no rough edges, so you do not need to fix them much. The tungsten carbide coating makes the blade last 4 to 10 times longer than normal blades. You spend less time changing blades and more time making good parts. This helps you save money and make more products.
Richiamo: When you pick carbide cutting tools for hard jobs, you get blades that last longer, cut better, and help you work faster. These tools help you do well in today’s busy factories.
Custom Industrial Tungsten Carbide Blade Solutions
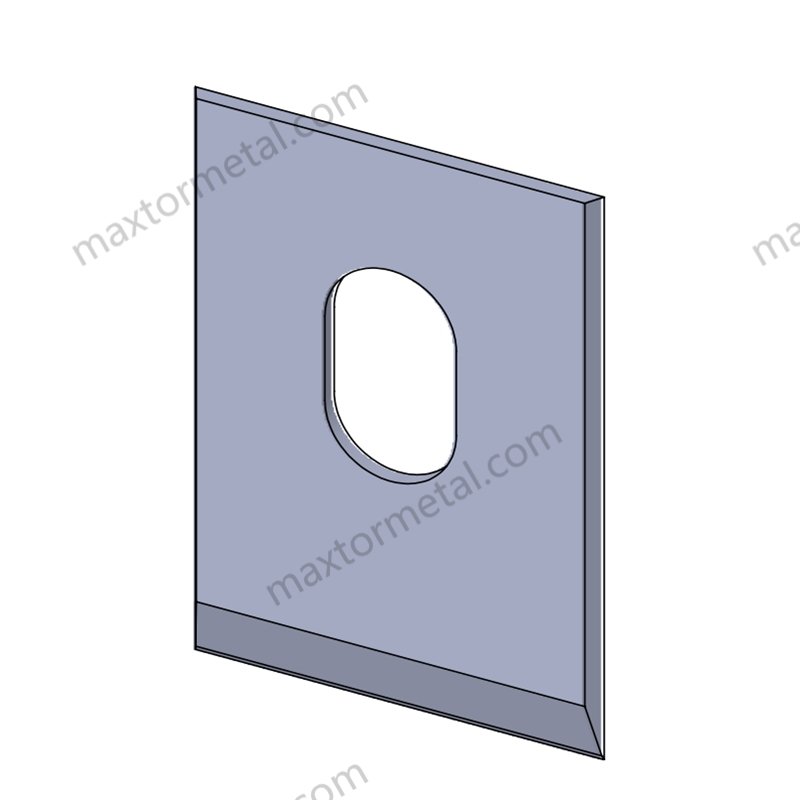
Perché la personalizzazione è importante
You may need a special blade for a certain job. Regular blades do not always work for every task. Customization lets you pick the blade’s material, shape, and how it works. You can choose the right design, grade, and coating for your job. This helps you get better results at work.
- Custom blades let you match the blade to your job. You can change hardness, toughness, and wear resistance.
- Different jobs need different blade shapes and sizes. Mining, aerospace, and packaging all need special designs.
- Working with a skilled maker means your blade will be strong and precise.
- Custom blades work better. They last longer and cut well, even in tough places.
When you make a custom tungsten carbide blade, you can change the alloy mix. You might add more cobalt to make it tougher or more carbide to make it harder. The way the blade is made, like the sintering process, changes how strong and dense it is. These changes help your blade do hard jobs, like cutting metal or working in high heat.
Le lame personalizzate ti offrono molti vantaggi:
- You spend less time fixing blades. A custom blade can last over 31 months, while a regular one may last just one month.
- Your work keeps going. Custom blades stay sharp for thousands of hours, so you do not stop for repairs.
- You save money over time. Fewer replacements and less stopping mean lower costs.
- You get cleaner, faster cuts. Custom blades can cut as close as ±0.001 inches, which means less waste and better quality.
- You help the planet. Custom blades use only what you need, so there is less waste and energy used.
Mancia: If you want to make your work better, save money, and get great results, pick a custom tungsten carbide knife for your next job.
Nanjing Metal Custom Services
If you need a trusted partner for custom blades, you can count on Nanchino Metal. This company is a top knife maker with over 20 years of experience. Nanjing Metal is known for its smart design team and skilled engineers. They focus on making special industrial blades for customers all over the world.
You can send your sample, drawing, or written plan to Nanjing Metal. Their team will design and build a blade that fits your needs. They use advanced CAD/CAM tools and precise machines to make each blade. You get expert help picking materials, like tungsten carbide, D2, HSS, stainless steel, and ceramic. Every blade is checked for quality, from the first sample to the finished product.
Nanjing Metal gives you:
- Custom blade shapes, coatings, and materials to fit your needs.
- OEM and ODM services with quick delivery and good prices.
- Help with big orders and urgent jobs, so you never miss a deadline.
- Full technical help, from testing to after-sales support.
- ISO-certified steps and real-time quality checks for every order.
Are you ready to get better cutting tools? Talk to a Nanjing Metal sales engineer today by Contatti to talk about your custom blade needs.
