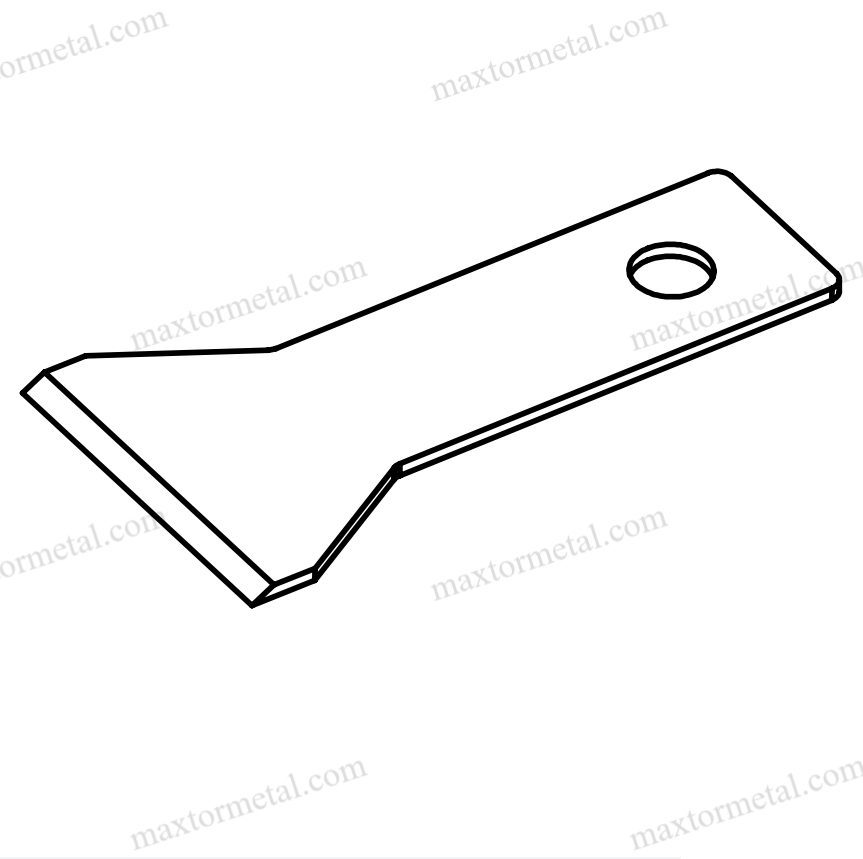
Selecting the best coltelli per pelletizzazione is crucial for efficient plastic processing. You need to consider the right knife type, high-quality materials, and precise design. In 2025, pelletizing knives play a vital role in the pelletizing process by producing better pellets, reducing costs, and supporting environmental sustainability. Research shows that using pelletizing knives to achieve uniform particle sizes improves production efficiency and maintains consistent pellet quality. This consistency is essential for the plastic recycling industry and its various recycling stages. The global market for pelletizing is rapidly expanding. Choosing pelletizing knives from trusted manufacturers ensures optimal results.
Punti chiave
- Picking the right pelletizing knife makes pellets better, uses less energy, and helps machines work faster.
- There are different pelletizer blade types for each plastic and job. You need to match the blade’s material and shape to your machine.
- Clean, sharpen, and change blades often to keep pelletizers working well and stop delays.
- Custom pelletizing knives fit better, last longer, and make better pellets. They also help you save money over time.
- Always read your pelletizer’s manual and check the plastic type before picking blades. This helps you avoid mistakes.
Pelletizing Knives Overview
What Are Pelletizing Knives
Pelletizing knives are special cutting tools used in the plastic industry. These blades cut plastic strands, molten polymers, or extruded materials into even pellets. The knives have different shapes like straight, slanted, or V-shaped. Each shape fits a certain pelletizer machine or job. Most pelletizer blades are made from high-carbon steel, tool steel, or strong alloys. These materials make the blades hard and tough. Heat treatment and coatings like titanium nitride or chromium help the blades last longer and slide better.
Some important technical details show how well pelletizer knives work:
- CNC machining makes edges very exact, as close as ±0.002 mm. This helps the blade shake less and last longer.
- Laser cutting gives the blade a very sharp edge. This makes cuts smoother and helps the blade last up to 30% longer.
- Smart coatings like Diamond-Like Carbon can make the blade slide 40% easier.
- Cryogenic treatment makes steel blades last 25% longer.
- AI sensors can tell when to replace blades with 95% accuracy.
Specification | Value / Range |
---|---|
Cutting Capacity | 1-8 mm pellets |
Output | 500-2,000 kg/h |
Materiale della lama | SKD-11 Steel + Tungsten Carbide |
Finitura superficiale | Mirror Polishing (Ra ≤0.1μm) |
Durezza | HRC 58-62 Core, 1,500 HV Edge |
Blade Runout Tolerance | ±0,005 millimetri |
Resistenza alla temperatura | 300°C Continuous Operation |
Warranty | 15,000 Operating Hours |
Role in the Pelletizing Process
Pelletizer knives are very important in the pelletizing process. They cut plastic into good pellets. These pellets are needed to make recycled products. The sharp and well-placed knives help keep pellet quality the same. This helps other machines and recycling steps work better. The pelletizing process needs sharp, lined-up, and strong knives to work well.
Manufacturers see many good things when they use better pelletizer blades:
- Energy use can go down by up to 15%.
- Production can go up by 20%.
- Automation and smart maintenance mean less downtime and lower costs.
- Better knives make fewer small bits and stop plastic from breaking down. This means more material is used and products are more even.
Pelletizer blades must be as hard and tough as the plastic they cut. The right blade shape and sharpness make clean cuts and good pellets. These things help companies make pellets that are always the same and save money. They also help make pellets for many uses.
