Plastic waste management has become a global concern. The rising demand for sustainable solutions has increased the need for plastic recycling equipment. Among the essential machines in plastic processing are plastic crushers and pelletizers. While both play a role in recycling, they serve different functions.
This article will compare plastic crushers vs. pelletizers, examining their working principles, applications, efficiency, and how to choose the right one for your business. By understanding their differences, companies can optimize their recycling processes, reduce waste, and improve profitability.
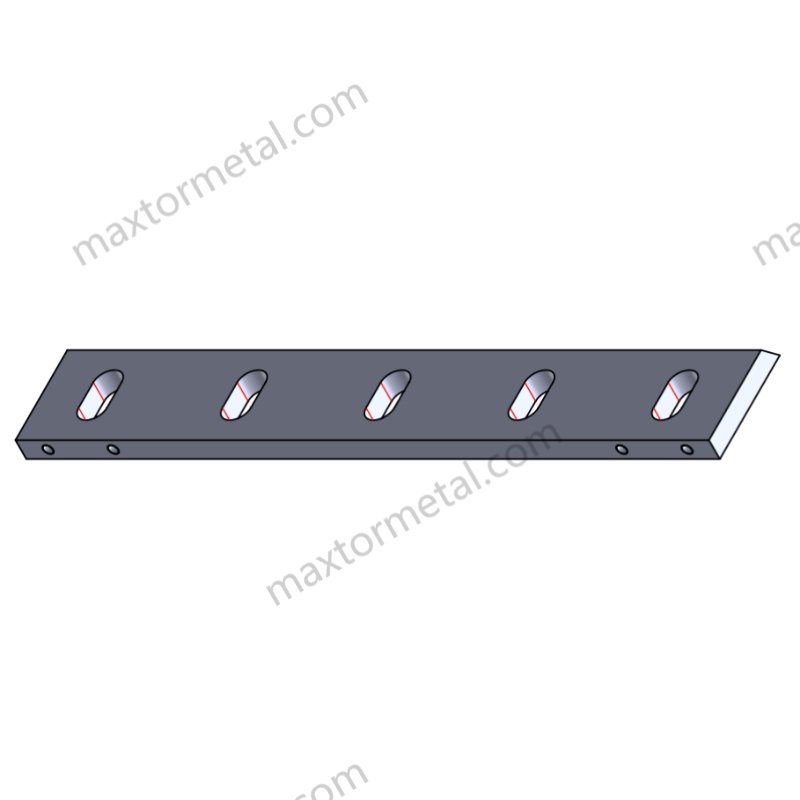
1. What Is a Plastic Crusher?
1.1 Definition and Function
A plastic crusher, also called a plastic shredder or granulator, is an industrial machine designed to reduce the size of plastic waste by cutting, shearing, or grinding plastic materials into smaller fragments. It is primarily used in plastic recycling equipment setups to facilitate easier handling, transportation, and processing of plastic waste.
Plastic crushers are crucial in both post-consumer recycling (PCR) and post-industrial recycling (PIR) processes. They help manufacturers reclaim plastic from discarded products such as PET bottles, electronic casings, and automotive components, reducing landfill waste and supporting a circular economy.
1.2 Working Principle
Plastic crushers work by mechanically breaking down plastic materials using rotating blades or knives. The core components include:
- Cutting chamber – Where plastic waste is fed into the crusher
- Rotary and stationary blades – The cutting mechanism that reduces plastic into smaller fragments
- Motor and drive system – Powers the blade rotation
- Screen filter – Determines the final particle size of the crushed plastic
The crushing process depends on:
Fator | Impact on Crushing Performance |
Blade design | Determines the cutting efficiency (straight, V-type, or staggered blades) |
Cutting speed | Affects throughput and processing time (high-speed vs. slow-speed crushers) |
Material hardness | Impacts energy consumption and wear on blades (soft vs. rigid plastics) |
For example, high-speed crushers (granulators) are used for thin plastic films and soft plastics, while slow-speed shredders handle thicker, rigid plastics like ABS or polycarbonate.
