The tire manufacturing industry is highly competitive, with demands for both precision and durability. The key to maintaining high productivity and minimizing costs lies in using the right tools, especially the blades and knives used throughout the production process. High-performance industrial blades for tire manufacturing are crucial for optimizing production efficiency and reducing operational costs.
В Нанкин Metal, we understand the importance of using high-quality blades that can withstand the rigorous demands of tire production. With a strong history of innovation and craftsmanship, Nanjing Metal provides cutting-edge solutions for tire manufacturers.
In this guide, we’ll explore how to choose the right blades for tire manufacturing, focusing on blade materials, applications, and their maintenance.
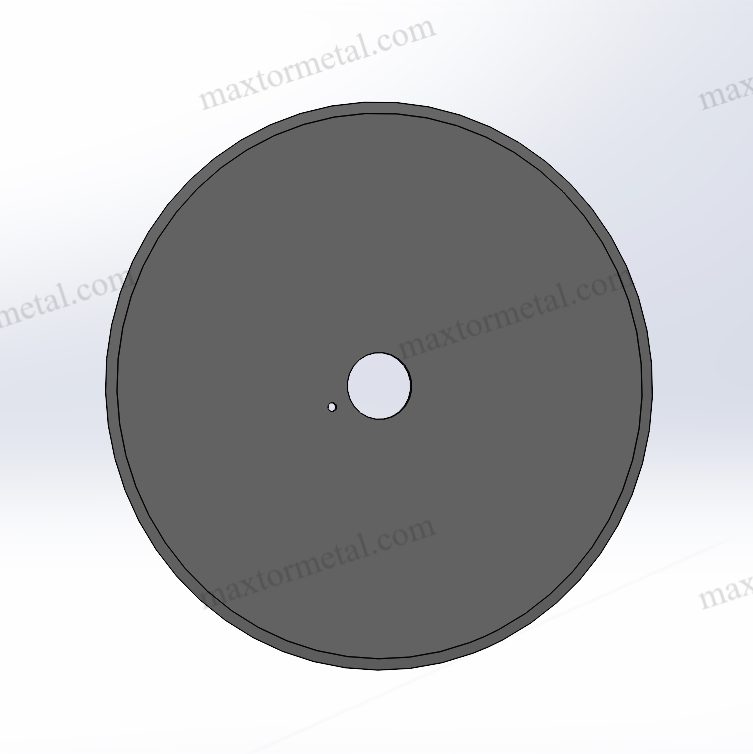
1. Tire Industry Blade Selection Guide
Selecting the right blades for tire manufacturing requires understanding several key factors:
- Тип материала
- Прочность
- Application-Specific Needs
1.1 Material Selection: Carbon Steel, Stainless Steel, and Alloy Steel
Different materials offer different advantages depending on the task at hand. Below is a comparison of common blade materials used in tire manufacturing:
Тип лезвия | Преимущества | Ограничения | Типичные применения |
Углеродистая сталь | Sharp edge retention, cost-effective, high hardness | Prone to rust, lower corrosion resistance | Rubber mixing, cutting soft rubber |
Нержавеющая сталь | Corrosion-resistant, precision cuts, durable | More expensive than carbon steel | Trimming, finishing, hygienic applications |
Легированная сталь | High wear resistance, long lifespan, can handle high stress | Expensive, needs specialized handling | Slitting, heavy-duty cutting, reinforced rubber |
Карбид вольфрама | Extremely durable, excellent for precision, maintains sharpness longer | High initial cost, more brittle than other steels | Precision cutting, tire finishing |
Key Takeaway: If you’re cutting through soft rubber, carbon steel may be more cost-effective, but for durability and long-term performance, alloy steel and stainless steel are often superior. Understanding your production demands will help guide the material choice.
1.2 Blade Applications: Cutting, Trimming, Slitting, and More
Tire production involves several steps that require different types of blades. Let’s break down each application:
- Cutting Blades: These blades are designed to handle the primary task of slicing through large sheets of rubber. Typically, carbon steel or alloy steel blades are used for this purpose.
- Trimming Blades: After the tire shape is formed, excess rubber needs to be trimmed off. Stainless steel blades are often preferred for their corrosion resistance and clean cutting properties.
- Лезвия для резки: These are used for cutting tires to their final width. Alloy steel blades are the best choice here due to their durability and ability to withstand high-stress cuts.
The selection of blade type for each application ensures high-quality results and maximizes productivity.
