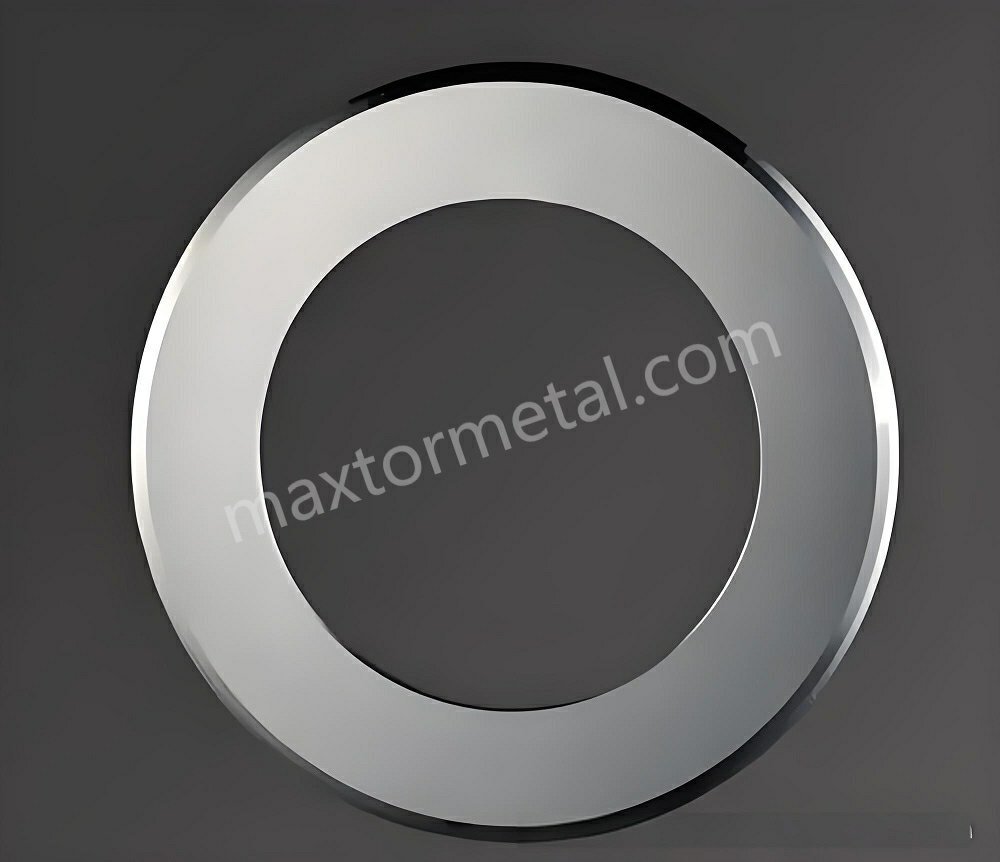
Le lame e i coltelli industriali in metallo duro sono diventati strumenti essenziali per molti processi produttivi, offrendo vantaggi significativi rispetto ai materiali tradizionali. Queste lame e coltelli ad alte prestazioni sono progettati per resistere a condizioni estreme, garantendo ai produttori una maggiore produttività, tempi di fermo ridotti e una migliore qualità del prodotto.
In questa guida, esploreremo tutto ciò che devi sapere sulle lame e i coltelli industriali in metallo duro, inclusi i loro vantaggi, le applicazioni e come sceglierli e mantenerli. Comprendendo questi aspetti, sarai in grado di prendere decisioni consapevoli che ottimizzeranno le tue operazioni.
1. Panoramica delle lame e dei coltelli industriali in metallo duro
Cosa sono le lame e i coltelli industriali in metallo duro?
Le lame e i coltelli industriali in carburo sono utensili da taglio realizzati principalmente con materiali in carburo, in particolare carburo di tungsteno (WC), un composto estremamente duro e resistente all'usura. Queste lame sono progettate per tagli di precisione in un'ampia gamma di applicazioni industriali, offrendo una durata superiore rispetto alle tradizionali lame in acciaio.
Composizione del materiale delle lame in carburo
Il componente principale delle lame industriali in metallo duro è il carburo di tungsteno, un composto metallico denso altamente resistente all'usura e all'abrasione. Oltre al tungsteno, le lame in metallo duro possono contenere altri elementi come cobalto (Co) O titanio (Ti), che migliorano la tenacità e le prestazioni del materiale. La composizione delle lame in carburo le rende ideali per il taglio di materiali duri, come metalli, plastica e gomma, che ottunderebbero rapidamente le tradizionali lame in acciaio.
Materiale | Proprietà | Applicazioni |
Carburo di tungsteno | Estremamente duro, resistente all'usura, durevole | Taglio metallo, plastica, Lame per Gomma |
Cobalto | Migliora la tenacità e la resistenza agli urti | Applicazioni pesanti |
Titanio | Leggero e resistente alla corrosione | Industria aerospaziale e automobilistica |
Come funzionano le lame in carburo
Le lame in metallo duro sfruttano la loro estrema durezza e resistenza all'usura per tagliare materiali tenaci con un'usura minima. I bordi affilati delle lame in metallo duro rimangono intatti molto più a lungo rispetto alle tradizionali lame in acciaio, il che significa meno sostituzioni e cicli di taglio più lunghi. Questo è particolarmente importante per le industrie che richiedono un taglio continuo e ad alto volume.
2. L'evoluzione delle lame in metallo duro
Sviluppo precoce e sfide
Le lame in metallo duro furono introdotte per la prima volta all'inizio del XX secolo per rispondere alla crescente necessità di utensili da taglio più resistenti. Le lame in acciaio tradizionali non erano sufficientemente efficienti per il taglio di materiali tenaci, il che portò allo sviluppo di utensili in metallo duro. Tuttavia, le prime lame in metallo duro presentavano problemi legati alla fragilità e alle tecniche di produzione limitate.
Progressi tecnologici nella produzione di lame in carburo
Nel corso degli anni, innovazioni tecnologiche come i processi di sinterizzazione e i rivestimenti superficiali hanno migliorato significativamente le prestazioni delle lame in metallo duro. Il processo di sinterizzazione, in cui la polvere di metallo duro viene compattata e riscaldata per formare lame solide, ne ha migliorato la durata e la consistenza. Inoltre, sono stati applicati rivestimenti superficiali come il nitruro di titanio (TiN) per migliorare la resistenza all'usura e ridurre l'attrito.