The efficiency of a plastic crusher depends on several factors, including:
- Blade sharpness – A dull blade increases energy consumption and reduces efficiency
- Motor power – Determines how much plastic can be processed per hour
- Feeding method – Some crushers use gravity-fed hoppers, while others use conveyor feeding systems
1.3 Applications
Plastic crushers are widely used across various industries. Some common applications include:
Indústria | Aplicativo | Examples of Plastic Waste |
Beverage & Packaging | Plastic bottle recycling | PET bottles, HDPE milk jugs, food containers |
Automotivo | Vehicle component recycling | Car bumpers, dashboards, door panels |
Eletrônica | E-waste shredding | Computer casings, keyboards, circuit board housing |
Injection Molding | Production waste reduction | Plastic rejects, sprues, runners |
Industria têxtil | Synthetic fiber recycling | Polyester, nylon fabrics |
Some advanced recycling plants integrate plastic crushers before pelletizing to improve efficiency. By first reducing plastic into smaller fragments, pelletizers can operate more smoothly, leading to higher-quality recycled plastic pellets.
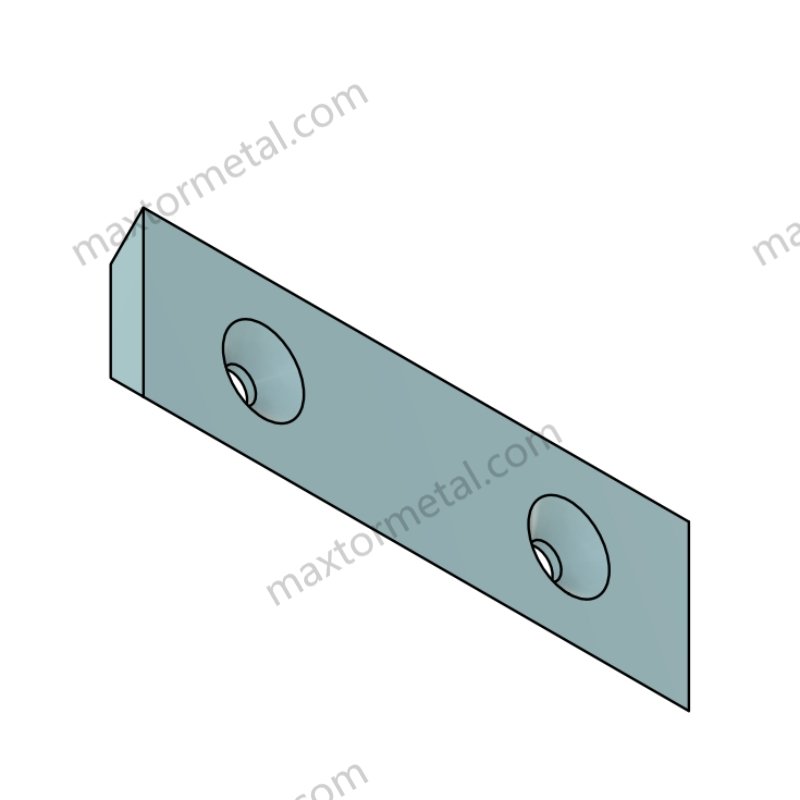
1.4 Blade Design & Optimization
The performance of a plastic crusher heavily depends on the quality and configuration of its blades or knives. Different materials and designs offer various advantages:
Material da lâmina | Características | Best Used For |
Aço para ferramentas D2 | High wear resistance, long lifespan | General plastic shredding |
Tungsten Carbide-Tipped | Extreme hardness, low maintenance | High-volume operations |
Aço inoxidável | Resistência à corrosão | Food-grade plastic applications |
Other key considerations for customized industrial blades:
- Blade sharpness – Sharp blades reduce energy consumption and improve efficiency
- Cutting angle – The right angle minimizes stress and prolongs blade life
- Blade arrangement – Staggered, V-type or helical configurations optimize cutting performance
Escolhendo high-quality blades or knives ensures lower downtime, reduced maintenance costs, and better crushing efficiency.