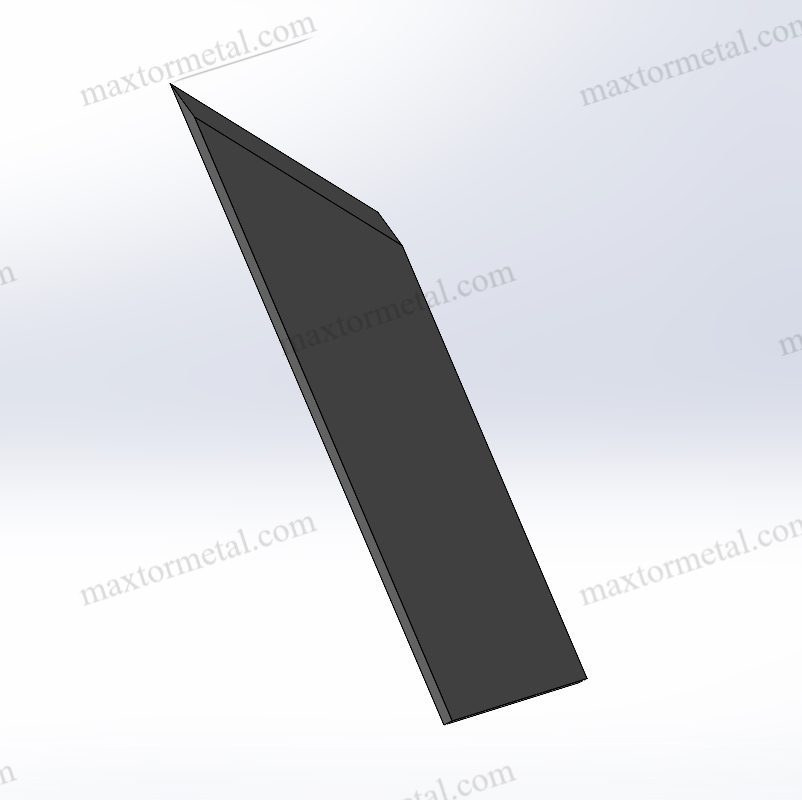
2. Industrial Blades in Tire Manufacturing
Industrial blades play an essential role in ensuring precision, efficiency, and the reduction of material waste throughout the tire manufacturing process. From rubber mixing to finishing, blades ensure that every step of tire production meets strict quality and durability standards. Here’s an expanded and more detailed look at how different blades function across the tire manufacturing stages.
2.1 Rubber Mixing: Cutting Blades
Приложение: In this stage, rubber mixing involves combining raw materials like rubber, carbon black, oils, and other additives. Cutting blades are used to slice and chop raw rubber into manageable sizes before mixing, which is a crucial step for consistent material properties and optimal mixing efficiency.
- Тип лезвия: Carbon Steel Blades (often preferred)
- Key Characteristics: Carbon steel blades are sharp and maintain their edge, ensuring that they can quickly and efficiently cut through tough rubber compounds. They are used because of their cost-effectiveness, particularly when cutting soft to moderately hard rubber mixtures.
- Blade Performance: Cutting efficiency also depends on factors like blade geometry and the type of rubber being processed. For example, blades with specific edge profiles are better suited to slicing through different thicknesses of rubber sheets, which can reduce wear and tear on blades during operation.
2.2 Tire Molding: Trimming Blades
Приложение: After the tire has been molded, excess rubber needs to be trimmed from the tire. Trimming blades are used to remove any flash (excess rubber) and ensure the tire is shaped to exact specifications.
- Тип лезвия: Stainless Steel Blades (most commonly used)
- Key Characteristics: Stainless steel blades are highly resistant to corrosion, making them ideal for high-precision tasks like trimming molded tires. These blades can perform at high speeds without losing sharpness, offering clean cuts and precise edge formation.
- Показатели производительности: Trimming blades made from stainless steel also help reduce post-molding defects such as uneven tire thickness. By improving the trimming precision, these blades directly contribute to reduced material waste and better-quality tires.
2.3 Tire Slitting: Лезвия для резки
Приложение: Slitting blades are crucial in dividing large tire rolls into the final width and shape. This step is necessary for creating tires with precise dimensions and characteristics that align with specific performance requirements.
- Тип лезвия: Alloy Steel Blades (preferred for slitting tasks)
- Key Characteristics: Alloy steel blades offer superior durability and resistance to heat. Their toughness ensures that they can handle the high pressure and force required to slit reinforced rubber and steel-belted tire materials without suffering from excessive wear.
- Key Considerations: The effectiveness of slitting blades also depends on the geometry of the blade, such as the angle of the edge and the blade’s thickness. Optimizing these factors can further enhance slitting precision and cutting speed.
2.4 Tire Finishing: Precision Cutting Blades
Приложение: The finishing stage involves the refinement of tire edges, particularly along the sidewalls, to ensure a uniform, smooth appearance. Precision cutting blades are used to trim these edges and remove any excess rubber without damaging the tire structure.