Types of Pelletizer Blades
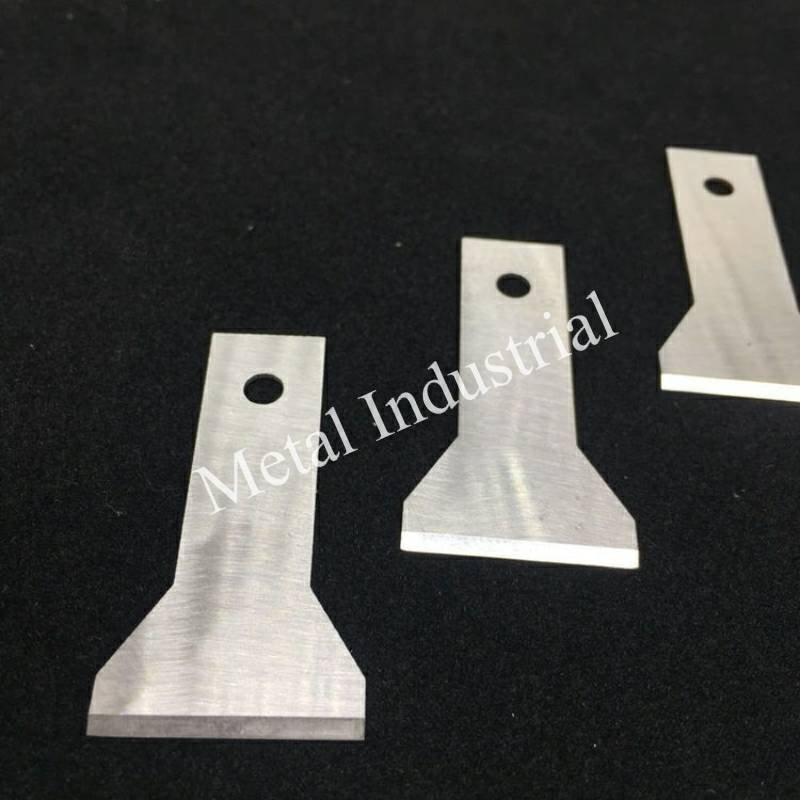
Pellettizzatore a filamenti
Suitable Plastic Types
Strand pelletizing systems can work with many thermoplastics. These include polypropylene, polyethylene, ABS, and polystyrene. Operators also use them for thermosets and elastomers. The system works with both new and recycled materials.
Main Advantages and Disadvantages
- The system cuts plastic into pellets that are all the same size.
- It can run for a long time and make lots of pellets.
- You can use it with many kinds of plastics.
- You can change the blade to make different pellet shapes.
- It fits into most extrusion lines without big changes.
Note: Some materials need extra drying after using strand pelletizing systems.
Scenari applicativi tipici
Strand pelletizing systems are good for small or medium jobs. Many recycling lines use them when pellet size is not the most important thing. Manufacturers use them for compounding, making masterbatch, and lab research. The system is popular because it works with many materials.
Water-Ring Pelletizer
Suitable Plastic Types
Water-ring pelletizing systems work with polyolefins like PE and PP. They also handle TPE, EVA, and some mixed plastics. These systems are good for polymers that melt well.
Main Advantages and Disadvantages
Aspetto | Water-Ring Pelletizers (WRPs) | Underwater Pelletizers (UWPs) |
---|---|---|
Metodo di taglio | Rotating knives cut at the die face | Knives cut in water |
Pellet Shape | Pellets are round and flat | Pellets are more round |
Cooling Method | Water ring cools and moves pellets | Pellets cool in a water bath |
Cooling Water Management | Water is cleaned and used again | Water is also cleaned and reused |
Throughput Capacity | About 11,000 pounds per hour | Up to 70,000 pounds per hour |
Polymer Compatibility | Works best with strong-melting polymers | Can handle more types of polymers |
Sensitivity to Process Variations | Not very sensitive to changes in melt or pressure | More sensitive, can freeze at the die |
Automation and Cost | Medium automation, lower cost, small size | More automation, higher cost, takes more space |
Water-ring pelletizing systems run all the time and cool pellets well. They make pellets that look good and have a nice surface. The system is small and does not cost too much. But it does not work well with sticky or thick materials. You also need to watch the water closely.
Scenari applicativi tipici
Manufacturers use water-ring pelletizing systems for masterbatch and compounding. The system is good when you need nice-looking pellets and fast cooling. It is used in medium and large factories where pellet size matters.
Pelletizzatore subacqueo
Suitable Plastic Types
Underwater pelletizing systems work with engineering plastics like polyamide, PBT, and PET. They also handle sticky, soft, or heat-sensitive polymers. The system can process special resins that are hard for other systems.
Main Advantages and Disadvantages
- Underwater pelletizing systems make pellets that are all the same size.
- Cutting and cooling happen at the same time, so pellets cool fast.
- These systems make less dust, so pellets stay clean.
- You can use them with many plastics, even sticky ones.
- They can make lots of pellets with little size difference.
- Underwater pelletizing systems use less power and space than strand systems.
- Pellet classifiers and water baths help keep pellets the right size.
Research shows pellet shape can change after cooling. The way pellets form is important for getting good results.
Scenari applicativi tipici
Underwater pelletizing systems are best for big factories. Manufacturers use them for engineering plastics and special polymers. They are great for jobs that need lots of pellets that are all the same. The system is good for tough materials and special resin jobs.
Pellettizzatore Die-Face
Suitable Plastic Types
Die-face pelletizing systems work with PVC, TPR, TPU, and other sticky or heat-sensitive plastics. The system is good for polymers that need to be cut right at the die.
