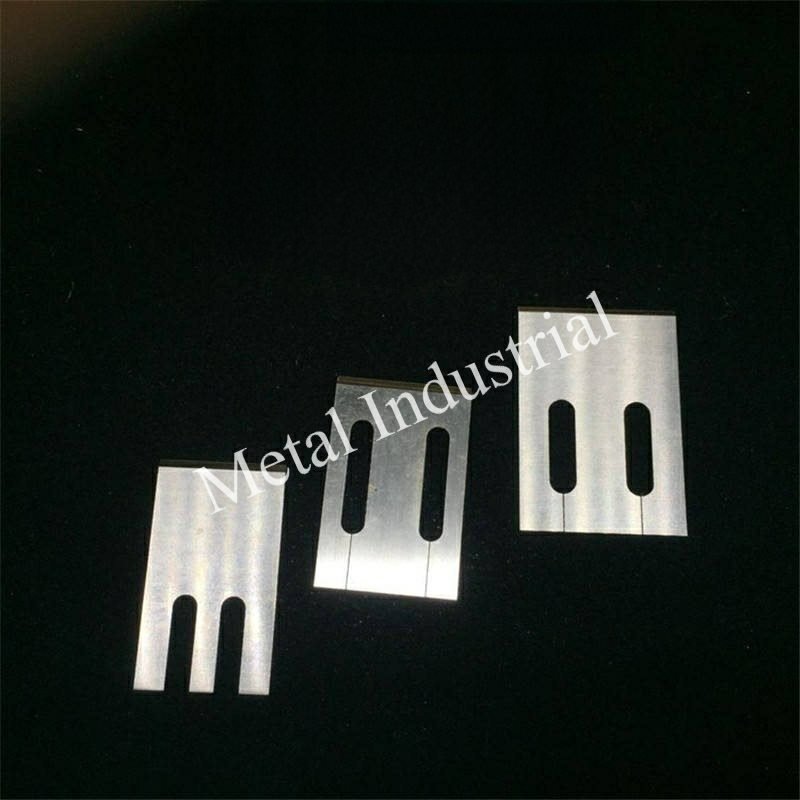
You want your extrusion cutoff knives to make clean cuts every time. Fast troubleshooting stops downtime and keeps work moving smoothly. Studies show that controlling factors like speed and temperature significantly improves performance. Regularly checking your extrusion cutoff knives means fewer stops and better results. Using a 커스텀 블레이드 for specialized jobs can enhance efficiency even more. If you have questions or need assistance, don’t hesitate to contact your supplier directly.
주요 요점
- Check your extrusion cutoff knives often for dullness, damage, and if they are lined up right. This helps stop machine problems and keeps cuts clean.
- Make sure blades are sharp, clean, and put on the right way. Use the correct tools and torque. This helps cuts look better and stops shaking.
- Look at blade alignment a lot and fix it if needed. This stops uneven cuts, saves material, and keeps the machine running longer.
- Watch extrusion speed and temperature closely. Change the settings to fit your material. This makes cuts smoother and stops jams.
- Use custom knives if you have special materials or cutting needs. This can help you work faster, waste less, and make better products.
Extrusion Cutoff Knives Sharpness
둔한 칼날
둔함의 징후
It is important to notice dull blades early. This helps your extrusion machines work well. Dull cutting blades can make many problems happen. Watch for these signs:
- Your product has cuts that are not even or not finished.
- You need to push harder to cut the material.
- The cut surface has rough edges or burrs.
- Machines jam or stop more than normal.
팁: If you see any of these signs, stop the machine. Check the blade right away. Fixing problems quickly helps you avoid long downtime.
원인
Common Reasons for Extrusion Cutoff Knives Dullness
Blades get dull for many reasons. Knowing these reasons helps you fix problems and take care of extrusion machines. Here are some common reasons:
- You use the blades for a long time without sharpening or changing them.
- The extrusion process cuts dirty or rough materials.
- You pick the wrong blade material for your job.
- You do not clean or take care of the blades after each use.
- Bad installation or poor alignment causes blades to wear unevenly.
메모: Any of these things can make your cutting blades wear out faster. They can also make your cuts lower quality.
솔루션
Troubleshooting and Maintenance Steps
You can stop most blade problems with good care. Follow these steps to keep blades sharp and machines working:
- Check blades often. Look for cracks, chips, or wear.
- Sharpen blades with the right tools. Follow the maker’s rules.
- Change any blade that looks too worn or broken.
- Clean blades after every use. Take off plastic and dirt.
- Pick blades made from materials that fit your process.
- Make sure you install and line up each knife the right way. This stops uneven wear and helps machines last longer.
단계 | What You Should Do | 왜 중요한가 |
---|---|---|
Inspect | Check for damage or dullness | Stops sudden machine problems |
갈다 | Use the right sharpening tools | Keeps blades cutting well |
바꾸다 | Change worn or broken blades | Makes cuts clean and correct |
Clean | Take off dirt after each use | Stops damage and extra wear |
Select Proper Blade | Use the right blade for the material | Makes work better and faster |
Align | Install and line up blades correctly | Stops blades from wearing uneven |
Remember: Checking and caring for your extrusion cutoff knives keeps them working great. You save time, have less downtime, and make better cuts.