- Тип лезвия: Tungsten Carbide Blades (or coated steel blades)
- Key Characteristics: Tungsten carbide blades are extremely hard and wear-resistant, making them ideal for precise cutting in the finishing stage. These blades maintain their sharpness for long periods, even in the face of frequent use during high-speed production processes.
- Показатели производительности: Tungsten carbide blades also improve edge quality by ensuring that no irregularities or unwanted burrs are left on the tire. Tires with smooth, uniform sidewalls have improved aesthetic appeal and better performance in terms of aerodynamics and balance.
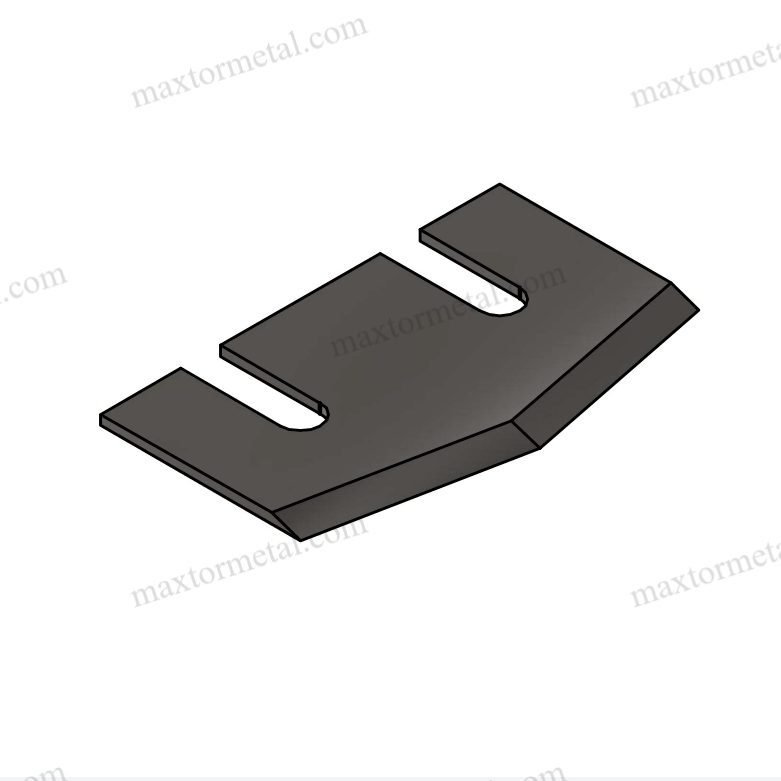
3. High-Performance Industrial Blades: Advantages
3.1 Повышение эффективности производства
High-performance blades are engineered to improve the cutting speed and precision, which directly translates into enhanced production efficiency. The efficiency gain is not only from faster cutting speeds but also from reduced downtime due to blade replacements. A study published in The International Journal of Industrial Engineering (2021) concluded that tire manufacturers using high-performance blades saw a 20% increase in production rates due to reduced downtime and fewer blade changes.
3.2 Longer Blade Life
High-quality industrial blades can endure extended use without losing sharpness or integrity. For example, alloy steel blades used for heavy-duty cutting tasks in tire manufacturing can last up to 2.5 times longer than their carbon steel counterparts. The International Rubber Study Group found that upgrading to a premium alloy steel blade can reduce blade replacement costs by 40% over the course of a year.
3.3 Reduced Downtime
Blades that are built to last and require fewer replacements reduce unplanned downtime. High-performance blades tend to retain sharpness longer and provide consistent cutting results, reducing the need for frequent adjustments.
- Данные по отрасли: According to a report from the National Rubber Manufacturers Association (2022), tire manufacturers using durable, high-performance blades experienced 40% less unplanned downtime than those using standard blades. The improved reliability of high-performance blades significantly enhanced production line efficiency.
3.4 Cost Reduction
While high-performance blades may come with a higher upfront cost, their extended lifespan, improved cutting efficiency, and lower maintenance requirements lead to long-term savings. Manufacturers who invest in high-quality blades often see a reduction in total cost per unit produced.
- Economic Data: The Manufacturing Cost Analysis Study (2022) found that manufacturers using high-performance blades could save up to 18% annually in operational costs, thanks to increased productivity and reduced need for blade replacements.
Investing in high-quality blades not only helps tire manufacturers maintain consistent output but also leads to significant savings over time. Blades that maintain sharpness, withstand high-stress cutting, and require minimal maintenance are crucial to achieving sustained cost efficiency in the tire production industry.