Produzione moderna e tecnologia CAD/CAM
Oggigiorno, tecnologie avanzate come CAD (progettazione assistita da computer) e CAM (Computer-Aided Manufacturing) stanno rivoluzionando la progettazione e la produzione di lame in metallo duro. Queste tecnologie consentono ai produttori di creare coltelli e lame in metallo duro altamente precisi e personalizzati, che soddisfano i requisiti specifici di diversi settori, dall'aerospaziale all'industria alimentare.
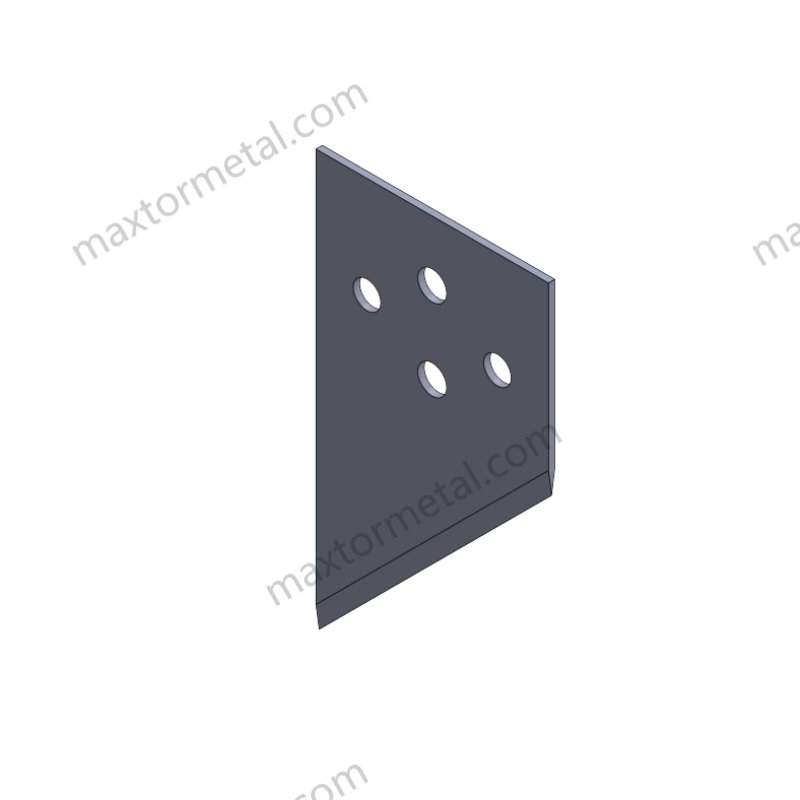
3. Vantaggi delle lame e dei coltelli industriali in metallo duro
Le lame e i coltelli industriali in metallo duro sono diventati strumenti indispensabili in molti settori manifatturieri grazie alle loro eccezionali prestazioni e affidabilità. Approfondiamo i vantaggi offerti da queste lame, integrando specifiche tecniche, dati e ricerche di settore.
Durezza eccezionale e resistenza all'usura
La caratteristica più notevole delle lame in carburo è la loro eccezionale durezza, che supera di gran lunga quella delle lame in acciaio tradizionali. Il carburo di tungsteno, comunemente utilizzato nella produzione di queste lame, ha una durezza di 8-9 sulla scala di Mohs, ovvero circa 3-5 volte superiore a quella dell'acciaio per utensili.
- Approfondimenti sui dati: Secondo studi di settore, le lame in carburo di tungsteno mantengono il filo tagliente fino a 5 volte più a lungo rispetto alle lame in acciaio rapido (HSS) in ambienti di taglio abrasivo. Ciò si traduce in costi di manutenzione ridotti e tempi di attività maggiori negli ambienti di produzione.
- Approfondimento tecnico: La densa struttura molecolare del carburo di tungsteno resiste all'usura e all'abrasione, consentendo alla lama di funzionare in modo costante per lunghi periodi senza subire degradazioni significative. Questa resistenza all'usura rende le lame in carburo ideali per applicazioni ad alta intensità, come il taglio di lamiere, gomma spessa e materiali plastici, tutti materiali che tendono a smussare rapidamente le lame tradizionali.
Prestazioni di taglio superiori
Le lame in metallo duro offrono prestazioni di taglio superiori grazie alla loro durezza e alla capacità di mantenere l'affilatura. La loro stabilità del filo le rende ideali per il taglio di precisione in una varietà di materiali, tra cui metalli, materie plastiche, materiali compositi e gomma.
- Esempio: Nell'industria metallurgica, le lame in carburo di tungsteno vengono spesso utilizzate per il taglio di acciaio, alluminio e rame. Uno studio della Carbide Tool Manufacturers Association (CTMA) ha dimostrato che le lame in carburo di tungsteno utilizzate per il taglio di leghe di alluminio possono mantenere l'integrità del tagliente fino a 200% in più rispetto agli utensili in acciaio standard.
- Applicazione industriale: Le lame in metallo duro sono ampiamente utilizzate nella produzione automobilistica, dove il taglio preciso dei componenti in alluminio è essenziale per mantenere tolleranze ristrette. La capacità di resistere a elevate pressioni di taglio e di mantenere un filo affilato rende le lame in metallo duro ideali per i settori che richiedono sia resistenza che precisione.
Maggiore durata e longevità
Oltre alla durezza, le lame in carburo mostrano una notevole resistenza in condizioni estreme, tra cui alte temperature, operazioni ad alta velocità e urti.
- Resistenza alla temperatura: Le lame in carburo di tungsteno mantengono la loro durezza a temperature superiori a 1.000 °C (1.832 °F), rendendole ideali per operazioni di taglio ad alta temperatura, come nei settori aerospaziale e automobilistico. Questa resistenza alle temperature impedisce alle lame di diventare fragili o di perdere l'affilatura, prolungandone così la durata operativa.
- Dati:In una ricerca condotta da Advanced Materials Research, gli utensili in metallo duro utilizzati nelle applicazioni di taglio ad alta velocità hanno mostrato un'usura inferiore del 40% rispetto alle loro controparti in HSS, anche durante il taglio di materiali come titanio e acciaio inossidabile, notoriamente difficili da lavorare.