Main Advantages and Disadvantages
Fattore | Die-Face Pelletizers (Plastic Pelletizer) | Alternative (Plastic Crusher) |
---|---|---|
Consumo energetico | Uses more energy per ton | Uses less energy per ton |
Requisiti di manutenzione | Needs cleaning and knife changes often | Needs blade sharpening often |
Initial Investment Cost | Costs more to buy | Costs less to buy |
Operational Cost | Costs more to run each year | Costs less to run each year |
Velocità di elaborazione | Slower because of melting and cutting | Faster, just cuts plastic right away |
ROI Period | Takes longer to earn back money | Earns back money faster |
Output Quality | Makes high-quality pellets | Makes crushed plastic, not as valuable |
Aspetto | Die-Face Pelletizers (Hot Die-Face System) | Cooling Pelletizers (Cold Pelletizing System) |
---|---|---|
Pelletizing Rate | Makes up to 22,679.62 kg/h (underwater), 13,607.77 kg/h (water spray), 4,989.52 kg/h (airflow) | Makes up to 6,803.89 kg/h (sliver), 1,814.37 kg/h (stretching) |
Cutting State | Cuts melted polymer right away | Cuts cooled, solid polymer |
Cutter Replacement Frequency | Needs new cutters less often | Needs new cutters more often |
Noise Emission | Quieter, water blocks sound | Louder |
Consumo energetico | Uses more energy, needs heating | Uses less energy, no heating needed |
Maintenance Complexity | Harder to maintain, needs careful setup | Easier to use and clean |
Operational Complexity | Needs careful control to stop freezing | Easier to run, but can have pellet size problems |
Cooling Method | Uses water or air to cool pellets | Uses air or water, then dries pellets |
Drawbacks | Can freeze at the die, costs more, harder to fix | Takes up more space, can make powder or scrap |
Vantaggi | Makes more pellets, better quality, less cutter wear, quieter | Costs less, easy to use, easy to clean, good for color mixing |
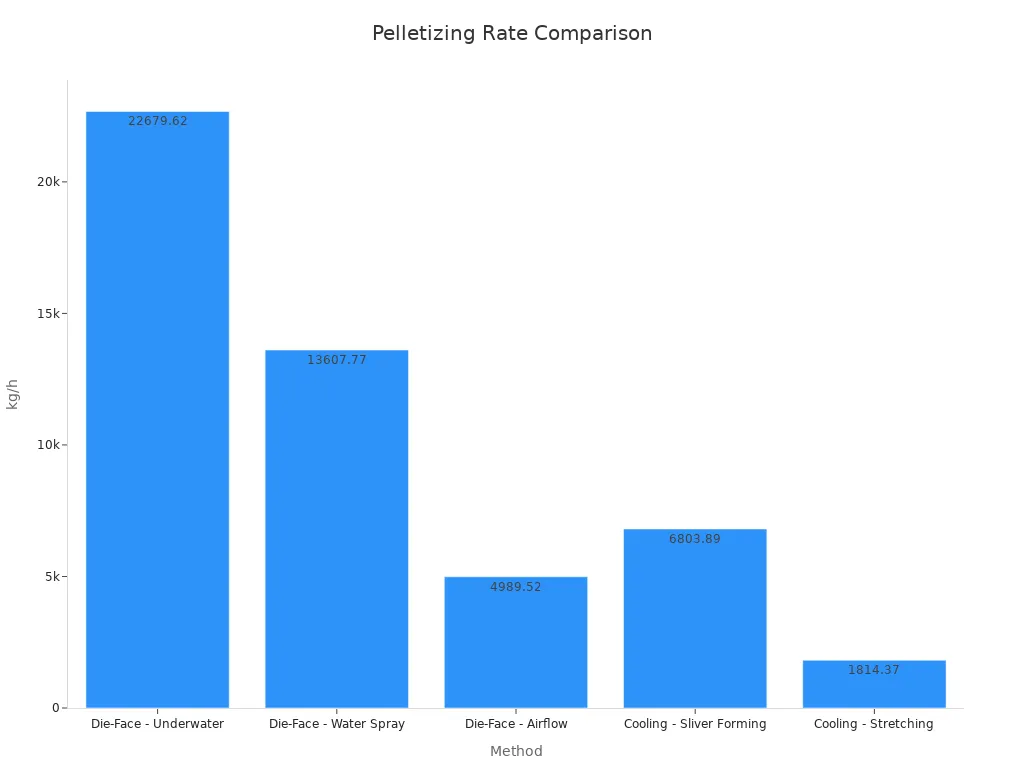
Die-face pelletizing systems make pellets that look very good. The system cuts melted polymer at the die, so cutters last longer and make less noise. You get more pellets and better quality. But you must watch the temperature and do regular maintenance to stop freezing and keep pellets the same.
Scenari applicativi tipici
Die-face pelletizing systems are used for soft PVC, TPR, TPU, and special compounds. Manufacturers pick this system for sticky or heat-sensitive plastics. It is good for making high-quality pellets for special and valuable products.