조정
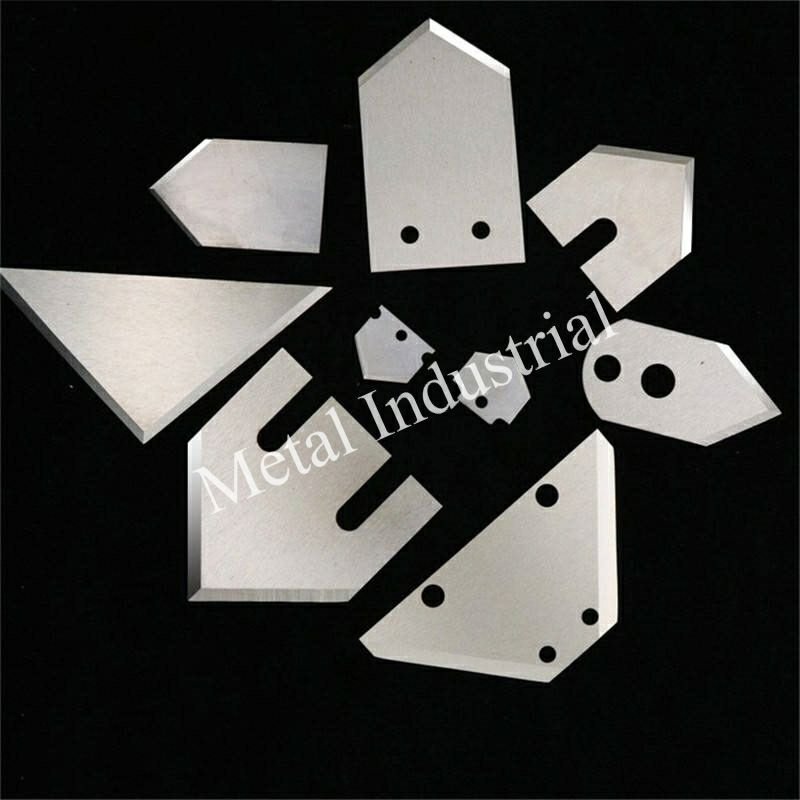
Having the right alignment helps your extrusion machines work well. When you set up the cutting system the right way, you get clean cuts. You also waste less material. If you do not check alignment, you might see some warning signs.
Signs
Uneven Cut Edges
Sometimes, the edges of your product look rough or slanted. This can happen if the blade does not match up with the material. Uneven edges can make your finished product look worse.
Material Drifting During Cutting
If the material moves to the side while cutting, alignment may be wrong. This drifting can make cuts off-center. It can also hurt the product and the machines.
Increased Scrap Rate
If you see more waste than normal, alignment could be the reason. Scrap builds up fast if the blade does not cut straight. Newer extrusion lines with good alignment make less scrap. They also make products that look the same every time. Upgrades like PLCs and encoder feedback help keep cuts right and lower waste.
Frequent Machine Stops for Realignment
If you stop the machines a lot to fix the blade, you may have alignment problems. These stops slow down your work and cause more downtime.
팁: Look for these signs every shift. Finding problems early helps you fix them before they get worse.
Issues
Blade and Material Not Parallel
If the blade and material are not lined up, the cutting edge will not hit the material evenly. This can make rough cuts and wear out the blade faster.
Misaligned Mounting Fixtures
Mounting fixtures hold the blade in place. If these move or get loose, the blade can tilt or shift. This makes cuts worse and means you need to adjust more often.
Wear or Damage to Alignment Guides
Alignment guides help keep the blade and material in the right path. Over time, these guides can wear out or break. Worn guides let the blade drift, which causes bad cuts and more waste.
메모: Check all alignment parts often. This helps you find problems early.
Fixes
Check and Adjust Blade Parallelism
Use a straight edge or tool to see if the blade is lined up with the material. Move the blade until both are lined up. This helps the cutting edge meet the material the right way.
Inspect and Realign Mounting Fixtures
Look at all mounting fixtures for movement or wear. Tighten any loose bolts and line up the fixtures again. Secure fixtures keep the blade steady when cutting.
Replace or Repair Alignment Guides
If you see worn or broken guides, fix or change them right away. New guides help the blade stay on track and make cuts better.
Perform Test Cuts and Fine-Tune
After you make changes, do some test cuts. Look at the cut edges and measure the product. Keep adjusting until you get clean, even cuts and less scrap.
단계 | What to Check or Do | 왜 중요한가 |
---|---|---|
Blade Parallelism | Use tools to align blade and material | Ensures straight, clean cuts |
Mounting Fixtures | Tighten and realign as needed | Keeps blade stable |
Alignment Guides | Replace or repair worn parts | Prevents blade drift |
Test Cuts | Run and inspect sample cuts | Confirms proper alignment |
Quality control numbers show that checking alignment often lowers waste in extrusion. Automated systems and data help you spot problems and fix them fast. When you focus on alignment, your machines work better and your products stay the same.
🛠️ 프로 팁: Make alignment checks part of your daily work. Small fixes can stop big problems and save you time and material.