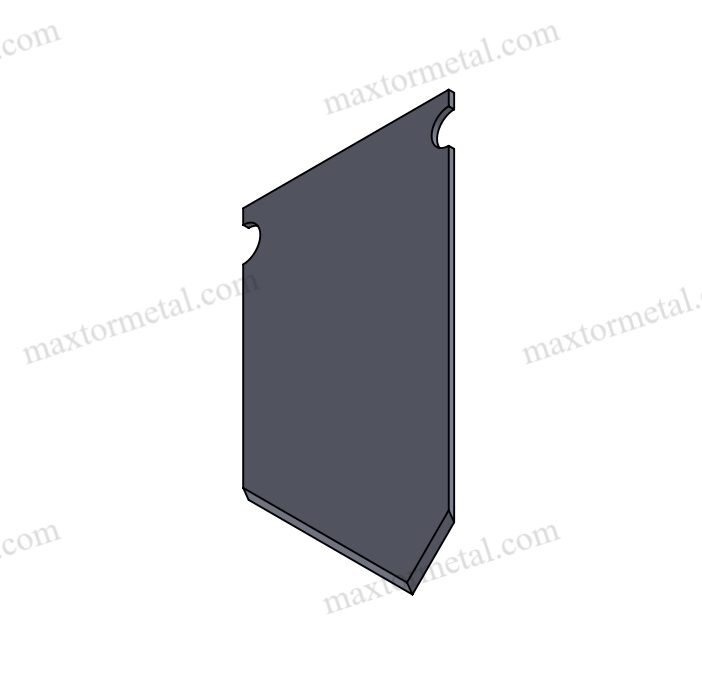
4. Custom Blade Solutions for Tire Manufacturing
Not all tire manufacturing operations are the same. Depending on your production environment, you may require customized blades that fit your specific needs. Nanjing Metal offers tailored blade solutions to ensure that your blades are optimized for your exact requirements.
Custom blade manufacturing involves working closely with the customer to design blades that fit the production line, material type, and production volumes. Our expert team guides you through every step of the process, from design to manufacturing, ensuring your blades are perfectly suited to your needs.
5. Blade Maintenance and Care
Maintaining industrial blades properly is crucial to ensuring their longevity, efficiency, and performance. Proper care not only extends the life of the blades but also minimizes production downtime and enhances the overall cost-effectiveness of the manufacturing process. Below are detailed, data-supported practices to optimize blade maintenance in tire manufacturing:
5.1 Regular Sharpening
Sharpening blades at the right intervals ensures they remain efficient and effective. Over time, blades wear down due to friction and impact with tough materials. Dull blades result in higher energy consumption and less efficient cutting, ultimately affecting the overall production cycle.
- Частота заточки: The frequency of sharpening depends on the blade material and the type of cutting it performs. For example, carbon steel blades used in rubber cutting might require sharpening every 50–100 hours of operation, while лезвия из карбида вольфрама, which are harder and more durable, may last for several hundred hours before needing sharpening.
- Sharpening Methods: Precision sharpening machines should be used to ensure the blade’s edge geometry remains intact. Incorrect sharpening can result in uneven edges, which can cause improper cuts, leading to quality defects in the tire manufacturing process.
5.2 Proper Storage
Storage conditions play a vital role in maintaining blade quality. Storing blades improperly, especially in environments with fluctuating humidity or extreme temperatures, can lead to rust and corrosion, particularly in carbon steel blades. To avoid these issues, proper storage practices must be followed.
- Environmental Conditions: Store blades in a clean, dry environment with stable temperatures between 15-25°C (59-77°F). Humidity should be kept below 50% to prevent oxidation and rust. If blades are stored in high-humidity areas, they should be regularly inspected and coated with protective oils or anti-rust coatings.
- Storage Systems: Implementing blade storage systems such as custom tool racks or cases with anti-corrosive liners helps maintain the integrity of the blade edges and minimizes the risk of physical damage during storage and handling.