Key Factors in Choosing Pelletizing Knives
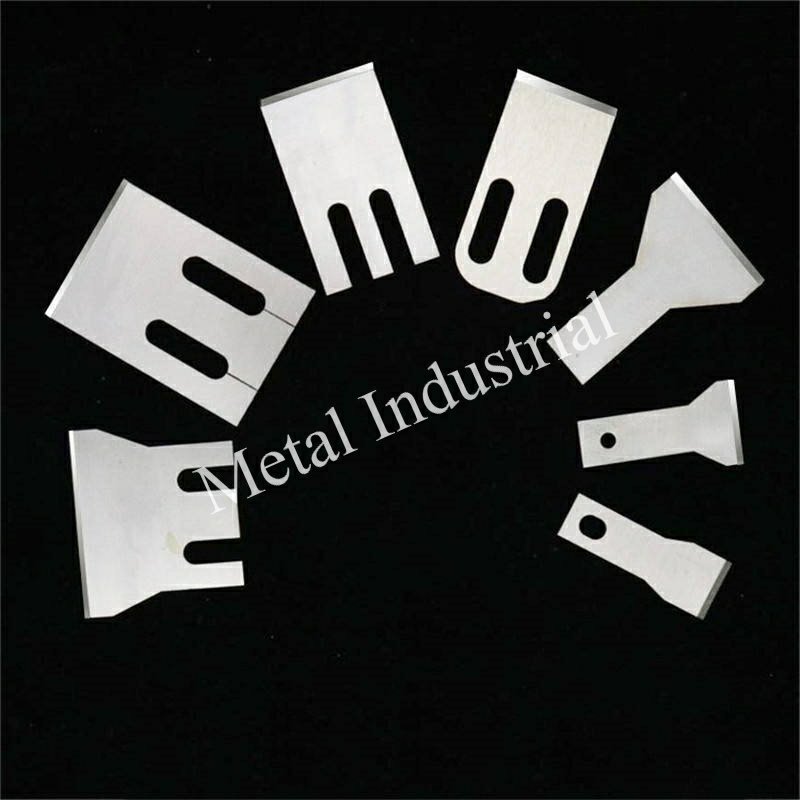
Compatibilità dei materiali
Material compatibility is very important when picking pelletizer knives. Each pelletizing system works with different plastics. These can be polyolefins or engineering resins. Operators must match the blade material to the plastic type. They also need to think about how rough any fillers are. For example, high-speed steel (HSS) and SKD11 are good for cutting tough or glass-filled plastics. D2 steel is hard and tough, so it works for most jobs. Carbide-tipped and powder metallurgy blades, like CPM M4, work best for fast lines and hard jobs. These special materials help the knives cut well and last longer, even in tough jobs.
Pelletizing knives also need to fit the machine brand. Big pelletizing system makers like EREMA, Gala, and NGR make their machines for certain blade shapes and materials. Operators should always check if the knife fits to get the best cuts and stop early wear.
Tip: Always check your pelletizer maker’s rules before picking blades for new or special plastics.
Precisione di taglio
Cutting precision is important for pellet quality and how much you make. The best pelletizer knife keeps close limits and makes clean, even cuts. Special measuring tools help operators check and improve cutting accuracy. The table below shows common things measured and tools used in pelletizing:
Measurement Aspect | Method/Instrument Used | Precision/Details | Statistical/Analytical Approach |
---|---|---|---|
Moisture Content | Moisture analyzer (MA50/1.R, Radwag) | Accuracy: 0.001% moisture; sample ~2 g; fivefold analysis with standard deviation reported | Variability expressed as standard deviation |
Consumo energetico | Power quality analyser (EQUA Wally) measuring instantaneous power on 3 phases | Voltage and current measured at 50 Hz frequency; mass measured by electronic scales (accuracy 0.01 g) | Energy consumption calculated by numerical integration (trapezoidal method) of instantaneous power and mass data |
Particle Size Distribution | Vibrating screen separator (LAB-11–200/UP) according to ANSI/ASAE S319.4 standard | Sieve mesh sizes: 1.65, 5.61, 8.98, 18.0, 26.9 mm; separation time 120 s | PSD fitted to models: Rosin–Rammler-Sperling-Bennett (RRSB), normal, logistic, lognormal distributions |
Mechanical Strength | Knife-edge cutting, crushing, three-point bending (from related catalyst studies) | Strength data correlated using Weibull distribution | Weibull distribution used for statistical correlation of mechanical strength data |
Knife Mill Operational Specs | Rotor speed: 2880 rpm; peripheral cutting speed: 15.39 m/s; knife blade angle: 45° | Clearance between cutting and counter-cutting edge: 1.15 mm; knives sharp | Power measured during idle and loaded states to assess cutting energy demand |
Operators use these ways to make sure pellets are always the same size and shape. High-precision blades make less waste and off-size pellets, so cutting works better.
Durata e resistenza all'usura
Durability and wear resistance show how long pelletizing knives last. Advanced materials like SKD11, HSS, and carbide-tipped steels fight wear from tough plastics and fillers. Powder metallurgy blades, like CPM 10V, last even longer for big jobs. Heat treatment and coatings, like chromium or titanium nitride, make blades harder and cut smoother.
A strong blade stays sharp and cuts well for many runs. Operators change blades less, have less downtime, and save on repairs. It is important to balance hardness and toughness. Too hard can chip, too tough can dull fast. Picking the right material helps the knife work well in any pelletizing job.
Esigenze di manutenzione
Regular maintenance keeps pelletizing knives working well. Operators should check, clean, and adjust blades on a set schedule. The table below shows how often to care for key parts in a pelletizing system:
Component | Frequenza di manutenzione | Problemi comuni |
---|---|---|
Scraper blades | Ogni 3 mesi | Blade dullness, misalignment |
Pan liner | Mensile | Wear and tear, thickness loss |
Power assembly | Annualmente | Equipment wear, lubricant loss |
Operators should also watch things like disc angle and speed to keep pellets good. Training workers to spot early wear or problems helps stop big breakdowns. Sharpening and changing blades on time keeps pellet quality high and protects the machine.
Note: Good maintenance makes pelletizers and knives last longer and helps manage materials better.
Rapporto costo-efficacia
Cost-effectiveness is more than just the price of pelletizing knives. Operators must think about how long blades last, how much care they need, and how they affect pellet quality. Special blades like carbide-tipped and powder metallurgy cost more at first, but last longer and cut downtime. This saves money by making cutting better and stopping delays.
Picking the right blade for each pelletizing system helps get the most value. Operators who choose blades for their job and materials get better pellets, less waste, and use less energy. Using good materials and caring for blades well saves even more money over time.