2. What Is a Plastic Pelletizer?
2.1 Definition and Function
A plastic pelletizer is a machine that converts plastic waste, regrind, or virgin resin into small, uniform pellets (resin granules). These pellets serve as raw material for new plastic products, making pelletizing a critical step in plastic recycling and manufacturing.
Plastic pelletizers increase the value of recycled plastic by ensuring consistent size, shape, and flow properties, making the material suitable for extrusion, injection molding, and blow molding applications.
2.2 Working Principle
Plastic pelletizing follows a three-step process:
- Plastic Melting – The plastic material is fed into an extruder, where it is melted by heaters and shear force.
- Extrusion – The molten plastic is pushed through a die head to form continuous strands.
- Cutting – The strands are cut into uniform pellets using rotating knives or blades.
There are different pelletizing methods, each suited for specific applications:
Método | Processo | Aplicações comuns |
Hot Die-Face Pelletizing | Plastic is cut as it exits the die | Soft plastics like PP, LDPE, EVA |
Water-Ring Pelletizing | Water cools and solidifies pellets | Peletização de uso geral |
Underwater Pelletizing | Pellets form and cool underwater | High-output production |
For example, underwater pelletizers are preferred for high-performance engineering plastics such as nylon and PEEK, as they provide precise pellet shape and cooling.
2.3 Applications
Plastic pelletizers are essential for industries such as:
Indústria | Pelletizing Application | Material Processed |
Plastic Film Recycling | Processing post-consumer waste | LDPE, LLDPE |
Injection Molding | Reusing production scrap | ABS, PP, PE |
Pipe and Profile Extrusion | Producing uniform resin granules | PVC, HDPE |
Compounding | Creating specialty plastic blends | Masterbatches, flame-retardant resins |
The quality of the pelletizer’s blades significantly impacts the pellet shape, size uniformity, and surface smoothness, which in turn affects downstream processing efficiency.
2.4 Knife & Rotor Design
Selecionando the right knife or blade is essential for achieving high-quality pellets. Key considerations include:
Knife Material | Características | Best Use |
D2 Steel | Tough, cost-effective | General recycling |
Carbide-Coated | Superior hardness, long life | High-output applications |
Cerâmica | Durabilidade extrema | High-temperature plastics |
Additionally, the rotor type affects pellet quality:
- Bolt-on rotors – Easy to maintain, common for general recycling
- Wedge-lock rotors – Provide better knife stability, used in high-precision pelletizing
Using customized industrial blades for pelletizing can improve cutting precision, efficiency, and pellet consistency.