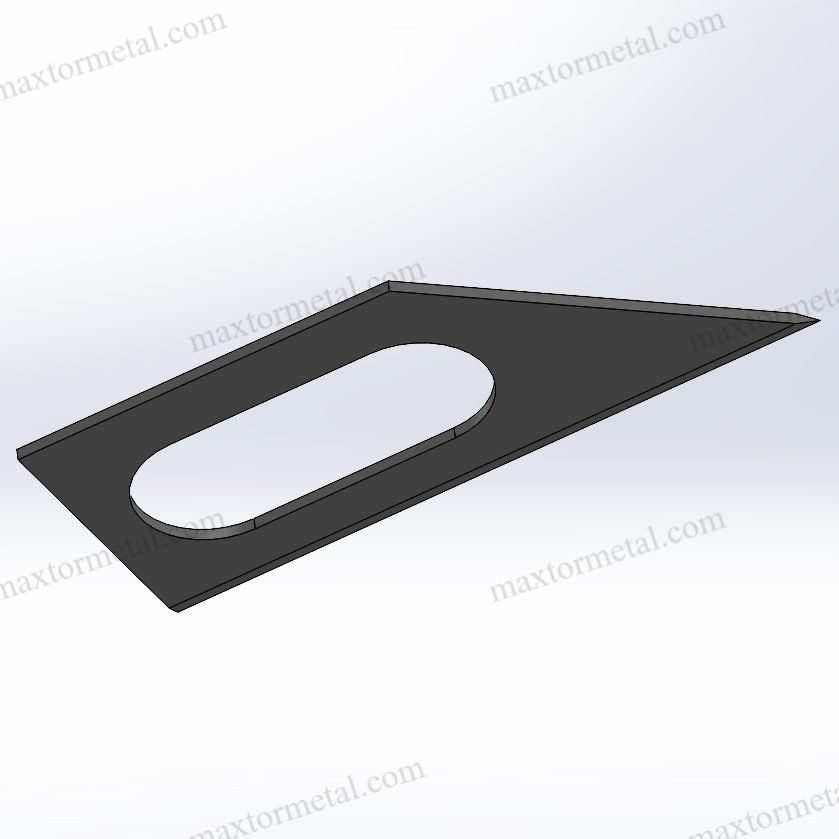
5.3 Routine Inspections
Regular inspections are key to identifying early signs of wear, damage, or other issues that can compromise blade performance. Timely detection of problems such as dull edges, chips, cracks, or bending can prevent sudden failures during production and improve safety.
- Частота проверок: Blades should be inspected at least once per shift, particularly in high-volume production environments. For blades used in critical processes, inspections may be required before each operation. Digital inspection tools or cameras can help detect minor flaws and cracks in the blade’s surface that might not be visible to the naked eye.
- Key Indicators of Blade Wear:
- Тупые края: Leads to inefficient cutting, higher energy consumption, and inconsistent product quality.
- Chips and Cracks: Typically occur due to impact or stress. If not addressed, they can lead to blade failure.
- Bending or Warping: Common in blades exposed to high temperatures or improper handling.
5.4 Addressing Common Blade Failures
Blades can fail due to several factors, including improper maintenance, poor-quality materials, or excessive wear. Recognizing these issues early and taking corrective action can prevent costly downtime and suboptimal production.
- Тупые края: Dull blades increase cutting resistance, which results in more heat and premature wear. Regular sharpening should be performed before edges become too dull to work effectively. Blades made from легированная сталь или карбид вольфрама typically hold their edge longer but will require sharpening as they wear down.
- Трещины: Cracks are often caused by mechanical stress or improper heat treatment. Once cracks appear, it’s essential to replace the blade immediately, as a cracked blade could shatter during operation, leading to damage or injury.
- Bending or Warping: Warped blades result from uneven heating during manufacturing or excessive operational stress. Bending can affect the blade’s ability to maintain its cutting precision and cause uneven cuts. Regular inspections for these issues can prevent this problem.
6. Blade Innovation in the Tire Manufacturing Industry
As the tire manufacturing industry continues to evolve, so does the technology behind the blades used in production. These innovations enhance blade performance, improve tire production efficiency, and reduce overall costs. Here are some of the latest trends and technological advancements in blade design:
6.1 Advanced Coatings for Extended Life
The use of advanced coatings нравиться алмаз, керамика, и titanium nitride (TiN) has dramatically improved the durability of industrial blades.
- Diamond Coatings: Diamond coatings are applied to blades to improve their hardness and wear resistance. These coatings reduce friction during cutting, which results in sharper edges and extended blade life. Diamond-coated blades are ideal for cutting highly abrasive materials, such as rubber compounds with embedded steel wires.
- Ceramic Coatings: Ceramic-coated blades offer high resistance to heat and corrosion. These coatings allow blades to maintain sharpness even under intense conditions, improving efficiency and reducing the need for frequent maintenance. Tire Industry Research (2021) has found that ceramic-coated blades in high-stress environments outperform traditional steel blades by 35% in terms of longevity and cutting precision.
- Нитрид титана (TiN): TiN coatings offer enhanced resistance to wear and corrosion while also reducing friction. This results in smoother cuts and better overall blade performance, which is essential for high-volume tire manufacturing operations. TiN coatings are particularly beneficial for blades used in high-speed slitting and cutting tasks.