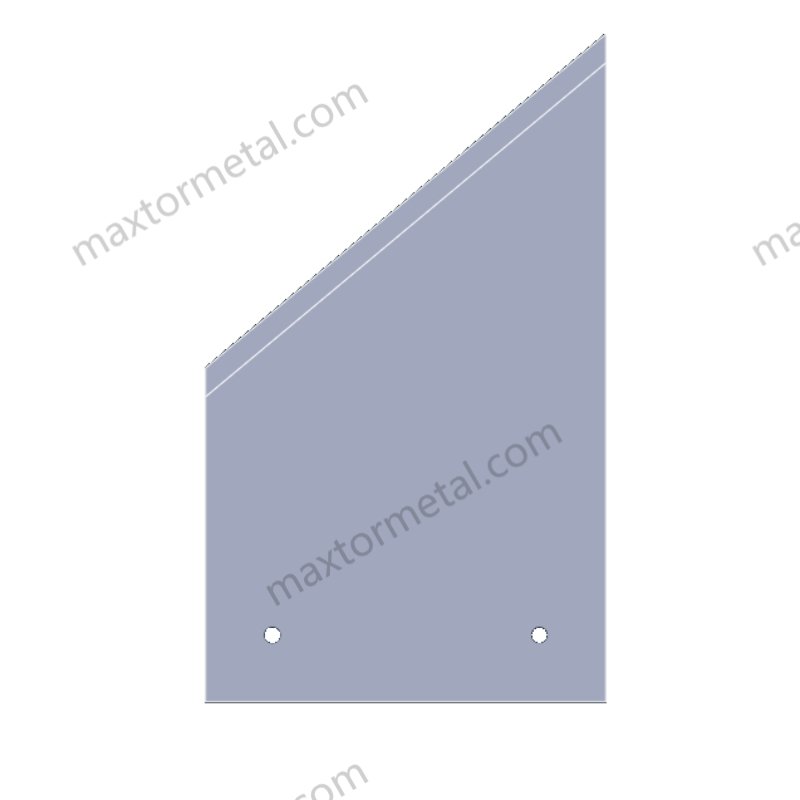
Capacità di taglio di precisione
Le lame in metallo duro eccellono nel taglio preciso grazie alla loro affilatura, alla tenuta del filo e alla resistenza alla flessione sotto pressione. Questo è fondamentale nei settori che richiedono una produzione ad alta precisione.
- Produzione di dispositivi medici: Le lame in metallo duro sono fondamentali per la produzione di strumenti medicali ad alta precisione. Ad esempio, nella produzione di strumenti chirurgici, la capacità di tagliare forme complesse con deviazioni minime dalle dimensioni specificate è essenziale. Una ricerca del Journal of Precision Manufacturing indica che le lame in metallo duro mantengono tolleranze entro ±0,001 mm, rendendole preziose per le applicazioni medicali.
- Lavorazione alimentare: Le lame in metallo duro vengono utilizzate per affettare e tagliare a cubetti carne, verdure e persino formaggio nelle linee di lavorazione alimentare. La loro elevata precisione garantisce tagli uniformi, fondamentali per la costanza del prodotto e il controllo qualità. Secondo un rapporto della Food Manufacturing Association (FMA), le lame in metallo duro utilizzate nella produzione alimentare riducono gli sprechi di prodotto fino al 25% grazie alle loro prestazioni costanti e alla lunga durata.
Ampia gamma di applicazioni
La versatilità delle lame in metallo duro ne consente l'utilizzo in diversi settori, ognuno con esigenze specifiche. Ecco alcuni dei settori più importanti che utilizzano le lame in metallo duro:
- Lavorazione alimentare: I coltelli in metallo duro vengono utilizzati per tagliare, affettare e tagliare a cubetti un'ampia gamma di prodotti alimentari. La loro precisione riduce gli sprechi alimentari e garantisce una qualità costante, fondamentale per il confezionamento e la vendita al dettaglio.
- Aerospaziale: L'industria aerospaziale si affida alle lame in metallo duro per il taglio ad alta precisione di materiali compositi e leghe. Gli utensili in metallo duro vengono utilizzati per rifinire i componenti degli aeromobili, dove precisione e finitura superficiale sono fondamentali.
- Settore Medicale:Le lame in carburo svolgono un ruolo importante nella produzione di strumenti chirurgici e dispositivi impiantabili, dove la precisione è fondamentale per garantire la sicurezza e l'efficacia del prodotto.
- Plastica e gomma:I coltelli in carburo sono essenziali per tagliare materiali compositi o gomma resistenti nei settori che richiedono una produzione ad alta velocità e grandi volumi.
4. Come scegliere la lama o il coltello in metallo duro industriale giusto
Scegliere la lama o il coltello in metallo duro più adatti è fondamentale per ottimizzare l'efficienza produttiva e garantire prestazioni durature. Diversi fattori devono essere considerati nella scelta del fornitore e della lama più adatta alle proprie esigenze.
Selezione del fornitore di lame giusto
Nella scelta di un fornitore di lame in metallo duro, date priorità alle aziende con una vasta esperienza nel settore e una comprovata esperienza nella produzione di alta qualità. Un fornitore affidabile dovrebbe anche offrire servizi di personalizzazione per garantire che le lame soddisfino le specifiche esclusive del vostro processo di produzione.
- Nanchino Metal vanta oltre 18 anni di esperienza nel settore della produzione di lame industriali ed è nota per la produzione di coltelli in metallo duro ad alte prestazioni, adattabili a un'ampia gamma di applicazioni industriali.
- Dati:Secondo Global Market Insights, i produttori che collaborano con fornitori affermati ed esperti riscontrano una riduzione del 15-20% nei costi operativi grazie alla maggiore longevità ed efficienza delle loro lame in carburo.
Considerazioni chiave nella scelta di una lama
- Tipo di materiale: La composizione del carburo gioca un ruolo fondamentale nelle sue prestazioni. Le lame in carburo di tungsteno sono in genere arricchite con cobalto, che ne aumenta la tenacità, mentre le lame in carburo di titanio sono ideali per operazioni di taglio ad alta velocità.
- Forma e dimensione della lama: La geometria della lama, che sia piatta, curva o angolata, deve essere allineata al materiale da tagliare. Ad esempio, una lama progettata per il taglio metalli duri potrebbe richiedere un design più rigido e spesso, mentre quello utilizzato per tagliare materiali più morbidi potrebbe dover essere più fine per evitare deformazioni.
- Processo di taglio: Anche il tipo di processo di taglio determina il design della lama. Per applicazioni di taglio ad alta velocità, sono necessarie lame con maggiore resistenza al calore e all'usura per sopportare l'attrito intenso. Per un taglio continuo, una maggiore durata del filo è fondamentale.