Picking pelletizer knives that are durable, precise, and fit your machine is the best way to save money.
Pelletizer Machine Compatibility
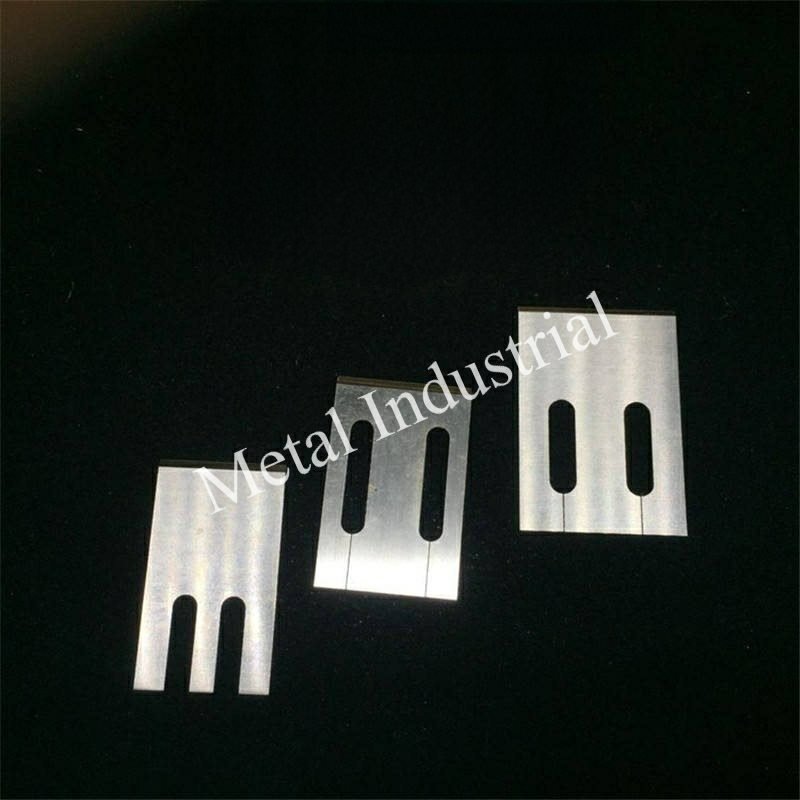
EREMA Pelletizer Blade Fit
Many people use EREMA pelletizers for recycling plastic. These machines need the right blades to work well. The erema pelletizer blade must fit the machine’s size and shape. It also needs the correct thickness and mounting holes. Operators often pick blades made from high-speed steel or SKD11. These materials are strong and stay sharp. The erema pelletizer blade makes clean cuts and less dust. This helps the pelletizer run smoothly.
A good erema pelletizer blade makes pellets more even. It also means less time fixing the machine. Users say the right blade lasts longer and stops many breakdowns. The erema pelletizer blade works well for fast production. This is important for big recycling plants. When picking a new blade, operators should check how hard it is and how smooth the edge is. Many suppliers sell erema pelletizer blades with special coatings. These coatings help the blade last longer.
Tip: Always use the machine manual when putting in a new erema pelletizer blade. This keeps the pelletizer safe and makes the best pellets.
In the future, erema pelletizer blades may use powder metallurgy and smart coatings. These new ideas help the pelletizer cut tough plastics and run longer.
Other Major Brands
Other brands like Gala, NGR, and Cumberland also make pelletizers. Each brand needs its own type of blade. For example, Gala pelletizers often use round blades. NGR pelletizers may need blades with special shapes. Operators must match the blade’s material and shape to the pelletizer and plastic type.
The table below lists popular pelletizer brands and their blade features:
Brand | Tipo di lama | Opzioni di materiale | Caratteristiche principali |
---|---|---|---|
EREMA | Straight, slanted | HSS, SKD11, carbide | High precision, long life |
Gala | Circolare | Tool steel, carbide | Fast change, smooth finish |
NGR | Custom shapes | HSS, D2, SKD11 | Abrasion resistance |
Cumberland | Rotor, stator | Alloy steel, HSS | Facile manutenzione |
Using the right blade for each pelletizer helps the machine work well. It also makes better pellets. Operators should always check the blade’s fit and material before buying. The correct blade stops extra wear and saves time.
If you want help or need specific pelletizer blades, talk to Nanjing Metal’s sales engineers Qui.
Custom Pelletizing Knives Solutions
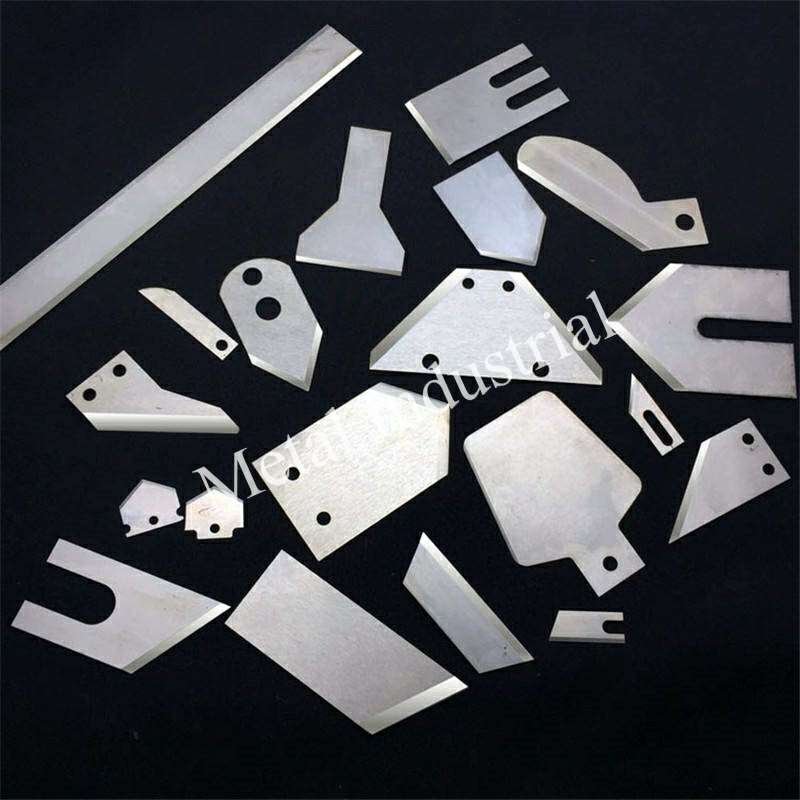
Vantaggi della personalizzazione
Custom pelletizing knives give companies a special advantage. They help make the pelletizing system work better. Every production line is different and has its own needs. Standard blades do not always give the best results. Customization lets operators pick the right blade shape, material, and surface finish for their job. This helps the system work better and makes the knives last longer.