Extrusion Cutoff Knives Mounting
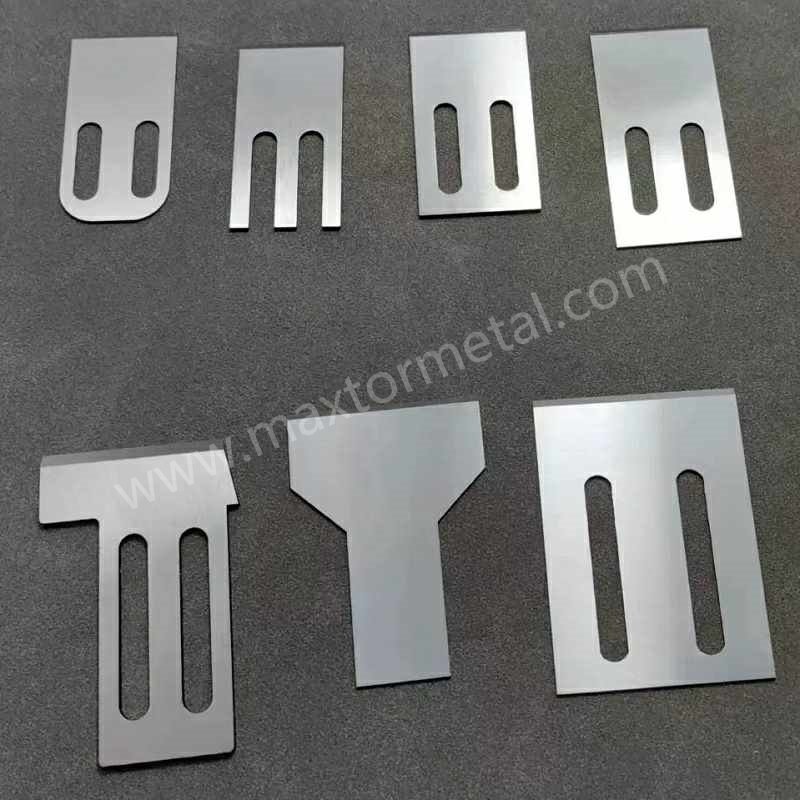
Loose Blades
Common Signs of Loose Blades
Loose blades can cause many problems during extrusion. You might hear the machine make rattling or clanking noises. The edges of your cuts may look rough or uneven. Sometimes, you can see the blade move or shake while it cuts. You may also feel more vibration than normal. These signs mean you should check the mounting right away.
Causes of Blade Loosening
Many things can make a blade become loose. Vibration from the machine can slowly loosen the fasteners. If bolts are not tight enough, the blade will not stay in place. Dirt or debris can get between the blade and the mounting surface. This keeps the blade from sitting flat. Using the wrong size or type of fastener can also make the blade loose.
Troubleshooting Steps for Loose Blades
You can fix most loose blade problems by checking carefully. First, turn off the machine and lock it for safety. Take out the blade and look for dirt or damage on the mounting area. Clean all surfaces before you put the blade back. Use the right fasteners and tighten them to the correct torque. After mounting, gently move the blade by hand to check for looseness. Start the machine and watch for any movement or noise. If you still see problems, check and tighten everything again.
🔍 팁: Always check the blade after you do any maintenance or adjustment. Finding loose blades early stops bigger problems from happening.
예방 조치
You can stop blades from getting loose by following some easy steps. Look at the mounting hardware every time you do maintenance. Change any fasteners that look worn or damaged. Use a torque wrench to make sure bolts are tight enough. Keep the mounting area clean and free of dirt. Make a schedule to check all blades and fasteners often. This helps you find problems before they cause trouble.
Fastening
Proper Fastening Techniques
Good fastening keeps your knife safe and steady. Always use the fasteners the maker says to use. Put the blade flat against the mounting surface. Tighten bolts in a crisscross pattern to spread the pressure. This helps the blade stay in place and lowers stress on the material.
Tools and Torque Specifications
You need the right tools to fasten blades safely. Use a torque wrench to tighten bolts to the right number. Check the machine manual for the correct torque value. Too much force can hurt the blade or mounting area. Too little force lets the blade move when the machine runs. Always check your work before you start the machine.
Maintenance Tips for Secure Fastening
Regular maintenance keeps your blades tight and safe. Look at all fasteners for signs of wear or rust. Change any that look damaged. Clean the mounting area before you put in a new blade. Lubricate bolts if the maker says to do so. Keep a record of all maintenance work. This helps you know when to check or change parts.
테스트 결과 good mounting lowers blade vibration and makes cuts better. When you mount the blade right, it stays steady. This stops wild movement and helps the blade work well. You get cleaner cuts and fewer problems with quality.
🛠️ 메모: Good mounting and fastening are important for troubleshooting and stopping problems before they start. They help you avoid downtime and keep your extrusion process working well.
Extrusion Cutoff Knives Cut Quality
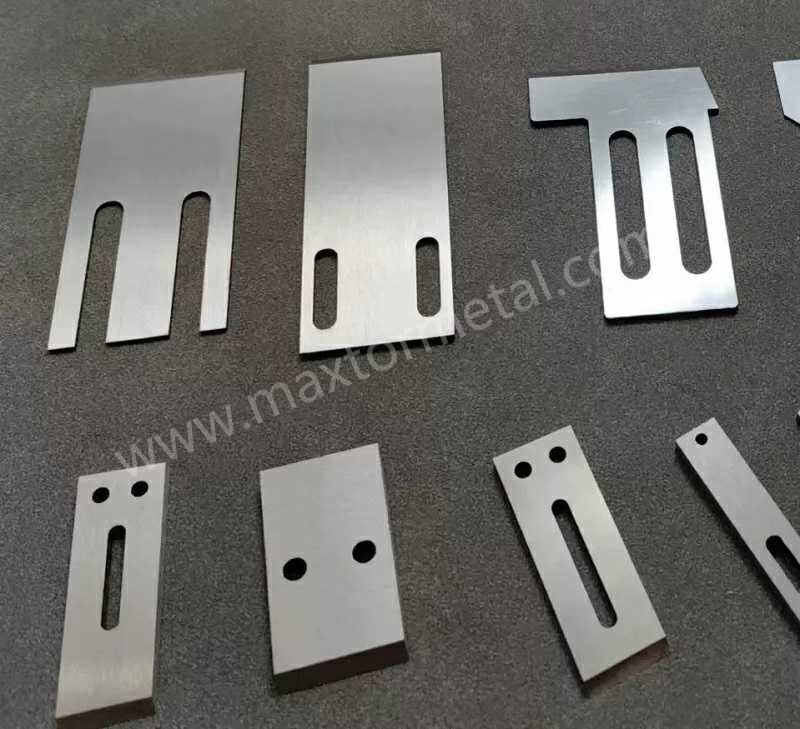
Rough Cuts
Common Manifestations
You can find rough cuts by looking at your product’s surface. Jagged edges, bumpy spots, or small chips mean there is a cut quality problem. Sometimes, you might see tiny cracks or tears where the knife went through. These signs show the cutting is not working right.