Manutenzione e cura
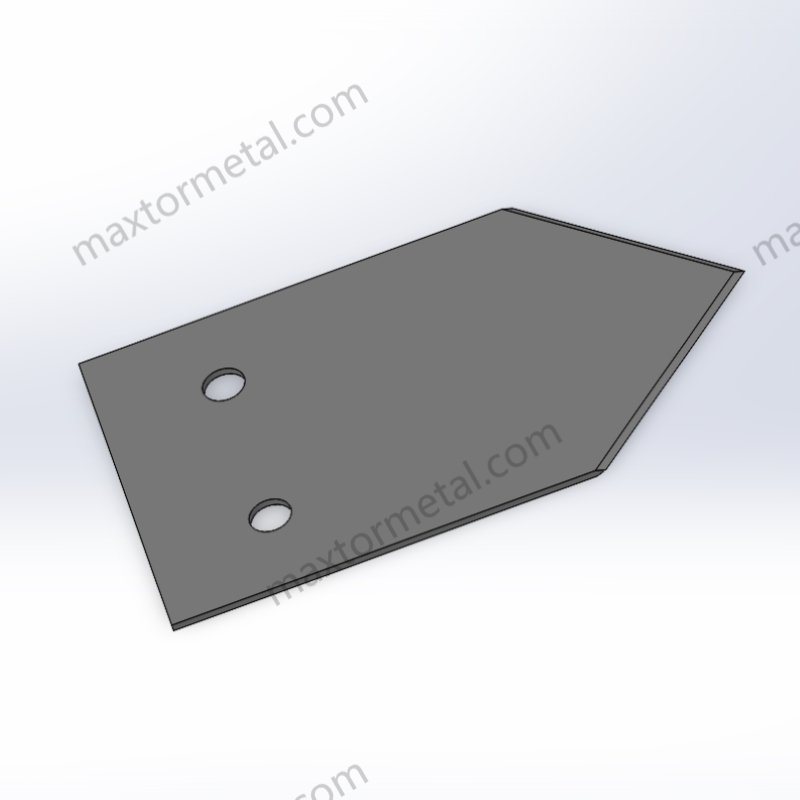
Sharpening and Handling
Recommended Sharpening Tools and Techniques
Per mantenere il tuo lame in carburo di tungsteno sharp, you need special tools. Diamond grinding wheels are the best choice. Diamond is harder than carburo di tungsteno. It sharpens the blade fast and keeps it accurate. Always use coolant to stop the blade from getting too hot. Silicon carbide grinding wheels are cheaper but wear out faster. Use them only for light sharpening jobs. Electrical Discharge Machining (EDM) is good for tricky blade shapes. It uses electric sparks to shape the blade without touching it. Laser sharpening uses a strong light beam to make blades sharp again. This works well in big factories with lots of blades.
Mancia: Always keep the blade cool when sharpening. This stops tiny cracks and keeps the edge strong.
Proper Sharpening Angles for Tungsten Carbide Blades
Try to match the sharpening angle to the original one. This keeps the blade’s shape and helps it last longer. If you use the wrong angle, the blade can chip or wear out quickly.
Safety Precautions During Sharpening
Wear gloves, goggles, and a dust mask. Dust from carburo di tungsteno can be bad for you. Use a dust collector to keep your work area safe.
Cleaning and Handling After Sharpening
After sharpening, clean the blade with a gentle cleaner. Dry it well before using it. Handle the blade carefully so you do not chip the edge.
Maximizing Blade Life
Routine Cleaning and Maintenance
Check your blades every week or after 20 hours of work. Look for dull spots, cracks, or rough edges. Clean with a soft cloth and gentle cleaner. Do not use strong chemicals.
Pratiche di conservazione adeguate
Keep blades in a dry, cool place. Use blade cases or racks to stop bending or damage. Keep the room less humid than 60% to stop rust.
Avoiding Excessive Force and Improper Use
Use the blade only for its main job. Too much force or twisting can hurt the edge and make the blade wear out faster.
Monitoring for Wear and Damage
Look at your blades often. Replace or sharpen them if you see chips or dull spots. This keeps your work safe and neat.
You want your work to turn out great. Picking the right blade is very important. Different types of tungsten carbide have special strengths for certain jobs. Look at the table below to see which blade type fits your needs:
Type | Punti di forza principali | Casi d'uso migliori |
---|---|---|
Fine Grain | Very hard and resists wearing out | Used for precision tools and surgery blades |
Ultrafine Grain | Keeps its edge for a long time | Good for electronics and jewelry making |
Medium Grain | Tough and not easy to break | Works well for general machining and mining |
Coarse Grain | Handles shocks without breaking | Best for heavy mining and drilling |
Submicron | Wears down slowly | Great for fast cutting and smooth finishes |
Cemented | Good for many uses | Used for cutting tools, wear parts, and molds |
Domande frequenti
What makes tungsten carbide blades last longer than regular steel blades?
Tungsten carbide blades have a much harder surface. You get less wear and fewer chips. The edge stays sharp for a long time. You spend less time sharpening and more time working.
Can you use tungsten carbide blades for cutting food?
Yes, you can use these blades in food processing. They resist rust and keep a clean edge. You get smooth, safe cuts for bread, meat, and vegetables. Always choose food-grade blades for safety.
How do you sharpen a tungsten carbide blade?
You need a diamond grinding wheel for sharpening. Use gentle pressure and keep the blade cool. This method protects the edge and gives you a sharp, long-lasting tool.
Mancia: Always wear safety gear when sharpening to protect yourself from dust and chips.
Vedi anche
Padroneggiare l'arte delle lame in carburo di tungsteno
Come prolungare efficacemente la durata delle lame circolari in acciaio al tungsteno?
I 10 Principali Fornitori e Produttori di Lame per Granulatori che Devi Conoscere nel 2025
I 10 Principali Produttori e Fornitori di Lame per Granulazione ad Anello d'Aria nel 2025
Trova le Lame di Granulazione Perfette per le Tue Esigenze di Lavorazione della Plastica
Una risposta