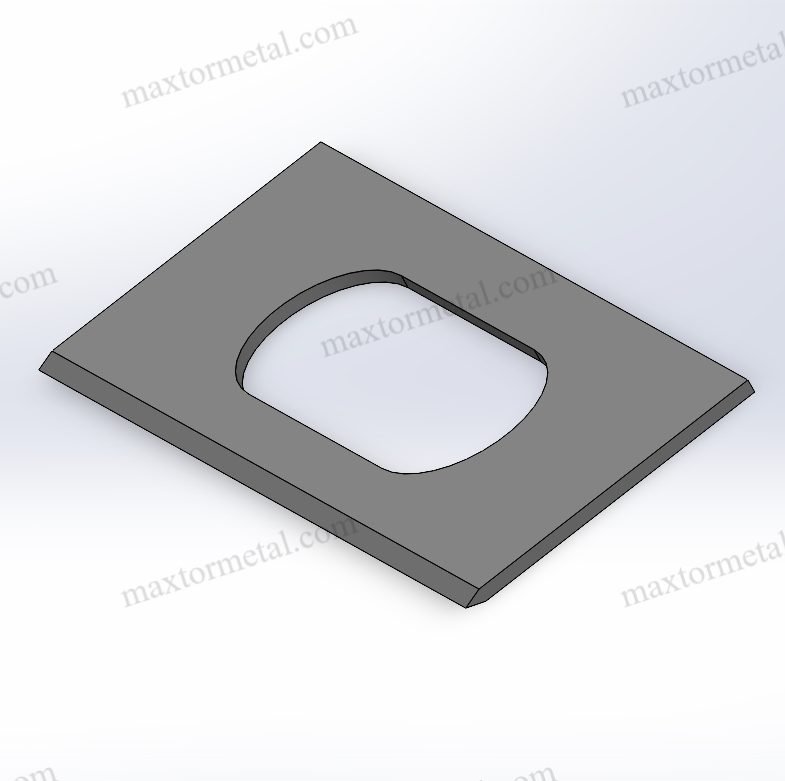
6.2 Heat Treatment for Blade Durability
Innovations in heat treatment techniques have enabled blades to maintain their sharpness and strength longer, even under intense operational conditions.
- New Heat Treatment Techniques: Advances in heat treatment processes such as vacuum heat treatment и induction hardening allow for more precise control over the hardness and toughness of blades. These treatments ensure that blades can withstand the extreme stresses they face during tire production, such as cutting through reinforced materials and high-tensile rubbers.
6.3 Custom Blade Geometry
Blade geometry—such as edge angles, thickness, and surface finish—can significantly affect the cutting efficiency and quality of the process.
- Edge Angle and Blade Geometry: Manufacturers are now designing blades with customized geometries tailored to specific production needs. For example, blades with sharper or more acute angles are ideal for fine cuts in tire finishing, while thicker edges are used for more robust cutting tasks in slitting or molding.
- Specialized Edge Coatings: Some blades feature specialized coatings to reduce wear and improve cutting precision at higher speeds. This includes cobalt-alloy coatings that can maintain cutting efficiency at elevated temperatures commonly found in the tire production process.
- Innovative Designs: Companies like Нанкин Metal are investing in the development of proprietary geometries that optimize cutting angles and reduce friction. According to a report by Tire Technology International (2022), custom-designed blades have led to a 10–15% increase in overall cutting efficiency, reducing operational costs and improving product quality.
These technological innovations in blade materials, coatings, heat treatment, and geometry have significantly improved the longevity and performance of blades used in tire manufacturing. Manufacturers that stay up-to-date with these advancements can benefit from reduced downtime, improved cutting precision, and lower maintenance costs.