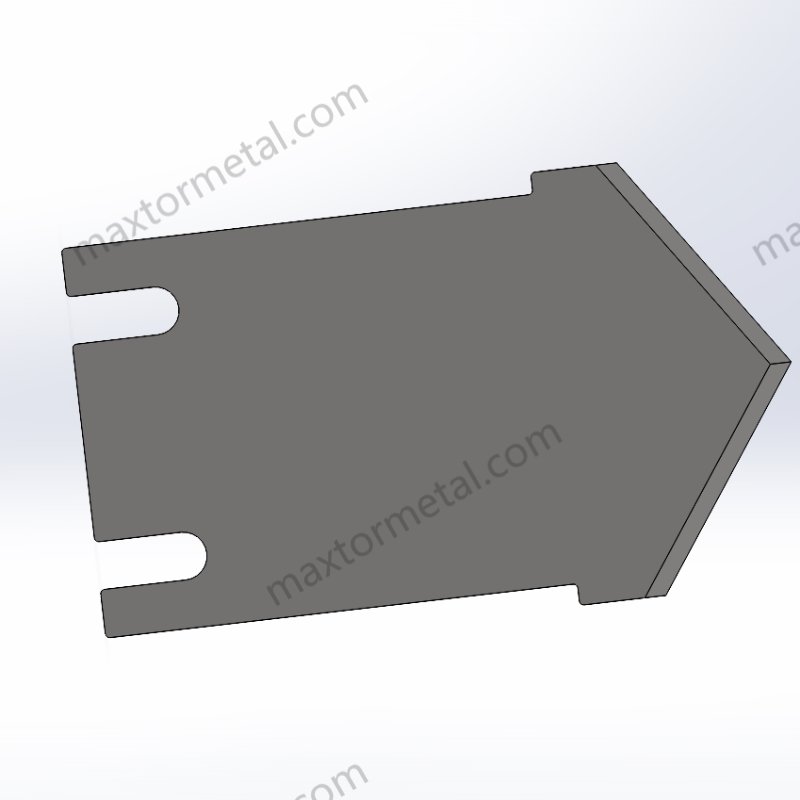
L'importanza della personalizzazione
Le lame in metallo duro personalizzate sono realizzate su misura per le vostre specifiche esigenze di taglio, garantendo la massima efficienza e prestazioni. Nanjing Metal offre una gamma completa di lame in metallo duro personalizzate per adattarsi a diverse applicazioni, dalla lavorazione alimentare all'industria automobilistica.
- Approfondimento tecnico: Le lame in metallo duro personalizzate consentono ai produttori di ottimizzare la velocità e la precisione di taglio. Secondo uno studio di Advanced Tooling Technologies, le aziende che utilizzano lame in metallo duro personalizzate segnalano un aumento del 20-30% dell'efficienza di taglio complessiva rispetto a quelle che utilizzano lame standard disponibili in commercio.
- Vantaggi della personalizzazione:La personalizzazione consente inoltre ai produttori di affrontare sfide specifiche, quali durezza del materiale, geometria di taglio e mantenimento desiderato del bordo, migliorando l'efficienza operativa complessiva e riducendo i tempi di fermo per manutenzione.
5. Manutenzione e cura delle lame in carburo
Suggerimenti per prolungare la durata della lama
Le lame industriali in metallo duro sono progettate per garantire durata e precisione, ma senza la dovuta cura, anche le lame migliori possono usurarsi prematuramente. Una manutenzione regolare e un utilizzo proattivo sono fondamentali per massimizzare la durata delle lame in metallo duro.
Pulizia regolare delle lame
Per mantenere le prestazioni di taglio ottimali, è fondamentale pulire regolarmente le lame in metallo duro. L'accumulo di residui, come polvere, detriti o residui di materiale, può compromettere l'efficienza di taglio della lama e, nel tempo, causare un'usura indesiderata del tagliente.
- Approfondimento dei dati:Secondo l'International Journal of Manufacturing Technology, fino al 30% di guasti agli utensili in metallo duro in ambito industriale sono dovuti a una pulizia non idonea, in particolare nelle operazioni di taglio abrasivo in cui si accumulano polvere e materiali fini.
- Tecniche di pulizia: Utilizzare una spazzola o un panno non abrasivo per rimuovere l'accumulo di materiale. Per residui più ostinati, come metallo o gomma, utilizzare un solvente delicato (come acetone o alcol) e un panno morbido. Evitare l'uso di sostanze chimiche aggressive che potrebbero danneggiare il rivestimento o l'integrità superficiale del carburo.
- Benefits: Mantenere la lama libera da accumuli impedisce che il materiale influisca sull'affilatura del filo e riduce il rischio di intasamento, che può portare al surriscaldamento durante il taglio. Questo aiuta a mantenere prestazioni costanti, anche durante lunghe tirature.
Pratiche di conservazione adeguate
Una corretta conservazione è essenziale per evitare danni ambientali alle lame in metallo duro, che potrebbero comprometterne la durata e le prestazioni.
- Condizioni di conservazione: Conservare le lame in un ambiente asciutto e fresco dove siano protette da temperature estreme, umidità o luce solare diretta. Un eccesso di umidità può causare ruggine o corrosione sulla superficie della lama, anche per le lame in metallo duro, che sono altamente resistenti all'usura ma possono comunque essere soggette a corrosione in condizioni estreme.
- Approfondimento dei dati: Una ricerca condotta dal Tool Wear Journal ha scoperto che le lame in carburo conservate sotto condizioni ottimali (in un ambiente fresco e asciutto) hanno durato fino a 25% in più rispetto a quelle conservate in aree con temperature e livelli di umidità variabili. Uno stoccaggio costante e controllato garantisce che le lame mantengano la loro integrità e funzionino in modo ottimale.
- Imballaggio e organizzazione:Per una protezione aggiuntiva, le lame in carburo devono essere avvolte singolarmente in custodie protettive o conservate in appositi contenitori per lame, che prevengono danni o tagli accidentali durante la manipolazione.
Ispezione regolare della lama
Le ispezioni di routine sono essenziali per individuare tempestivamente eventuali segni di usura, consentendo così di intervenire tempestivamente con la manutenzione o la sostituzione prima che si verifichino danni significativi.
- Frequenza di ispezione: A seconda dell'intensità di utilizzo, ispezionare le lame almeno una volta alla settimana o dopo ogni importante ciclo produttivo. Verificare la presenza di scheggiature, crepe o smussatura del filo, che possono indicare usura. Un rilevamento tempestivo può evitare costosi tempi di fermo causati da guasti imprevisti dell'utensile.
- Tecniche di ispezione avanzate: Si consiglia di utilizzare micrometri o microscopi ottici per misurazioni più precise dell'usura della lama. I micrometri possono misurare lo spessore del bordo per rilevare l'assottigliamento, mentre un microscopio ottico può identificare microfratture e altri segni di degradazione invisibili a occhio nudo.