Many manufacturers see big changes after using custom pelletizing knives. Operators notice machines run faster, pellets look better, and maintenance costs go down. The table below shows some of the clear benefits:
Performance Metric / Maintenance Practice | Descrizione | Quantitative Improvement / Benefit |
---|---|---|
Guadagni di efficienza | Machines work faster and make more pellets | Some setups reach up to 94.84% efficiency |
Bulk Density | Shows how good the pellets are | Bulk density can be as high as 0.850 g/cm³ |
Market Growth | More people are using advanced pelletizer knives | 4.5% yearly growth (2022-2030), CAGR 7.5% |
Residue Reduction by Cleaning | Cleaning helps keep knives clean | Daily cleaning cuts residue by 40% |
Knife Life Extension by Maintenance | Good care and sharpening help knives last | Knife life can be up to 60% longer |
Risparmio sui costi | Strong knives and less downtime save money | Lower repair costs and more work done |
Pellet Quality | Pellets are more even and waste is less | Pellets look the same and there is less waste |
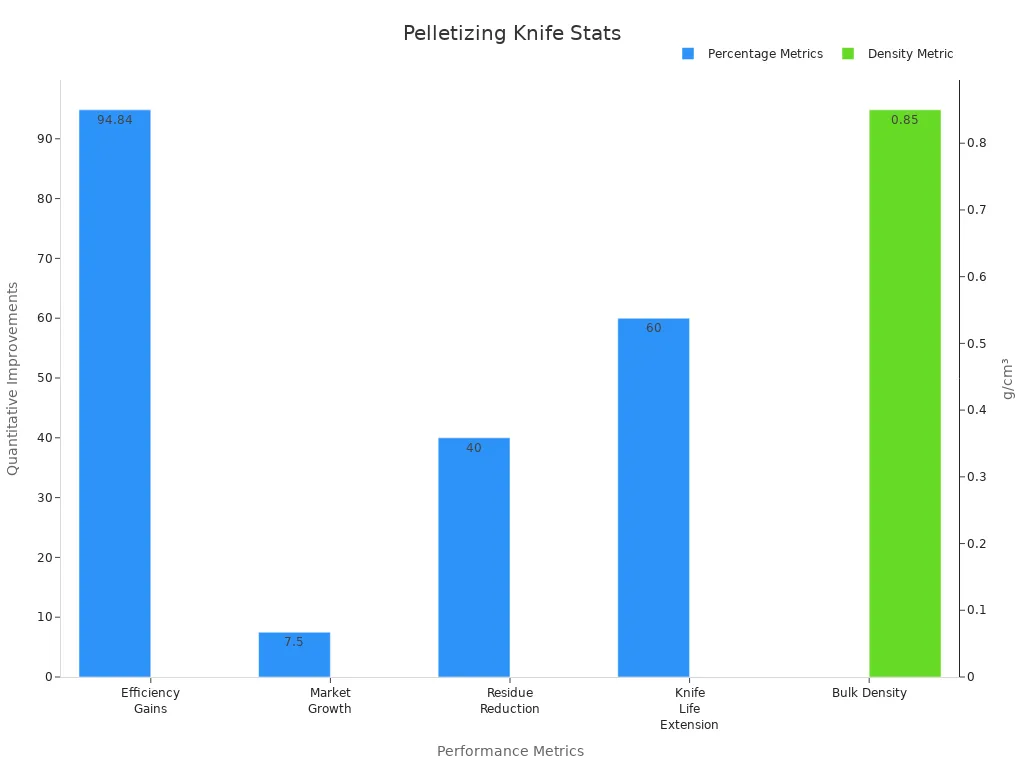
Custom blades help operators get the best fit for their system. They also help make more pellets and keep them the same size. Many companies pick custom blades when they use new materials, run machines fast, or need high quality. Customization is also good for tough jobs, like cutting rough fillers or soft plastics.
Tip: Custom pelletizing knives can help stop downtime and make the plant work better. Operators who buy custom blades often get their money back quickly.
Maxtor Metal Custom Services
Nanjing Metal, also called Maxtor Metal, is a top pelletizing manufacturer. They have over 20 years of experience. The company makes custom industrial blades for many pelletizing systems. Their team has skilled engineers and technicians who know about plastic processing.
Maxtor Metal gives full OEM and ODM services. Customers can ask for blades using drawings, samples, or specific needs. The company offers many materials, like SK2, HSS, M2, SKD11, carbide-tipped, and powder metallurgy steels. Each blade gets special heat treatment, such as quenching, tempering, and sub-zero processing, to make it last longer.