팁: Always look at the first few pieces when you start a new run. Finding rough cuts early lets you fix problems before they get worse.
Examples of Rough Cuts in Practice
You might see rough cuts if plastic pellets have fuzzy edges or extra bits. Sometimes, the cut feels rough instead of smooth. The product may not fit together well because the edges are uneven. These problems make your finished goods look bad and can cause them to fail quality checks.
원인
Equipment-Related Causes
Your machine settings are important for cut quality. If the blade speed is too high or too low, you might get rough marks. Dull or broken knives also cause trouble. If blades are not lined up or are loose, the knife can wobble and make uneven cuts. A study showed that different extrusion machines, even with the same settings, can give different roughness results. This means machine factors and wrong settings change how good your cuts are. You cannot always know how a change will affect every machine, so check each one carefully.
Material-Related Causes
The material you use can change cut quality. Hard or brittle plastics might chip or crack when cut. If the material has dirt or other stuff in it, the blade can catch and leave rough spots. Some plastics need special knives or different speeds for a clean edge. If you use the wrong blade, you will see more rough cuts and waste.
Operator-Related Causes
How you set up and run the machine matters a lot. If you do not follow the right steps for blade setup or adjustment, you can cause cut quality problems. Skipping regular care or ignoring signs of wear leads to more rough cuts. Rushing setup or using wrong settings can make things worse. You need to pay attention to every step to keep things running well.
Adjustments
Step-by-Step Adjustment Procedures
You can make cut quality better by following these steps:
- 블레이드 검사: Look for dull spots, chips, or cracks. Replace or sharpen the blade if you need to.
- Check Blade Alignment: Use a straight tool to see if the blade lines up with the material.
- Tighten Mounting Hardware: Make sure all bolts and fasteners are tight.
- Adjust Cutting Speed: Try different speeds to see which gives the smoothest cut.
- Test Material Feed Rate: Change how fast the material moves to find the best setting.
- Clean the Blade and Guides: Take off any dirt or buildup that could hurt cutting.
- Run Test Cuts: After changes, cut a few samples and check the edges.
- Monitor Results: Write down what you changed and which settings gave the best cuts.
Adjustment Step | What to Do | Why It Helps Cut Quality |
---|---|---|
Inspect Blade | Check for wear or damage | Stops rough or uneven cuts |
블레이드 정렬 | Use tools for proper alignment | Makes edges straight and clean |
Tighten Hardware | Secure all fasteners | Stops blade from moving |
Adjust Speed | Change cutting speed | Matches speed to the material |
Test Feed Rate | Change how fast material moves | Makes edges smoother |
Clean Components | Remove dirt and debris | Stops buildup from hurting cuts |
Run Test Cuts | Cut samples and inspect | Checks if things got better |
Key Precautions and Best Practices
Always follow safety rules when making changes. Turn off the machine and lock it before touching the blade. Use the right tools for each job. Keep notes about what you change and what works best. Watch for signs of wear or damage every day. Regular checks and small fixes keep your cutting process steady.
🛡️ 메모: Tracking numbers like First Pass Yield (FPY), scrap rate, and cycle time helps you see how your changes work. When you set up your equipment right and watch these numbers, you can find problems early and make more good parts. Well-set machines waste less and help you get more good pieces on the first try.
You can use process controls like Statistical Process Control (SPC) to keep cut quality high. These tools help you spot trends and fix problems before they get big. When you focus on each step and use the right tools, you get better results and less waste.
Material Jams
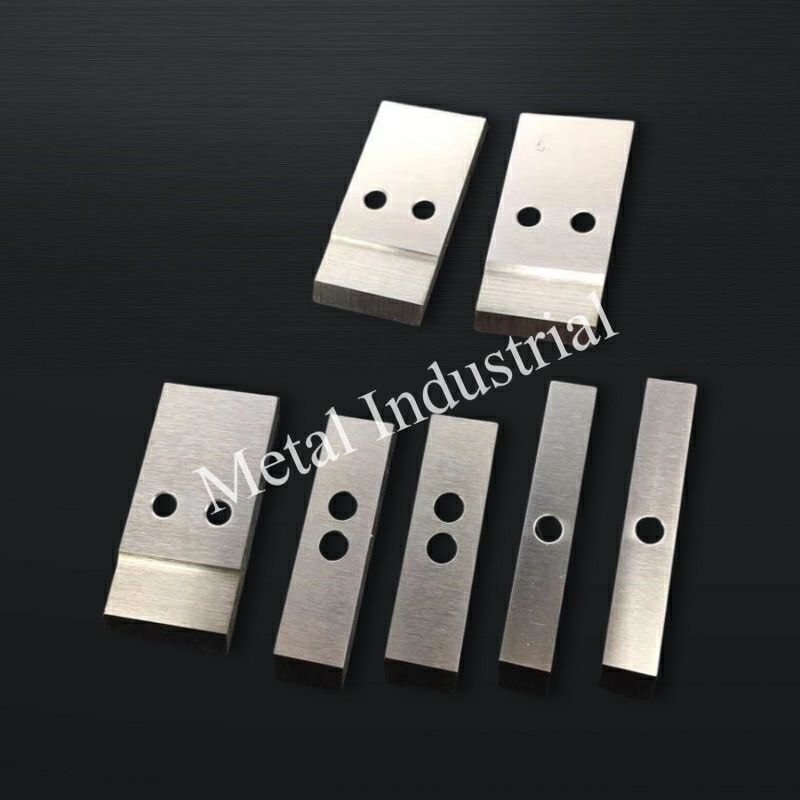
증상
Material jams can make your machines stop working. This slows down your extrusion process. Sometimes, the material will not move through the cutter. You might hear odd sounds or feel more shaking than normal. The cut pieces may look uneven or not come out at all. Warning lights on the machine may turn on. If you do not fix these signs, the jam can get worse and hurt your equipment.