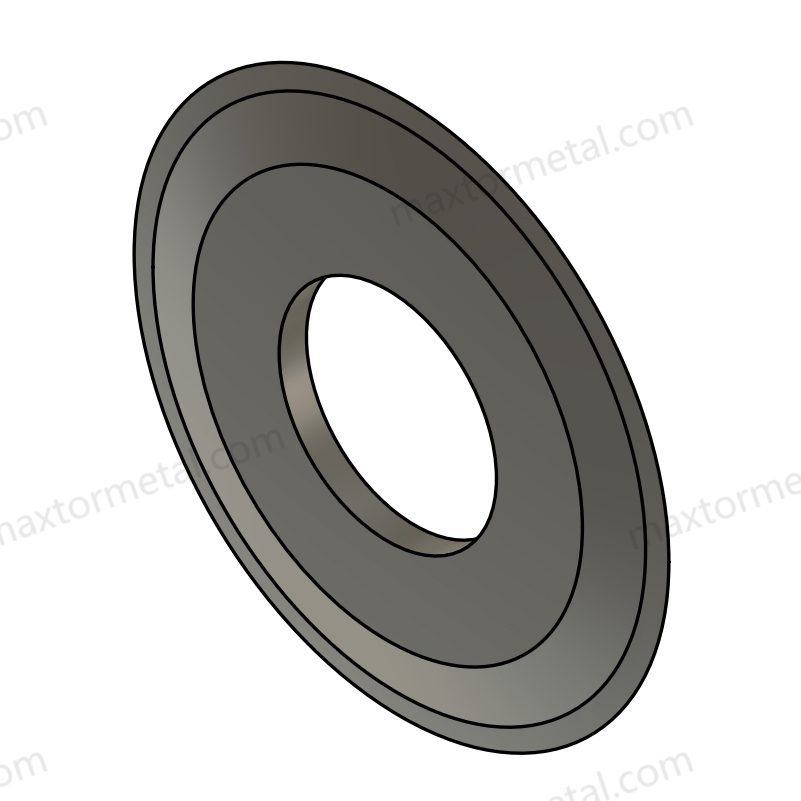
7. Comparing Different Blade Types for Tire Manufacturing
Selecting the right blade type for specific tasks is crucial in optimizing the tire manufacturing process. Each blade type is designed with unique features that make them suitable for specific tasks. Below is a more detailed comparison of the most commonly used blades in tire production, with added insights into material properties and performance metrics.
Тип лезвия | Функция | Материал | Recommended Use | Detailed Insights |
Круглые лезвия | Continuous cutting of rubber sheets | Carbon steel, alloy steel, tungsten carbide | Ideal for bulk cutting | Circular blades are often chosen for their uniform cutting capability and precision in slicing large volumes of rubber sheets or tire components. The use of карбид вольфрама in these blades, known for its hardness and wear resistance, allows for extended lifespan, especially when cutting high-abrasion materials. |
Trimming Blades | Removing excess rubber after molding | Stainless steel, cobalt alloy | Clean cuts in tire shaping and trimming | Trimming blades must have a sharp edge and corrosion resistance, as they are exposed to high temperatures and humidity. Stainless steel blades are ideal for this purpose because they resist corrosion while maintaining a sharp edge. Cobalt-alloy trimming blades are more resilient to wear and tear when exposed to high temperatures during the final tire shaping process. |
Лезвия для резки | Cutting tires into widths and precise shapes | Alloy steel, high-speed steel | Slitting rubber to size | Slitting blades are designed for accuracy and precision when dividing tire sections into specified widths. Быстрорежущая сталь (HSS) is preferred here due to its excellent heat resistance and ability to maintain sharpness under stress. Легированная сталь, often used for slitting blades, provides a balance of toughness and cost-effectiveness. The cutting speed and resistance to heat buildup make alloy steel particularly suited for high-speed slitting applications. |
The choice of material significantly impacts the blade’s performance, wear resistance, and cutting quality. Tungsten carbide is ideal for high-abrasion tasks, while stainless steel excels in precision cutting and trimming. Alloy steel and high-speed steel offer a balanced combination of durability and performance for slitting operations.
8. Optimizing Cutting Efficiency
To maximize efficiency and minimize production costs, it is essential to understand the relationship between blade geometry и cutting performance. The design of the blade’s edge, angle, and surface properties can influence cutting speed, precision, and the quality of the final product. Let’s explore some key factors that play a critical role in blade efficiency:
8.1 Key Factors in Blade Geometry:
8.1 Blade Angle
The angle at which the blade meets the material during cutting—known as the угол резания—plays a crucial role in reducing cutting resistance. A sharper cutting angle (smaller blade angle) can reduce friction and make cutting easier, leading to faster production times. However, there is a tradeoff: sharper angles can cause blades to wear faster, as the cutting edge becomes more vulnerable to impact and heat buildup.
- Optimal Blade Angles for Tire Manufacturing:
- Круглые лезвия: Typically use an angle between 20° and 30°, which allows for a balance between cutting speed and blade durability. This ensures smooth, continuous cuts of rubber sheets without excessive wear.
- Trimming blades: A sharper angle of around 15° to 20° is often used for cleaner cuts, especially during the final tire shaping process where precision is paramount.
- Slitting blades: Usually have a slightly larger cutting angle (30° to 45°) to withstand the increased stress from cutting through thicker, tougher rubber materials.
8.2 Edge Design
The design of the blade edge—whether smooth, serrated, or honed—can significantly impact cutting precision, friction levels, and heat generation. A smooth edge tends to reduce friction, leading to lower heat generation and longer blade life. On the other hand, a serrated edge is better suited for cutting through more fibrous or abrasive materials.