Quality control is very important at Maxtor Metal. The company checks every blade in many steps to make sure it is good. The table below shows their quality checks and what makes their production better:
Quality Control Metrics | Production Performance Data and Advantages |
---|---|
First article inspection | Skilled R&D team |
Incoming material inspection with certification | Modern production machines |
In-process quality inspection | ISO certification for steady quality and performance |
Final quality inspection | Real-time updates on production |
Total quality control in heat treatment (quenching, tempering, sub-zero treatment) | Overseas checks for clear and reliable production management |
Sub-zero treatment to enhance blade longevity and martensite structure |
Customers get real-time updates, clear production management, and easy importing. Maxtor Metal allows small orders and flexible buying choices. The company is known as a trusted pelletizing manufacturer because it cares about quality and customers.
Operators should think about custom pelletizing knives if standard blades do not work. Custom blades are best for special pelletizing setups, hard materials, or when you want the best pellets. Maxtor Metal’s skills and modern machines make them a good partner for any pelletizing job.
Maintenance for Pelletizing Knives
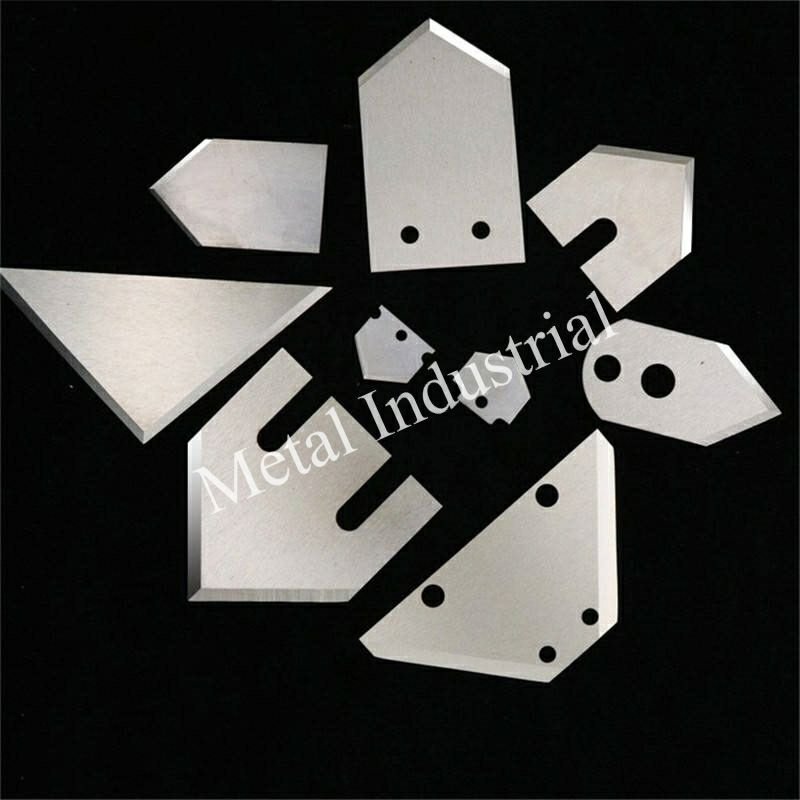
Routine Care
Routine care helps pelletizing knives work well. Operators should clean the blades after each run. Taking off plastic and dust stops buildup. This keeps the edge from getting dull. Workers need to look for chips, cracks, or uneven wear. They can use a soft brush or air to clean small spaces.
A simple checklist helps teams remember what to do:
- Wipe blades with a soft cloth.
- Look for rust or corrosion.
- Make sure bolts are tight.
- Add oil to moving parts if needed.
- Write down all maintenance in a logbook.
Mancia: Cleaning and checking the knives often makes them last longer and keeps machines running.
Sharpening and Replacement
Sharpening keeps the cutting edge sharp. Operators should sharpen knives before they get too dull. A grinding machine helps keep the right angle and smooth edge. If you sharpen too much, the blade can get weak. Workers must follow the maker’s rules.
Sometimes sharpening does not help anymore. Then, the blade needs to be replaced. Signs a blade needs changing include:
Sintomo | Cosa significa |
---|---|
Uneven pellet size | Blade edge is worn or chipped |
Increased noise | Blade is misaligned or dull |
More dust or fines | Cutting edge has degraded |
Frequent jams | Blade has lost sharpness |
Operators should always use the right part for their machine. Keeping extra knives ready helps stop delays.
Common Pelletizing Mistakes
Mancata corrispondenza dei materiali
Sometimes, operators pick the wrong blade for the plastic. This mistake makes pellets look bad and wears out blades fast. For example, a regular steel knife gets dull quickly with rough or glass-filled plastics. High-speed steel or carbide-tipped blades work better for tough plastics. Using the right blade for the plastic gives clean cuts and helps the blade last longer.
Mancia: Always check what kind of plastic you have before picking a pelletizing knife. Follow the manufacturer’s rules for the best results.
A quick table helps operators choose the right blade:
Tipo di plastica | Recommended Blade Material |
---|---|
Polyolefins (PE, PP) | D2, SKD11 |
Engineering Plastics | HSS, Carbide-Tipped |
Filled/Glass Plastics | Powder Metallurgy, HSS |
Trascurare la manutenzione
If you do not take care of pelletizer knives, they will not last long. Dull or dirty blades make pellets uneven and can hurt the machine. Operators should clean, check, and sharpen blades on a regular schedule. Checking often helps find chips or cracks early. Skipping care can cause the machine to stop and make bad pellets.
- Clean blades after every run.
- Look for damage or dirt.
- Sharpen or change blades when needed.
Regular care keeps the pelletizing process working well and helps machines last longer.
Overlooking Machine Fit
Using a blade that does not fit the pelletizer causes problems. A bad fit can make the blade shake or cut unevenly. Each pelletizer brand, like EREMA or Gala, needs special blade shapes and mounting holes. Operators must check the blade size and if it fits before putting it in.