- Manutenzione preventiva: Se la lama mostra i primi segni di danneggiamento, è meglio sostituirla o affilarla immediatamente piuttosto che aspettare un guasto completo. Una manutenzione ritardata può causare difetti nel prodotto finale e colli di bottiglia operativi.
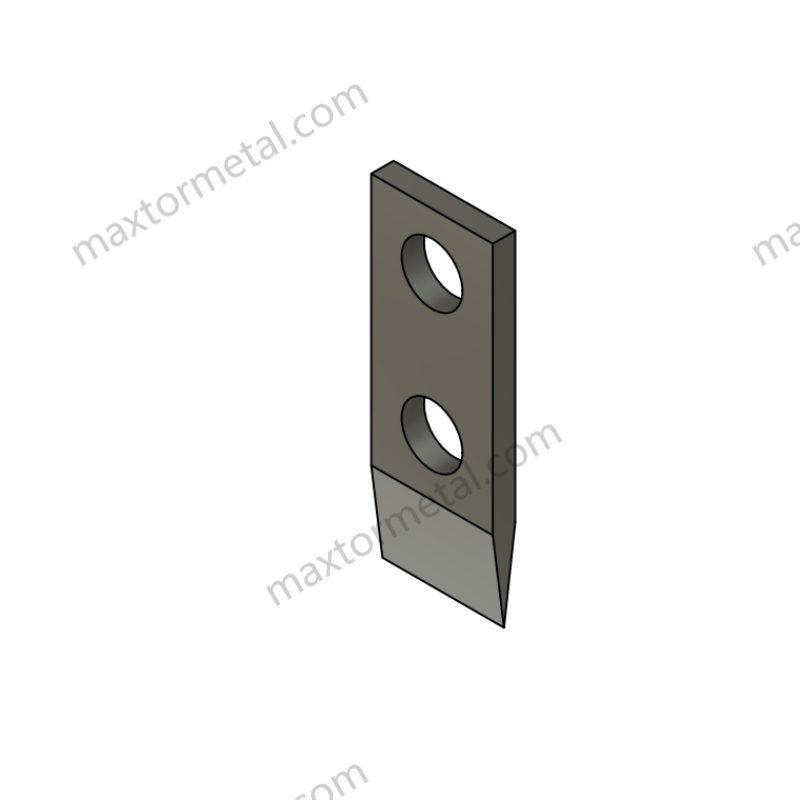
Buone pratiche per l'utilizzo della lama
Per garantire la longevità e l'efficacia delle lame in metallo duro, è essenziale adottare le migliori pratiche d'uso. Sovraccaricare le lame o utilizzare parametri errati può causare un'usura prematura, una riduzione delle prestazioni e potenzialmente costosi tempi di fermo.
Evitare di sovraccaricare le lame
Uno degli errori più comuni nell'uso delle lame è il sovraccarico, che consiste nel forzare una lama in metallo duro a tagliare materiali che superano la sua capacità di progettazione.
- Rischi di sovraccaricoSovraccaricare la lama con una pressione eccessiva o tentare di tagliare materiali eccessivamente duri può causare microfratture nel carburo o far perdere il filo alla lama. In casi estremi, potrebbe portare a guasti catastrofici, con danni significativi alla lama e ad altri componenti del macchinario.
- Caso di studioUno studio di Cutting Tool Engineering ha dimostrato che le lame in metallo duro che operavano entro i limiti di progetto duravano 30-50% in più rispetto a quelle sottoposte a pressione eccessiva. Lo studio ha sottolineato che il sovraccarico potrebbe causare non solo la rottura della lama, ma anche un aumento delle vibrazioni durante il taglio, compromettendo la qualità del materiale in lavorazione.
- Ottimizzazione del carico di taglio: Assicurarsi sempre che il carico di lavoro e il tipo di materiale siano conformi alle specifiche della lama in metallo duro. Ad esempio, coltelli in metallo duro progettati per plastiche morbide Non deve essere utilizzato per tagliare lamiere spesse. Allo stesso modo, utilizzare la lama entro i limiti di velocità e avanzamento consigliati previene il sovraccarico.
Ottimizza i parametri di taglio
Ogni lama in metallo duro è progettata con un set specifico di parametri che ne ottimizzano l'efficienza di taglio. Questi parametri includono velocità di taglio, pressione e velocità di avanzamento, che devono essere attentamente calibrati in base al materiale da tagliare.
- Velocità di taglio: Le lame in metallo duro in genere offrono prestazioni migliori a velocità più elevate, ma è importante non superare i limiti raccomandati dal produttore. Il taglio ad alta velocità aiuta a ridurre al minimo l'attrito, prevenendo un eccessivo accumulo di calore che potrebbe causare un'usura prematura.
- Velocità di avanzamento: La velocità con cui il materiale viene alimentato nel tagliente influisce sulle prestazioni della lama. Un'alimentazione troppo rapida può sovraccaricare la lama, mentre un'alimentazione troppo lenta può causare un'usura inutile dovuta al contatto prolungato con il materiale.
- Approfondimento dei datiSecondo uno studio di Carbide Tool Research, le lame in metallo duro tagliano in modo più efficiente quando la velocità di avanzamento è impostata tra 150 e 250 mm/min per le applicazioni su metallo e tra 300 e 500 mm/min per le applicazioni su materiali plastici. Lavorare al di fuori di questi parametri può aumentare l'usura della lama fino a 40%, poiché il filo della lama potrebbe essere sottoposto a sollecitazioni eccessive.
- Controllo della pressione: Mantenere una pressione ottimale garantisce che la lama in metallo duro funzioni in modo efficiente senza usura eccessiva. Una pressione eccessiva può deformare il tagliente, mentre una pressione insufficiente può causare inefficienza e tagli irregolari.
Calibrazione e monitoraggio regolari degli strumenti
Per massimizzare la durata della lama e garantire la costanza, è essenziale calibrare regolarmente i macchinari da taglio per soddisfare gli standard prestazionali ottimali delle lame in metallo duro.
- Calibrazione degli utensili: Utilizzare sistemi di monitoraggio della macchina per monitorare le prestazioni delle lame in metallo duro, regolando parametri come velocità, pressione e velocità di avanzamento per evitare un'usura eccessiva. I sistemi di monitoraggio possono rilevare quando è necessario regolare le impostazioni, evitando sollecitazioni inutili sulle lame.