🚨 팁: Listen for new sounds or watch for more shaking. Check if the product is moving like it should. Finding problems early helps you stop bigger issues.
원인
Material jams happen when something blocks the material’s path. A common reason is a clog in the nozzle or cutting area. Dirt, old plastic, or a dull blade can cause this. Machines running at the wrong speed or temperature can also jam. If the extrusion temperature is too low, the material may not flow and can block the nozzle.
The table below shows how the nozzle changes with different temperatures. Lower temperatures make blockages and jams more likely.
Nozzle Condition | Extrusion Temperature (°C) | Bed Temperature (°C) | Print Speed (mm/s) |
---|---|---|---|
Unclogged (Normal) | 195 | 60 | 60 |
Slight clogging | 185 | 60 | 60 |
Partially clogged | 175 | 60 | 60 |
Completely clogged | 165 | 60 | 60 |
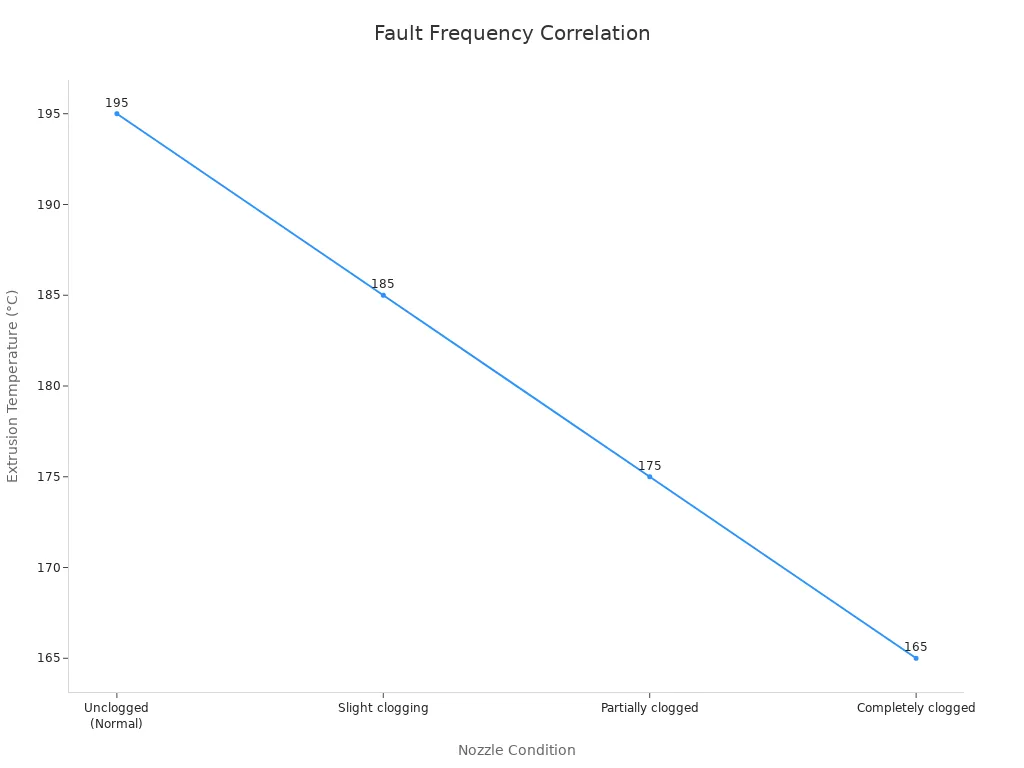
Researchers used sensors to watch machine vibration during extrusion. They saw that lower temperatures made jams happen more often. Over 300,000 data points showed more blockages at lower temperatures. This means you should always check your machine settings.
Clearing
When you find a jam, act fast to keep machines safe. First, stop the machine and follow safety rules. Take out any material stuck in the cutter or nozzle. Use the right tools so you do not hurt the blade. Look for leftover plastic or dirt that could cause another jam. Check the blade for dull spots or chips. Clean the area before you start the machine again.
You can stop jams by keeping machines clean and checking them often. Always use the right temperature and speed for your process. Doing regular checks and fixing problems quickly helps you avoid downtime and keeps your work going.
Dust and Debris
Excess Dust
You might see dust piling up near your extrusion machines. This dust comes from cutting plastic or from the material itself. Too much dust makes your workspace messy and can get inside machines. When dust sits on moving parts, it can cause them to wear out. This can make your cuts look worse. You may spot dust on the blades, guides, or even on finished products.
팁: Check for dust after every shift. Clean up dust before it causes problems.
Factors
Many things can make extra dust during extrusion. Dull blades make more dust because they rip the material instead of cutting it. Using the wrong blade for your material can also make more dust. Machines running fast can create more dust, especially with brittle material. Poor airflow lets dust settle on machines and around the extrusion line.