- Make sure the blade size and holes match the machine.
- Use the pelletizer’s manual for how to install the blade.
- Test the fit before starting to make pellets.
The right fit helps the machine run smoothly and makes good pellets.
Operators who avoid these mistakes get better results and have fewer problems.
Pelletizing Knives Comparison
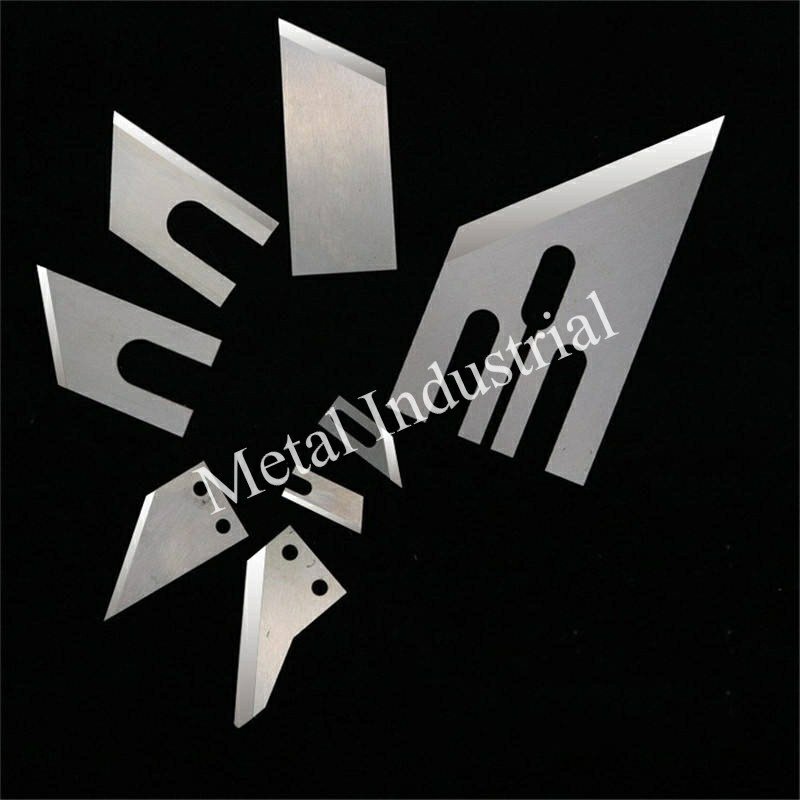
Quick Reference Table
Scegliere il giusto pelletizing knife can seem hard. Operators often look at many choices before picking one. The table below gives a quick look at common pelletizer blade types, what they are made of, and what they do best. This helps users find the right blade for their job and plastic.
Tipo di lama | Best Material Options | Suitable Plastics | Key Advantages | Typical Application |
---|---|---|---|---|
Pellettizzatore a filamenti | D2, SKD11, HSS | PE, PP, ABS, PS | Simple use, easy maintenance | Recycling, compounding |
Water-Ring Pelletizer | HSS, Carbide-Tipped | PE, PP, TPE, EVA | Good pellet shape, fast cooling | Masterbatch, large output |
Pelletizzatore subacqueo | SKD11, Powder Metallurgy | PA, PET, PBT, sticky resins | Uniform pellets, high output | Engineering plastics |
Pellettizzatore Die-Face | HSS, Carbide-Tipped | PVC, TPR, TPU | Handles sticky materials | Soft PVC, specialty blends |
Operators can use this table to see which blade works for them. Each blade type is best for certain plastics and has special benefits.
- Strand pelletizer knives are good for most recycling jobs.
- Water-ring blades are great when you need nice pellets and quick cooling.
- Underwater knives work well with tough or special plastics.
- Die-face blades are best for sticky or heat-sensitive plastics.
Mancia: Always read the machine manual and check your plastic before picking a blade. The right choice makes better pellets and keeps the machine running.
Picking the right pelletizing knives helps machines work better and saves money. Operators who use strong materials, keep blades sharp, and do regular care get many good results:
- Pellets stay the same size and look better.
- Machines stop less often and cost less to fix.
- Blades last longer with special cold treatments.
- Matching blade shape to the plastic makes work faster.
New ideas in the industry show that smart sensors and special coatings help blades last over 30% longer. If you need special help, you can Contatti Nanjing Metal’s sales engineers for advice.
Domande frequenti
What is the main function of a pelletizing knife?
A pelletizing knife cuts plastic into small pellets. These pellets are all the same size and shape. Manufacturers use them to make new plastic things or recycle old ones. The knife helps make sure every pellet looks right.
How often should operators replace pelletizer blades?
Operators need to check blades often. How long blades last depends on what plastic you use and how much you make. It also depends on how good the blade is. Most people change blades when they get dull or noisy. If pellets look uneven, it is time to replace the blade.
Which materials work best for pelletizer knives?
High-speed steel, SKD11, and carbide-tipped alloys are strong. They last a long time and do not wear out fast. These materials can cut hard plastics and rough fillers. Powder metallurgy steel is even better for tough jobs.
Can custom pelletizing knives improve production results?
Custom blades fit special machines and plastics. They help make more pellets and stop delays. Pellets look better and are more even. Many companies pick custom blades for hard jobs or new plastics.
Where can readers get expert advice or order custom pelletizer blades?
Readers can talk to Nanjing Metal’s sales engineers for help. You can ask questions or order custom blades.
Vedi anche
Lame per Granulatori a Confronto: Trova Facilmente Quella Giusta
Cosa Sono le Lame per Granulatori e Come Funzionano nell'Industria?
Come scegliere il coltello per pelletizzazione più adatto al tuo settore
Guida Completa alla Scelta della Migliore Lama Granulatrice per la Vostra Macchina