- Approfondimenti sui dati: Studi di IOIl gruppo di ricerca sugli utensili industriali ha scoperto che la calibrazione regolare delle macchine riduceva l'usura della lama di 15-20%, migliorando la durata complessiva dell'utensile e la produttività. Inoltre, i sistemi di monitoraggio automatizzati possono prevedere quando una lama si avvicina alla fine della sua durata di taglio ottimale, consentendone la sostituzione tempestiva prima che si verifichi un guasto.
Utilizzare metodi di raffreddamento adeguati
L'accumulo di calore durante il taglio può ridurre significativamente la durata delle lame in metallo duro. Pertanto, l'impiego di metodi di raffreddamento efficaci è essenziale, soprattutto nelle applicazioni ad alta velocità.
- Utilizzo del refrigerante: L'utilizzo di sistemi di raffreddamento appropriati, come refrigeranti liquidi o getti d'aria, può prevenire il surriscaldamento e ridurre l'attrito. Ciò è particolarmente utile quando si tagliano metalli o altri materiali sensibili al calore.
- Vantaggi del raffreddamento:Secondo un rapporto del Journal of Manufacturing Science and Engineering, l'utilizzo di un sistema di raffreddamento ad alta pressione durante il taglio con utensili in metallo duro può aumentare la durata dell'utensile fino al 50%, poiché aiuta a dissipare il calore in modo più efficiente, proteggendo così il filo della lama dal degrado termico.
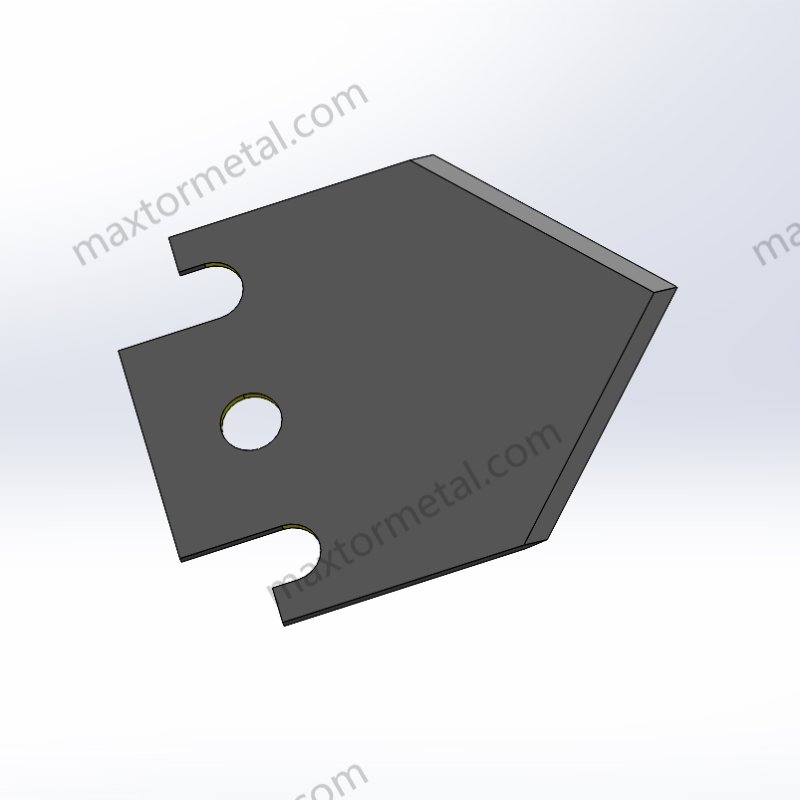
6. Nanjing Metal Competenza nelle lame in metallo duro
Background aziendale
Con oltre 18 anni di esperienza nel settore, Nanjing Metal è un produttore leader di lame e coltelli industriali in metallo duro. Il nostro team di esperti utilizza tecnologie all'avanguardia e materiali di alta qualità per produrre lame che soddisfano esattamente le esigenze dei nostri clienti. Ci impegniamo a fornire soluzioni durevoli, affidabili e convenienti per le industrie di tutto il mondo.
Soluzioni personalizzate
Noi di Nanjing Metal comprendiamo che ogni settore ha esigenze di taglio uniche. Ecco perché offriamo lame e coltelli in metallo duro completamente personalizzati, su misura per le vostre esigenze specifiche. Che operiate nel settore aerospaziale, automobilistico o alimentare, possiamo progettare e produrre lame che offrano prestazioni ottimali.
Garanzia di qualità e assistenza clienti
Noi di Nanjing Metal prendiamo sul serio il controllo qualità. Ogni lama in metallo duro viene sottoposta a rigorosi test per garantire che soddisfi i nostri elevati standard di durata, precisione e prestazioni. Il nostro team di assistenza clienti dedicato è sempre pronto ad assistervi per qualsiasi richiesta, garantendovi un'esperienza fluida e soddisfacente.
7. Tendenze del settore e prospettive future
Innovazioni tecnologiche nel settore delle lame in metallo duro
Il settore delle lame in metallo duro sta subendo trasformazioni significative con l'emergere di nuove tecnologie, che consentono ai produttori di creare utensili da taglio più efficienti, durevoli e precisi. Queste innovazioni sono principalmente guidate dai progressi in produzione intelligente, automazione, E Industria 4.0 principi.
1. Produzione intelligente e automazione
La produzione intelligente si riferisce all'uso di tecnologie avanzate come IoT (Internet delle cose), IA (Intelligenza Artificiale), E apprendimento automatico Per migliorare le capacità produttive. Nel contesto della produzione di lame in metallo duro, queste tecnologie contribuiscono a ottenere una maggiore precisione nella progettazione, nella produzione e nel monitoraggio in tempo reale delle prestazioni della lama.
- Produzione basata sui datiIntegrando sensori e dispositivi IoT nelle linee di produzione, i produttori possono raccogliere dati in tempo reale sull'usura delle lame, sulla velocità di taglio, sulla durezza del materiale e sullo stress dell'utensile. Questi dati consentono regolazioni dinamiche durante la produzione, ottimizzando la durata delle lame in metallo duro. Ad esempio, un sistema basato su sensori può rilevare quando una lama in metallo duro presenta un'usura eccessiva o un surriscaldamento, regolando automaticamente i parametri di taglio per preservare la durata dell'utensile.