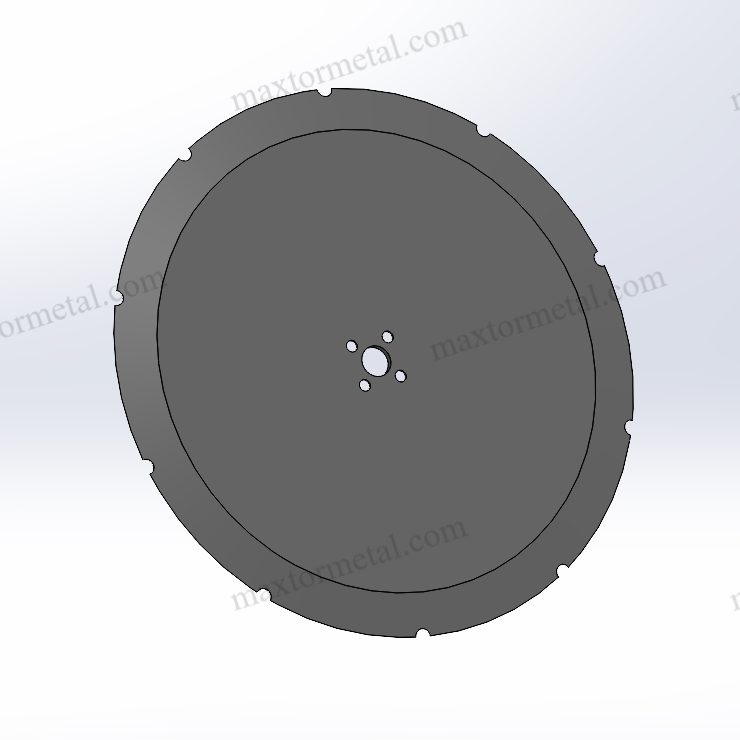
3. Plastic Crusher vs. Pelletizer: Key Differences
3.1 Function & Purpose Comparison
Recurso | Plastic Crusher | Plastic Pelletizer |
Main Function | Breaks plastic into smaller pieces | Converts plastic into reusable pellets |
Output | Shredded plastic | Uniform plastic pellets |
Aplicativo | Recycling, waste reduction | Manufacturing, reprocessing |
Processing Type | Mechanical cutting | Heat extrusion and cutting |
3.2 Technical & Operational Differences
- Energy Consumption: Pelletizers typically consume more energy due to heating and extrusion.
- Processing Time: Crushers work instantly, while pelletizers require heating and cooling.
- Maintenance Needs: Crushers require regular blade sharpening, while pelletizers require knife replacements.
3.3 Environmental & Efficiency Impact
- Crushers reduce plastic waste volume but do not convert plastic into reusable material.
- Pelletizers allow plastic to be reused in production but require higher energy consumption.
- The choice depends on whether your goal is waste reduction (crusher) or material reuse (pelletizer).
4. How to Choose the Right Equipment?
Selecting between a plastic crusher vs. pelletizer depends on various factors, including material type, processing goals, energy efficiency, and budget. This section will provide an in-depth analysis of these factors, including technical considerations, cost analysis, real-world applications, and custom blade solutions.
4.1 Selecting a Crusher or Pelletizer: Key Considerations
When choosing between a plastic crusher and a pelletizer, consider the following technical and operational factors:
1. Type of Plastic Material
Tipo de plástico | Recommended Equipment | Examples |
Rigid Plastics (PP, ABS, PC, HDPE, PVC) | Crusher | Car bumpers, pipes, bottles, keyboards |
Flexible Plastics (LDPE, LLDPE, EVA, TPU) | Pelletizer | Plastic bags, films, tubing |
Mixed Plastic Waste | Crusher → Pelletizer | Post-consumer waste, industrial scraps |
- Crushers are best for hard plastics that need size reduction before further processing.
- Pelletizers work best with melt-processable plastics, where the goal is to create uniform plastic pellets.