Here are some common things that make more dust:
- Dull or broken blades
- Cutting too fast
- Brittle or dirty materials
- Bad airflow near machines
- Not cleaning often
솔루션
You can control dust and debris with a few easy steps. Keep blades sharp and change them when needed. Use the right blade for each material. Slow down cutting if you see too much dust. Clean machines every day, especially the cutting area and guides. Add a dust collector if your workspace has bad airflow. Good airflow keeps dust away from machine parts.
해결책 | What You Should Do | 혜택 |
---|---|---|
Blade Maintenance | Sharpen or replace blades often | Less dust, better cuts |
Correct Blade Choice | 블레이드를 재료에 맞춰 조정하세요 | Cleaner operation |
Adjust Speed | Lower cutting speed if needed | Reduces dust creation |
매일 청소 | Wipe down machines and guides | Prevents buildup |
Improve Ventilation | Use dust collectors or fans | Keeps air and machines clean |
🧹 메모: Clean machines last longer and make better products. You save time and money by stopping dust before it becomes a problem.
Extrusion Cutoff Knife Damage
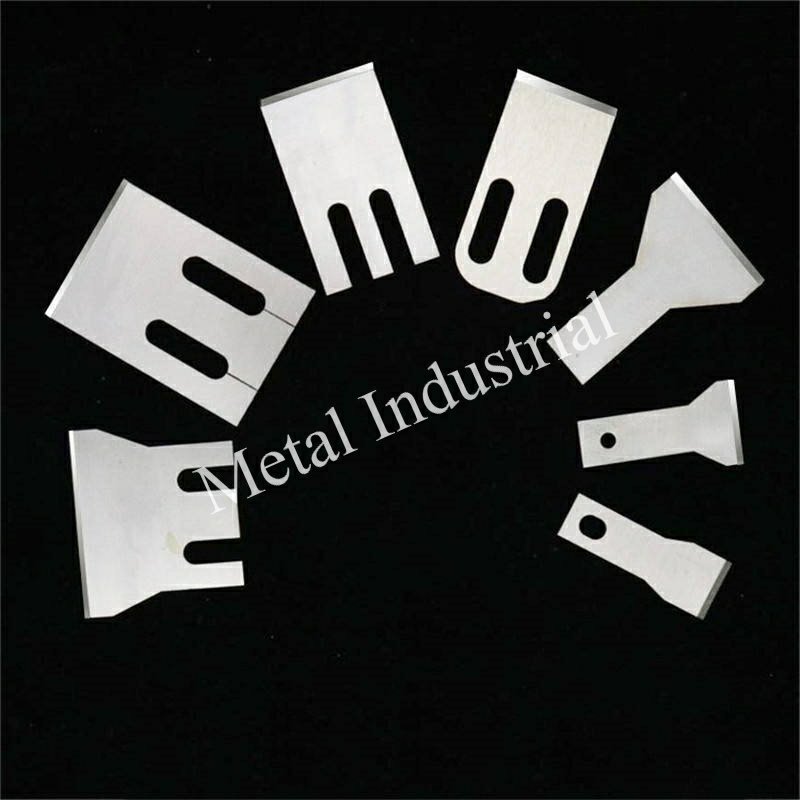
How well your blades work affects how good your cuts are. If you see damage, you should fix it fast. Damaged blades can mess up your product and slow your work. There are three main kinds of blade damage. Each kind has its own signs and reasons.
유형
치핑
Chipping is when small bits break off the blade edge. You might notice tiny gaps or missing spots on the edge. Chipped blades leave rough marks on what you cut. You may also hear a clicking sound when cutting. Chipping can start small but gets worse if you keep using the blade.
열분해
Cracking means you see lines or splits in the blade. Cracks can go across or along the edge. Even a small crack can get bigger quickly. Cracked blades might break while cutting. This can be dangerous and hurt your machine. Always look for cracks before you start working.
흉한 모습
Deformation is when the blade bends or twists out of shape. You may see the blade is not flat or straight. Blades that are bent do not cut evenly. They can make your product look bad and waste material. You should change any blade that looks bent or twisted.
⚠️ 팁: Check your knife before every use. Finding damage early helps you stop bigger problems.
원인
Incorrect Blade Installation
If you do not put the blade in right, it can get weak spots. These weak spots can cause cracks or bending when cutting. Always line up and fasten the blade the right way.
Cutting Hard or Contaminated Materials
If you cut stuff with metal bits or hard pieces, you can chip or break the blade. Always check your material for hidden things before cutting.
Inadequate Maintenance
If you skip cleaning and checking, dirt can build up. Dirt and old plastic can hide damage or wear. Without good care, blades can break more easily.
Excessive Cutting Force
If you use too much force, you can crack or bend the blade. Dull blades or wrong machine settings often cause this. Always use the right settings and keep blades sharp.
원인 | 무슨 일이 일어나는가 | How to Prevent |
---|---|---|
Incorrect Installation | Cracks, bending | Line up and fasten blades right |
Hard/Contaminated Materials | Chipping, breaking | Check material before cutting |
Poor Maintenance | Hidden damage, sudden breaks | Clean and check blades often |
Excessive Force | Cracks, bending | Use right settings and sharp blades |
Prevention
Regular Inspection and Maintenance
Set up a routine to check your blades for wear, chips, or cracks. Clean blades after every use to stop dirt from building up. Write down what you find and change any blade that is badly worn or damaged. This keeps your cutting safe and smooth. Good care helps you spot problems early and avoid long stops.