- IA per la progettazione e la simulazione delle paleL'utilizzo di software di progettazione basati sull'intelligenza artificiale sta rivoluzionando il modo in cui vengono progettate le lame in metallo duro. Gli algoritmi di intelligenza artificiale possono analizzare vasti set di dati per prevedere la geometria ottimale della lama, il materiale di rivestimento e le prestazioni in diverse condizioni operative. Ad esempio, gli strumenti di intelligenza artificiale possono simulare l'impatto degli angoli di taglio e dei rivestimenti in metallo duro sulle prestazioni della lama in diverse applicazioni industriali, riducendo drasticamente i tempi di prototipazione e gli sprechi di materiale.
- Automazione nella produzione: I macchinari automatizzati dotati di bracci robotici e rettificatrici di precisione possono produrre lame in metallo duro con un grado di precisione superiore rispetto ai metodi tradizionali. Questo si traduce in lame con qualità e uniformità costanti, riducendo i difetti e aumentandone la durata. I sistemi automatizzati di controllo qualità consentono inoltre di rilevare rapidamente eventuali discrepanze nella qualità delle lame durante la produzione, con conseguente miglioramento dell'efficienza produttiva e riduzione al minimo degli sprechi.
- Impatto sull'efficienza produttivaSecondo uno studio di McKinsey & Company, i produttori che hanno adottato tecniche di produzione intelligenti hanno registrato aumenti di produttività fino a 30%, poiché l'automazione riduce l'errore umano, migliora la precisione di taglio e riduce gli sprechi di materiale. Inoltre, queste tecnologie consentono un feedback in tempo reale, consentendo un'ottimizzazione continua dei parametri di produzione, migliorando l'uniformità e la durata delle lame in metallo duro.
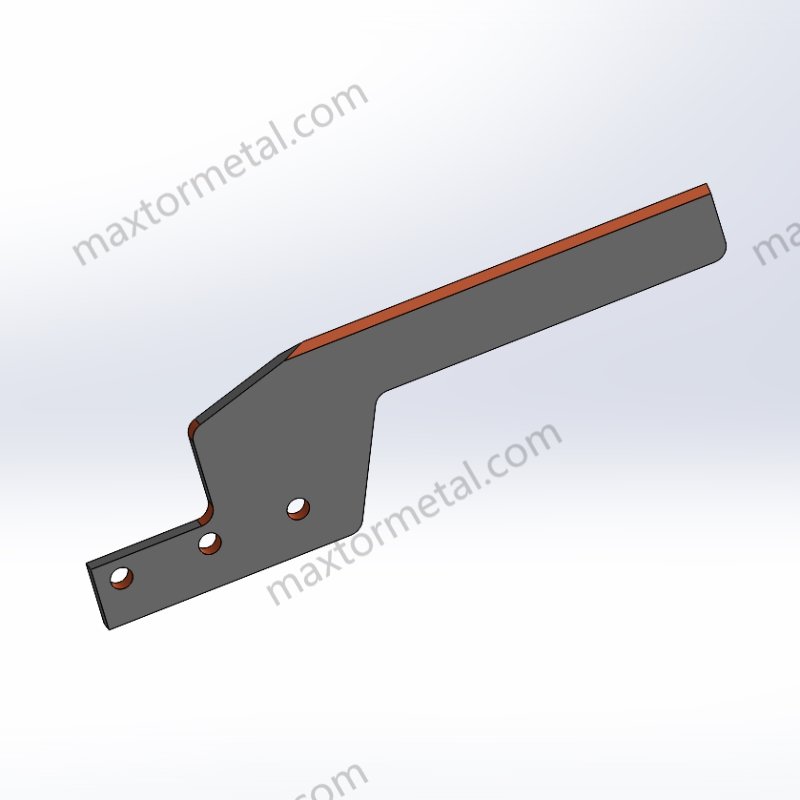
2. Produzione additiva (stampa 3D) per la produzione di utensili in metallo duro
Produzione additiva, o stampa 3D, sta diventando sempre più rilevante nella produzione di lame in metallo duro. Sebbene la tecnologia sia ancora in fase di sviluppo nel settore degli utensili da taglio industriali, il suo potenziale è enorme:
- Utensili personalizzati: La stampa 3D consente la creazione di lame in metallo duro personalizzate con geometrie complesse, difficili da realizzare con i metodi di produzione tradizionali. Questo è particolarmente utile per i settori che richiedono design di pale altamente specifici, come quello aerospaziale o della produzione di dispositivi medicali.
- Prototipazione più rapida: La produzione additiva consente la prototipazione rapida di lame in metallo duro, consentendo ai produttori di testare e perfezionare i progetti prima di impegnarsi nella produzione su larga scala. Ciò riduce il tempo di commercializzazione per i nuovi prodotti e riduce al minimo i rischi associati ai difetti di progettazione.
- Innovazione dei materiali:Mentre la stampa 3D è stata tradizionalmente limitata dalla selezione dei materiali, i recenti progressi nella tecnologia di stampa ora consentono l'uso di materiali ad alte prestazioni polveri metalliche, compresi quelli per le leghe di carburo. Ciò apre possibilità per la produzione di lame con proprietà migliorate, come resistenza all'usura migliorata E maggiore tenacità, che in precedenza erano irraggiungibili con i metodi convenzionali.
Sostenibilità nel settore delle lame in metallo duro
Con l'affermazione della sostenibilità come forza trainante in tutti i settori, anche il settore delle lame in metallo duro si sta evolvendo per integrare pratiche più ecocompatibili in tutto il processo produttivo. I produttori si stanno concentrando sulla riduzione dell'impatto ambientale adottando pratiche di riciclo, esplorando materiali ecocompatibili e migliorando l'efficienza energetica.
1. Materiali in carburo riciclato
Una delle principali sfide ambientali nella produzione di lame in metallo duro è la necessità di materie prime, in particolare il carburo di tungsteno. Il tungsteno è un materiale raro e ad alta intensità di risorse, il che rende l'approvvigionamento e il riciclo sostenibili fondamentali per la sostenibilità a lungo termine del settore.
- Programmi di riciclaggioMolti produttori di lame in metallo duro hanno implementato sistemi di riciclo a circuito chiuso, in cui le lame usurate o scartate vengono restituite al produttore, smontate e utilizzate per produrne di nuove. Ciò riduce la necessità di materie prime vergini e riduce l'impatto ambientale dell'estrazione di tungsteno e altri metalli.
- Approfondimento dei datiSecondo la World Tungsten Association, circa il 30-40% della fornitura globale di tungsteno proviene da materiali riciclati. Per gli utensili in metallo duro, ciò rappresenta una significativa riduzione dell'impatto ecologico della produzione di lame. Le aziende possono anche ridurre significativamente i costi dei materiali utilizzando polvere di carburo di tungsteno riciclata, il che si traduce in una produzione di lame più economica ed ecologica.