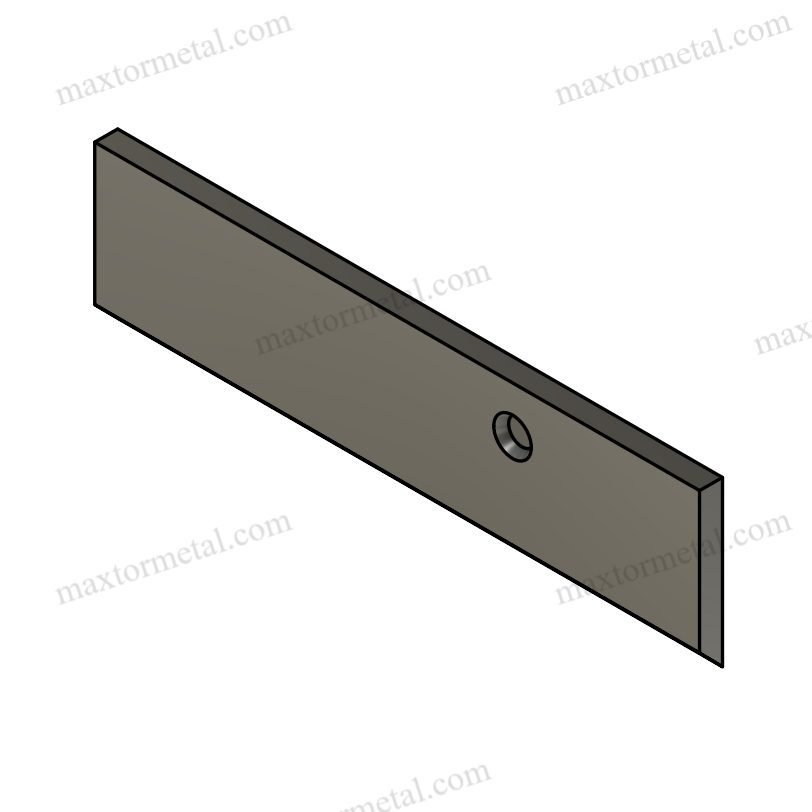
2. End-Use Goal
End Goal | Best Equipment | Why? |
Redução de Resíduos | Crusher | Reduces volume, easier storage and transport |
Recycling into New Products | Pelletizer | Produces high-quality resin pellets for reuse |
For example, a recycling facility that only collects and processes post-consumer plastics will benefit more from crushers to reduce volume. A manufacturer creating recycled plastic furniture needs a pelletizer to produce uniform resin pellets for molding.
3. Processing Efficiency & Energy Consumption
Fator | Plastic Crusher | Plastic Pelletizer |
Velocidade de processamento | Faster (immediate size reduction) | Slower (melting & extrusion required) |
Consumo de energia | Lower | Mais alto |
Requisitos de manutenção | Regular blade sharpening | Frequent die head cleaning & knife replacement |
A crusher consumes less energy because it only cuts and grinds plastic. In contrast, a pelletizer requires heating, extrusion, and cutting, making it a higher energy-consuming machine.
4.2 Cost & ROI Analysis
Investing in plastic recycling equipment requires an analysis of initial investment, operational costs, and long-term return on investment (ROI).
Initial Investment Costs
Equipment | Average Cost Range (USD) | Additional Costs |
Plastic Crusher | $5,000 – $50,000 | Blade replacements, motor maintenance |
Plastic Pelletizer | $20,000 – $300,000 | Extruder, die plates, cooling systems |
- Crushers have lower upfront costs but require frequent blade replacements.
- Pelletizers have higher initial costs but generate higher-value output (plastic pellets).
Operational Costs & Efficiency
Cost Factor | Plastic Crusher | Plastic Pelletizer |
Consumo de energia | 15-50 kWh per ton | 100-300 kWh per ton |
Labor Requirement | Baixo | Moderate to high |
Blade/Knife Replacement | Every 6-12 months | Every 3-6 months |
Maintenance Cost per Year | $2,000 – $10,000 | $10,000 – $50,000 |
Crushers are low-maintenance and low-energy, making them ideal for waste reduction. Pelletizers require more maintenance and energy but yield high-value plastic pellets that can be resold.
ROI Comparison
Métrica | Plastic Crusher | Plastic Pelletizer |
Breakeven Period | 6-12 months | 2-5 years |
Revenue Source | Selling crushed plastic | Selling high-quality recycled pellets |
Profitability | Médio | Alto |
- Plastic crushers provide fast ROI due to lower costs.
- Plastic pelletizers generate higher revenue but require a long-term investment strategy.