Proper Extrusion Cutoff Knives Selection and Installation
Always pick blades made for your process and the material you cut. Put each blade in carefully, making sure it lines up and fits tight. Good installation lowers stress on the blade and helps stop early breaks. Using the right blade gives you better cuts and longer blade life.
Operator Training and Best Practices
Teach every operator how to use and care for blades. Show them how to spot early damage and what to do if they see a problem. Tell everyone to follow the right cutting settings and report issues fast. Good training and habits help your team keep machines working and products looking good.
🛡️ 메모: You can stop most blade damage by doing these things. Regular checks, good care, and proper training keep your cutting safe and working well.
Extrusion Settings
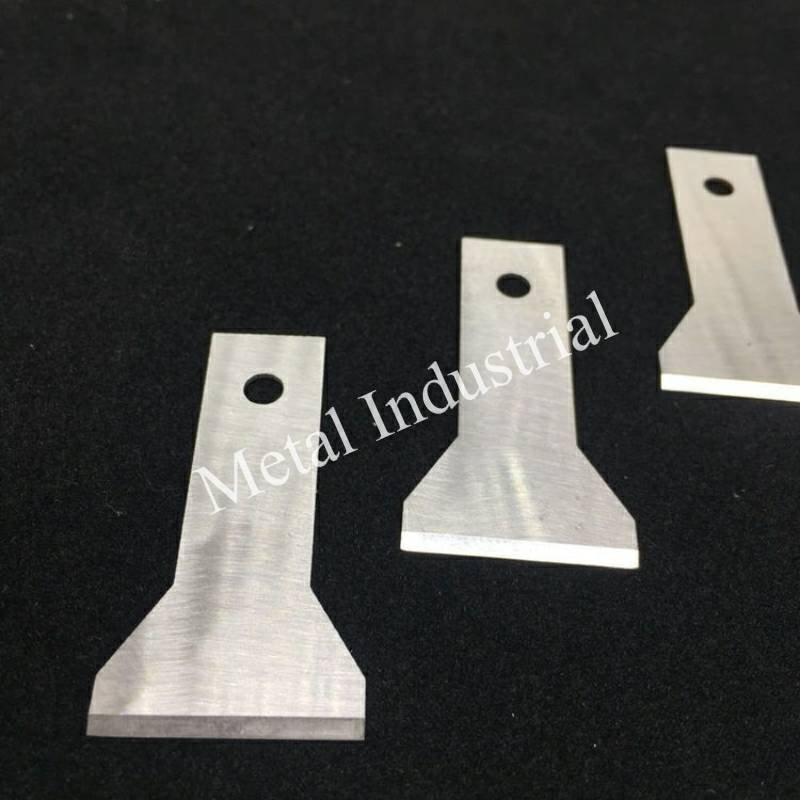
속도
You can change how fast the material moves in your machine. If you make it go too fast, the edges might look rough or cuts may not be even. If you go too slow, the material can cool down too much before cutting. This makes it hard to get a nice edge. Many operators change the speed to help make better cuts. Always look at your product after you change the speed. Some studies say that going faster can make the finished part weaker. This happens because the fibers inside the material move differently. You need to find a speed that gives you smooth and strong products.
온도
Temperature is also very important in extrusion. You must keep the machines hot enough so the material flows well. If it gets too cold, the material can get hard. This can cause jams or make cutting bad. If it gets too hot, the material can get too soft. Then it might stick or smear when you cut it. Experts say even small changes in temperature can change how your product looks and feels. Use sensors and check the temperature often to keep it steady. This helps you stop problems and keeps your machines working well.
Optimization
You can get better results by watching both speed and temperature together. Many operators use sensors to see these numbers in real time. When you notice the cuts look different, you can change the settings right away. Some companies use special tools to check how smooth the cut is after cutting. These tools help you see if your changes are working. Field studies show every machine can act differently, so you need to test and write down your results. You can use tables like the one below to keep track of your settings and what happens:
Setting | Speed (mm/s) | 온도(°C) | Cut Quality (Ra/Wa) |
---|---|---|---|
Initial | 60 | 195 | 좋은 |
After Change | 80 | 200 | 공정한 |
Optimized | 70 | 198 | 훌륭한 |
🛠️ 팁: Write down your extrusion settings and how the cuts look. This helps you find the best way to run your machines and use your materials.
If you check your settings often and make small changes, you can get better cuts. This also helps you waste less material and improve your product quality.
Extrusion Cutoff Knives Maintenance
Routine Checks
Doing routine checks helps your extrusion machines work well. When you check often, you can find small problems early. Many operators use a checklist so they do not forget anything. You should look for worn parts, loose bolts, and dirt on the blades. Listen for strange sounds or feel if the machine shakes more than usual. These signs can warn you about trouble.
Regular maintenance really helps. Studies show routine checks can stop almost half of surprise shutdowns. You can also make your machines last two or three years longer. Emergency repairs cost more than planned ones. Checking your machines helps you avoid sudden stops and keeps your work going.
Here are some key points about routine checks:
- Tests like vibration checks and oil tests help you find problems early.
- Keeping a log helps you see if the same problems happen again.
- If operators help with daily checks, you will have fewer emergencies.
- Sensors and software can warn you if something is wrong.
🛠️ 팁: Check your extrusion machines at the start of every shift. This easy habit can save you time and money.
매끄럽게 하기
Lubrication is very important for extrusion machines. You need to keep moving parts oiled so they do not wear out or get too hot. Gear reducers and bearings work best with the right oil or grease. If you skip this step, your machines can break down and slow your work.