- Smooth Edges: Provide clean, precise cuts with minimal wear. This is particularly important for trimming blades that require sharpness and accuracy throughout the production process.
- Serrated Edges: Often used in applications where the material being cut is tougher, like steel-belted rubber. Serrated edges provide better grip and cutting efficiency, especially for лезвия для резки used for tougher tire segments.
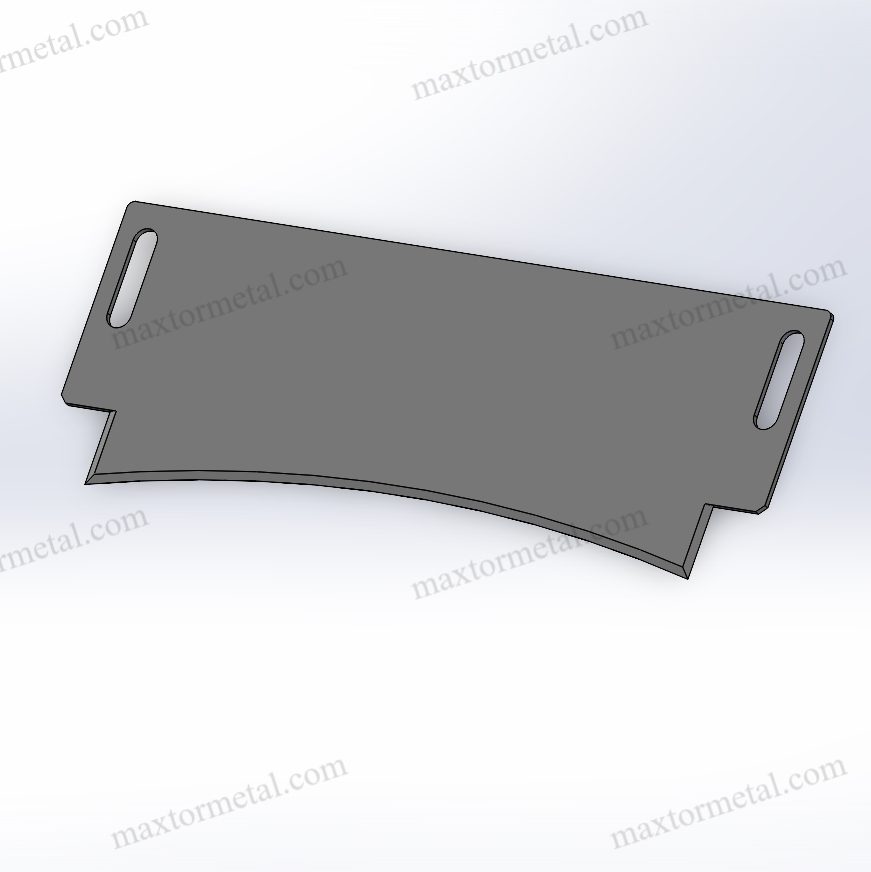
8.3 Surface Finish
The finish of the blade surface, including whether it is polished, coated, or treated, impacts its performance. Blades with a polished или coated surface experience less friction, leading to reduced wear and smoother cuts.
- Coated Blades: Many tire manufacturing blades are coated with Тин (Titanium Nitride) or Алмазоподобный углерод (DLC) coatings, which reduce friction and improve wear resistance. These coatings enhance cutting efficiency, especially in high-temperature operations, and reduce the frequency of sharpening.
8.2 Relationship Between Geometry and Cutting Efficiency
Blade geometry not only affects the cutting speed but also determines how cleanly the material is cut and how minimally the blade wears. By optimizing the blade geometry, tire manufacturers can achieve a substantial boost in efficiency while reducing operational costs:
- Энергоэффективность: A blade with optimized geometry (correct angle and edge design) requires less force to cut through rubber, thus reducing energy consumption.
- Precision and Waste: Precision cutting ensures the production of high-quality tires with minimal material waste. Cleaner cuts lead to better tire performance and aesthetics, which is critical in the competitive tire industry.
- Operational Cost Savings: Minimizing wear, reducing friction, and prolonging blade life result in fewer replacements and less downtime for blade maintenance. This translates into cost savings and increased production uptime.
9. The Critical Role of Blades in Tire Manufacturing
Blades play an integral role in ensuring tire production is efficient, precise, and cost-effective. By understanding the different blade materials, types, and applications, you can optimize your production line for maximum output and minimal downtime.
At Nanjing Metal, we specialize in providing high-quality, durable blades that meet the demanding needs of tire manufacturers. Whether you require standard blades or custom-made solutions, we have the expertise to support your business’s growth and success.
To learn more about how Nanjing Metal’s blades can improve your tire manufacturing process, contact us today.