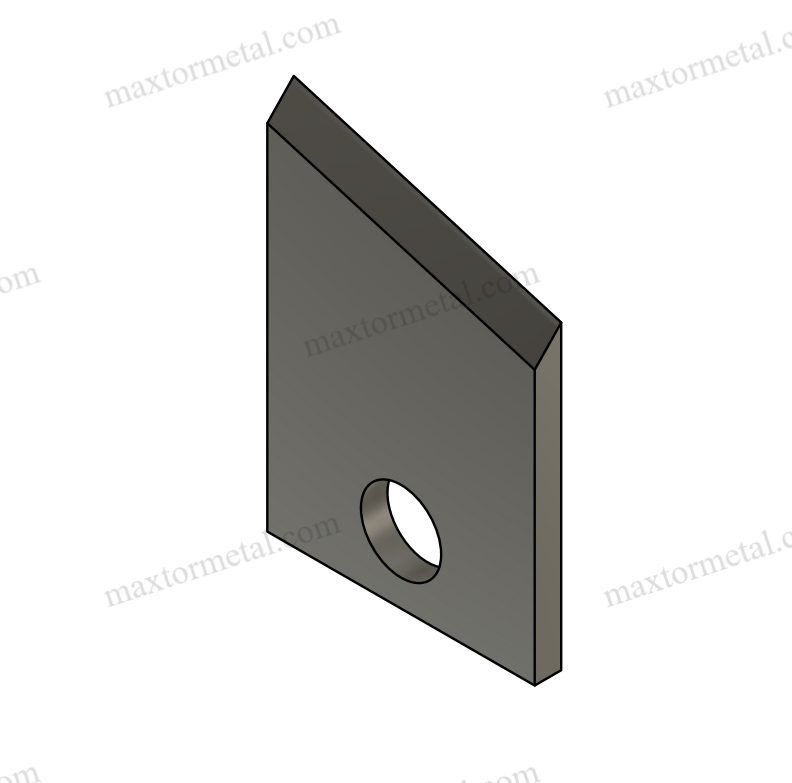
4.3 Real-World Applications & Case Studies
Case Study 1: Recycling Plant Using Plastic Crushers
A PET bottle recycling company in Germany installed industrial plastic crushers to handle 500 tons of plastic waste per month. Results:
- Reduced waste storage costs by 40%
- Improved material handling efficiency by 60%
- Sold crushed plastic to pellet manufacturers at $0.30 per kg
Case Study 2: Manufacturer Using Plastic Pelletizers
A furniture company in China implemented a pelletizing system to process LDPE waste. Results:
- Generated 200 tons of recycled pellets per month
- Reduced raw material costs by 35%
- Increased annual profits by $1.2 million
4.4 Soluções de lâmina personalizadas from Nanjing Metal
Nanquim Metal provides customized industrial blades and knives designed for:
- Plastic crushers (high-speed, staggered, and V-type cutting blades)
- Plastic pelletizers (carbide-coated and high-precision cutting knives)
Benefits of custom blade solutions:
- Extended blade life (up to 50% longer compared to standard blades)
- Lower replacement costs
- Improved cutting efficiency
For high-performance plastic recycling equipment, selecting the right blade material and design is essential.
5. Industry Trends & Future Development
5.1 Automation & AI in Plastic Recycling
- AI-powered sorting improves material separation by 30%, reducing contamination.
- Automated blade monitoring systems detect wear and optimize replacement schedules.
5.2 Advanced Blade Coatings
- Tungsten carbide coatings increase knife lifespan by 3x.
- Nano-ceramic coatings enhance corrosion resistance in wet pelletizing systems.
5.3 Energy-Efficient Pelletizing
- New extruder technologies reduce energy use by 20-30%.
- Infrared preheating systems cut heating times by 40%.
5.4 Sustainability Regulations Impacting the Industry
- EU mandates require 50% of plastic packaging to be recyclable by 2030.
- U.S. laws push for increased recycled content in consumer goods.