- Vantaggi del riciclaggioUtilizzando materiali riciclati, i produttori non solo riducono gli sprechi, ma riducono anche le emissioni di carbonio. L'energia necessaria per produrre carburo di tungsteno dal minerale grezzo è significativamente superiore a quella necessaria per la lavorazione di materiali in carburo riciclato. Questo aiuta le aziende a raggiungere gli obiettivi di sostenibilità e ad allinearsi agli standard ambientali globali.
2. Pratiche di produzione ecologiche
- Efficienza energetica: I produttori stanno adottando sempre più tecnologie a basso consumo energetico nei loro processi produttivi. Questo include l'utilizzo di forni ad alta efficienza per la sinterizzazione di lame in metallo duro, che riducono il consumo energetico fino a 20% rispetto ai metodi convenzionali. L'integrazione di impianti solari e altre fonti di energia rinnovabile sta inoltre aiutando i produttori a ridurre la loro impronta di carbonio.
- Rivestimenti ecocompatibiliUn'altra innovazione sostenibile nella produzione di lame in metallo duro è l'utilizzo di rivestimenti ecocompatibili. I rivestimenti tradizionali spesso si basano su sostanze chimiche che possono essere dannose per l'ambiente. Tuttavia, sempre più produttori stanno passando a rivestimenti a base d'acqua e materiali atossici che offrono prestazioni simili senza danneggiare l'ambiente.
- Riduzione dei rifiutiOttimizzando i processi di taglio e riducendo gli sprechi di materiale, i produttori di lame in metallo duro stanno riducendo al minimo l'impatto ambientale della produzione. Le tecnologie di taglio di precisione consentono ai produttori di ridurre gli scarti e migliorare la resa complessiva.
- Impatto delle pratiche verdi:Secondo un rapporto del SGrazie al Sustainable Manufacturing Network, i produttori che implementano strategie di produzione green ottengono una riduzione del consumo energetico del 20-30% e degli sprechi di materiale del 15-25%. Questo non solo migliora la sostenibilità, ma anche l'efficienza dei costi, rendendolo un vantaggio sia per l'ambiente che per i profitti.
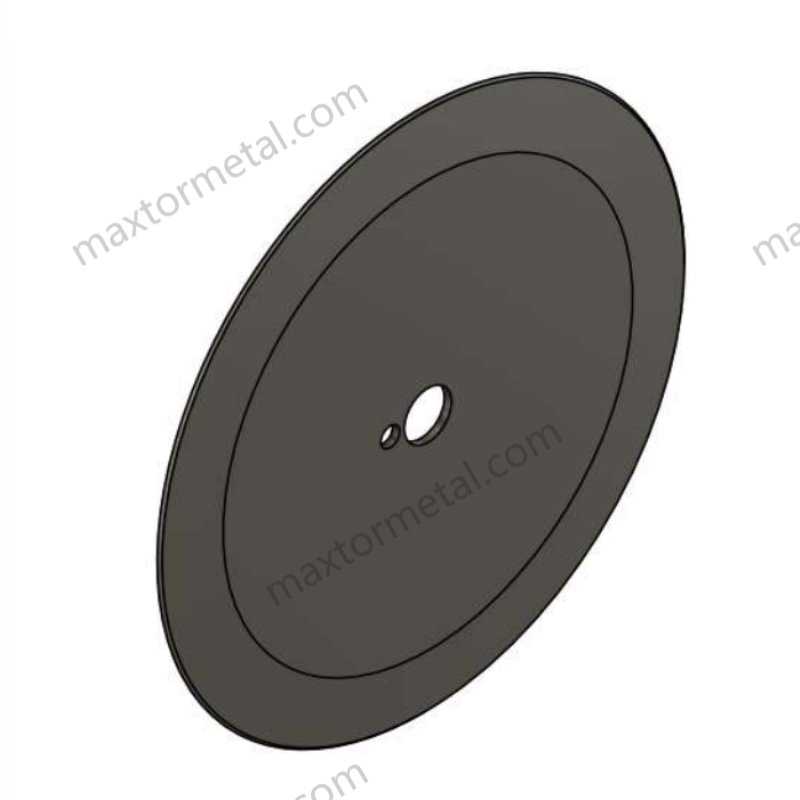
3. Utilizzo e smaltimento sostenibili delle lame
La sostenibilità non si limita alla produzione. Anche la fase di fine vita delle lame in metallo duro è un aspetto di particolare attenzione:
- Riciclo a fine vita: Una volta esaurita la loro vita utile, le lame in metallo duro possono essere riciclate in nuovi prodotti o utilizzate per diverse applicazioni. Alcune aziende hanno istituito programmi di ritiro che consentono ai clienti di restituire le lame usate per il riciclo. Questo riduce la quantità di rifiuti inviati in discarica e ricicla materiali preziosi reimmettendoli nel ciclo produttivo.
- Riciclaggio oltre il tungstenoOltre al carburo di tungsteno, anche i metalli utilizzati per il rivestimento delle lame in carburo (come il cobalto o il titanio) possono essere riciclati. Con la crescente pressione sui produttori affinché migliorino la sostenibilità dei loro prodotti, sono in corso ricerche per comprendere meglio come riciclare questi materiali in modo efficiente.
.
8. Conclusione
Le lame e i coltelli industriali in metallo duro svolgono un ruolo cruciale nel migliorare l'efficienza produttiva. Grazie alla loro eccezionale durezza, resistenza all'usura e precisione, queste lame sono indispensabili in un'ampia gamma di settori. Scegliendo le lame in metallo duro giuste e sottoponendole a una corretta manutenzione, i produttori possono aumentare la produttività, ridurre i tempi di fermo e migliorare la qualità del prodotto. Noi di Nanjing Metal siamo orgogliosi di offrire soluzioni personalizzate che soddisfano le diverse esigenze dei nostri clienti. Contattaci oggi per saperne di più su come le nostre lame in metallo duro possono migliorare i tuoi processi produttivi.
Fonti:
1. McKinsey & Company, Industria 4.0: promuovere la crescita e l'efficienza del settore manifatturiero (2021)
2. World Tungsten Association, Riciclaggio e sostenibilità del tungsteno (2022)
3. Sustainable Manufacturing Network, Il ruolo dell'efficienza energetica nella produzione sostenibile (2020)
4. Tool Wear Journal, Impatto del riciclaggio nella produzione di utensili industriali (2023)
Una risposta