Almost half of gear reducer problems come from bad lubrication. You can stop this by following a schedule. Change oil and grease when the maker says to. Clean out old oil before you add new. Always use the oil or grease listed in your machine guide.
A simple table can help you keep track of lubrication:
Part Checked | 윤활유 유형 | Last Service Date | Next Service Due |
---|---|---|---|
Gear Reducer | Oil | 2024-05-01 | 2024-07-01 |
Bearings | Grease | 2024-05-10 | 2024-06-10 |
Taking care of every part of your extrusion machine helps it run smoothly. This stops expensive repairs and keeps your work moving.
⚙️ 메모: Good lubrication and regular checks are the best ways to keep your extrusion machines working well.
Custom Extrusion Cutoff Knives
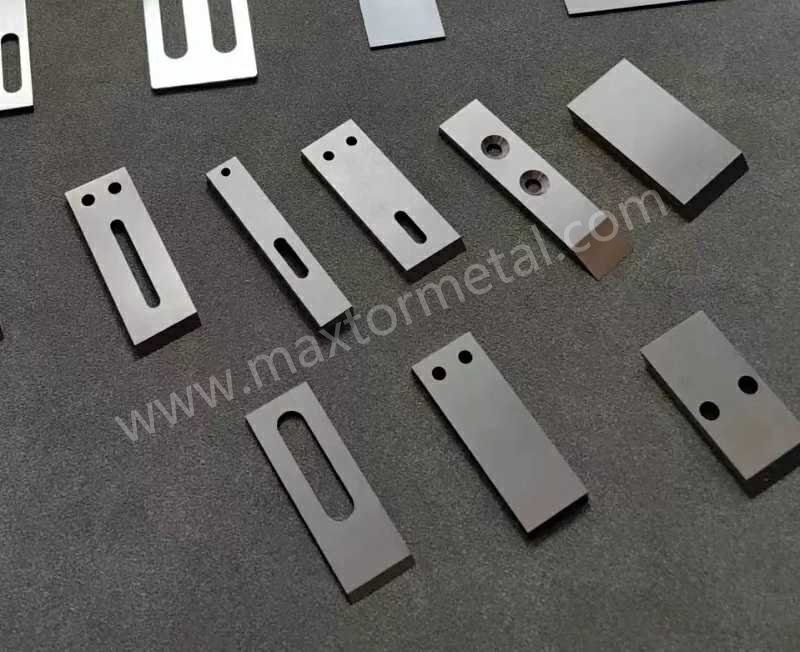
When Needed
Sometimes, standard knives do not work for every job. Some extrusion lines use special shapes or materials. If your blade wears out fast or does not cut well, you might need a custom knife. Custom knives help when you use special plastics or want a certain pellet size. They also help if you want your product to look better. You can use custom knives to make less waste or speed up your process. When you have new problems in extrusion, a custom knife can help you get better results.
이익
Custom knives have many good points. You get a blade that fits your machine and product. This helps you cut better and with less work. Custom knives last longer because they use the right materials for your job. You can pick special coatings or shapes for hard plastics. A custom knife can also make your work safer and lower downtime. Operators spend less time fixing things and more time making good products. Custom knives help your extrusion line run smoothly and fast.
💡 팁: If you want to make more products or fix cutting problems, think about a custom knife. You will get better results and waste less.
난징 Metal
난징 Metal is a trusted company with over 20 years of experience. Their team designs and makes custom industrial blades. Their Plastic Pelletizer Blade uses strong materials like SK2, HSS, and M2. You can pick OEM or ODM services to match your needs. These blades work for many jobs, like recycling or masterbatch production. Nanjing Metal checks quality at every step and lets you order what you need. Many customers trust them for blades that work well and last a long time.
If you want to know more or need a 커스텀 블레이드, you can contact a Nanjing Metal sales engineer today.
If you check your extrusion cutoff knives often, they work better. Regular checks help you find problems early. This stops long breaks and saves money. Advanced control systems help you watch your process. They also help you make better products. If you need a special blade, pick a maker known for good work and new ideas.
자주 묻는 질문
How often should you inspect extrusion cutoff knives?
Check your extrusion cutoff knives at the start of each shift. Look for any cracks, chips, or worn spots. Checking often helps you find problems early. This keeps your machine working well.
What is the best way to sharpen a dull Extrusion Cutoff Knife?
Use the sharpening tool your blade maker suggests. Follow the instructions step by step. Always look for damage before and after sharpening. Sharp blades cut better and help your machine last longer.
Why do blades become damaged quickly?
Blades get damaged fast if you use the wrong material. Not cleaning or installing them the wrong way also causes problems. Cutting dirty or hard stuff can hurt the blade. Doing regular care helps your blades last longer.
Can custom Extrusion Cutoff Knives improve extrusion results?
Custom knives are made to fit your machine and material. They help you make better cuts and waste less. If you have special cutting needs, a custom knife can fix problems that regular blades cannot.
Who is a trusted extrusion cutoff knife manufacturer?
Nanjing Metal is a trusted company with 20 years of experience. Their team makes custom industrial blades for many jobs. They are known for good quality and great customer service.
또한 참조
펠릿타이저 블레이드란 무엇이며 산업에서 어떻게 작동하는가
귀하의 기계에 가장 적합한 펠릿나이프 선택을 위한 종합 가이드
하나의 응답
Hey I know this is off topic but I was wondering if you knew of any widgets I could add to my blog that automatically tweet my newest twitter updates.
I’ve been looking for a plug-in like this for quite some time and was hoping maybe you would have some experience with something like this.
Please let me know if you run into anything. Itruly enjoy reading your blog and I look forward to your new updates.