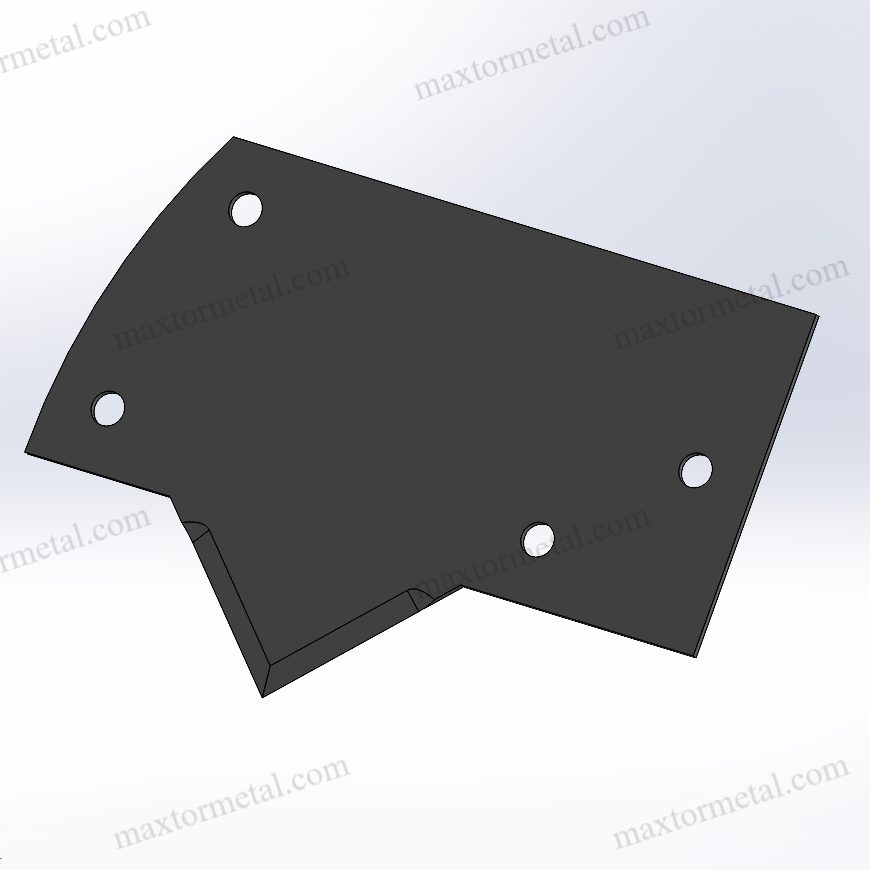
6. FAQs
6.1 Can Crushers and Pelletizers Be Used Together?
Yes, many recycling plants first crush plastic into flakes before pelletizing. This improves pelletizer efficiency and reduces energy costs.
6.2 How to Extend Blade Life?
- Use high-quality customized industrial blades.
- Implement regular sharpening and preventive maintenance schedules.
6.3 How to Reduce Energy Costs for Pelletizing?
- Use infrared heating instead of traditional resistive heating.
- Optimize extruder temperature control for energy efficiency.
6.4 What’s the Best Equipment for My Business?
- If you process large rigid plastics, choose a crusher.
- If you need high-value recycled material, invest in a pelletizer.
Both plastic crushers and pelletizers play a crucial role in plastic recycling. Choosing the right equipment depends on your specific processing needs:
- If your goal is waste volume reduction and easier material handling, a plastic crusher is the right choice.
- If you need reusable plastic pellets for manufacturing, a pelletizer is the better investment.
However, the efficiency, durability, and performance of these machines rely heavily on high-quality industrial blades and knives. Investing in customized industrial blades not only ensures better cutting efficiency and longer service life but also reduces operational costs and downtime.
Looking for High-Performance Crusher or Pelletizer Blades? Contate-nos!
At Nanjing Metal, we specialize in customized industrial blades designed for plastic crushers and pelletizers.
Referências
· Plastics Recycling Update (2024). Global Trends in Plastic Waste Management.
· Market Research Report (2023). Energy Efficiency in Plastic Processing Equipment.
· European Plastics News (2022). Best Practices for Pelletizing Recycled Plastics.